28.05.2017
Der größte jemals gefertigte konvexe Spiegelrohling
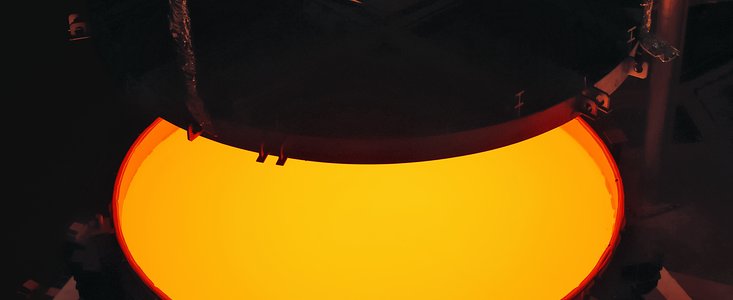
Die Firma SCHOTT in Mainz hat erfolgreich den Guss des Rohlings für den Sekundärspiegel des Extremely Large Telescope (ELT) der ESO abgeschlossen. Der fertiggestellte Spiegel wird einen Durchmesser von 4,20 Metern haben und 3,5 Tonnen wiegen. Er wird der größte jemals an einem Teleskop eingesetzte Sekundärspiegel und gleichzeitig auch der größe konvexe Spiegel sein, der je produziert wurde.
Das Extremely Large Telescope (ELT) der ESO mit 39 Metern Durchmesser wird das größte Teleskop seiner Art sein, das jemals gebaut wurde, wenn es im Jahr 2024 sein erstes Licht sehen wird. Mit dem Guss des Sekundärspiegels (M2) für das Teleskop, der größer ist als der Hauptspiegel vieler heutiger wissenschaftlicher Teleskope, ist nun ein weiterer Meilenstein auf dem Weg zur Vollendung des ELT erreicht worden.
Der Spiegelrohling ist der gegossene Materialblock — in diesem Fall aus der Glaskeramik Zerodur® [1] — die dann später in Form geschliffen und poliert wird. Im Januar 2017 hat die ESO den Auftrag für die Herstellung des M2-Spiegelrohlings an SCHOTT vergeben (eso1704). Die ESO blickt auf eine langjährige erfolgreiche Zusammenarbeit mit der Firma SCHOTT zurück, die auch schon die 8,2 Meter-Hauptspiegel und die ultradünnen Meniskusspiegel (ann12015) des Very Large Telescope am Paranal-Observatorium der ESO gefertigt hat. Als Hersteller außergewöhnlicher astronomischer Produkte auf allerhöchstem Niveau hat SCHOTT außerdem bereits die Rohlinge der deformierbaren Schalenspiegel geliefert, die den Quartärspiegel M4 des ELT ausmachen werden (ann15055). Zusätzlich wird SCHOTT auch den Rohling für den Tertiärspiegel M3 fertigen.
Der Spiegelrohling des Sekundärspiegels muss nun über ein Jahr lang einen langsamen Prozess aus Abkühlung, maschineller Bearbeitung und Wärmebehandlung durchlaufen, dann ist er bereit für den Schliff in die korrekte Form und das anschließende Polieren. Dieser Bearbeitungsschritt und die dazugehörigen Tests werden von der französischen Firma Safran Reosc durchgeführt (ann16045). Der Spiegelrohling wird dabei mit einer Oberflächengenauigkeit von 15 Nanometern (ein 15 Millionstel Millimeter) über die gesamte optische Oberfläche bearbeitet.
Sobald der M2-Spiegel fertiggestellt ist, wird er über Kopf hängend oberhalb des riesigen Hauptspiegel hängend installiert. Damit bildet er das zweite optische Element des neuartigen Fünf-Spiegel-Systems des ELT. Der Spiegel wird stark gekrümmt und asphärisch sein, was eine große Herausforderung bei Herstellung und Tests darstellt.
Endnoten
[1] Zerodur® wurde ursprünglich Ende der 1960er Jahre für astornomische Teleskope entwickelt. Es hat auch bei großen Temperaturunterschieden nur eine sehr geringe thermische Ausdehnung, ist chemisch äußerst widerstandsfähig und kann mit höchster Genauigkeit poliert werden. Viele Teleskope mit Zerodur®-Spiegeln arbeiten zuverlässig seit Jahrzehnten, unter anderem das Very Large Telescope der ESO in Chile.
+++
Bei der Öffnung der Gussform des Sekundärspiegels für das ELT
Öffnen der Gussform des Sekundärspiegels für das ELT mit der nach wie vor sehr heiße ZERODUR®-Glaskeramik während des Austemperns. Der Spiegelrohling wurde im Mai 2017 von der Schmelzanlage von SCHOTT zur 4-Meter-Austemperungsanlage von SCHOTT in Mainz transferiert. Der Guss dieses Spiegels ist ein wichtiger Meilenstein für den Bau des größten Teleskops der welt für das sichtbare ud nahinfrarote Licht, einer der größten Leistungen der ESO.
Der Sekundärspiegel des ELT während des Transports
Der glühend heiße frisch gegossene M2-ZERODUR®-Spiegelrohling für das ELT wird im Mai 2017 an der Schmelzanlage von SCHOTT in Mainz auf einen LKW-Anhänger geladen. Im Anschluss wurde er mit Schrittgeschwindigkeit und Polizei- und Feuerwehreskorte durch Mainz gefahren und kam schließlich wohlbehalten in der SCHOTT-Austermperanlage an, wo er nun langsam auskühlen wird. Danach wird er per Schiff nach Frankreich transportiert, um dort geschliffen und poliert zu werden.
+++
Nachdem der Sekundärspiegelrohling mit 4 Metern Durchmesser für das Extremely Large Telescope (ELT) der ESO erfolgreich bei SCHOTT gegossen wurde, wurde er im Mai 2017 in die Austermperungsanlage von SCHOTT in Mainz überstellt.
+++
Der Sekundärspiegel des ELT während des Transports zur Austemperungsanlage
Mit einem Gewicht von 3,5 Tonnen und einem Durchmesser von 4,20 Metern ist der M2-Spiegel der ESO der größte Teleskopsekundärspiegel überhaupt. Hier sieht man, wie der nach wie vor heiglühende Spiegelrohling vorsichtig durch Mainz zur Austermperungsanlage für 4-Meter-Spiegel transportiert wird.
+++
Der Sekundärspiegelrohling des ELT in den Straßen von Mainz
Transfer des ELT-Secondärspiegelrohlings zur 4-Meter-Austermperungsanlage von SCHOTT in Mainz im Mai 2017. Der Rohling wurde aus Zerodur® gegossen, einem Material, das ursprünglich Ende der 1960er Jahre für astornomische Teleskope entwickelt wurde. Es hat auch bei großen Temperaturunterschieden nur eine sehr geringe thermische Ausdehnung, ist chemisch äußerst widerstandsfähig und kann mit höchster Genauigkeit poliert werden.
+++
Ankunft des Sekundärspiegels des ELT an der Austemperungsanlage
Der Sekundärspiegelrohling des ELT, der frisch aus der Glaskeramik ZERODUR® gegossen wurde, bei seiner Ankunft an der 4-Meter-Austemperungsanlage von SCHOTT in Mainz im Mai 2017. Der Rohling, der zur Zeit nur ein großer Block ist, wird später zum fertigen Spiegel geschliffen und poliert.
Quelle: ESO
---
Update: 13.01.2018
.
SCHOTT begins manufacturing primary mirrors for ELT
The SCHOTT melting team has started casting the first mirror segments that will make up the 39-meter primary mirror (M-1) of the European Large Telescope (ELT). To make the segments, liquid glass heated to over 1400 degrees Celsius will be poured directly into molds, and transferred into a cooling furnace and subjected to a ceramicization process lasting several weeks.
The result is ZERODUR glass-ceramic, a material with a thermal expansion of near zero that makes it especially suited to astronomy applications. The SCHOTT production facility in Mainz is expected to complete delivery of the segments by 2024.
SCHOTT, the international technology group, will produce up to 949 identical 1.52-meter hexagonal segments for the ELT. The giant mirror will be composed of a total of 798 segments, made of ZERODUR glass-ceramic, with the balance used as replacement segments.
"Casting the mirror substrates for the M1 is a milestone in the European Southern Observatory's (ESO) project plan. The main mirror of the ELT will be humanity's largest eye on the sky, enabling us to reach unprecedented depths of space," said Marc Cayrel from ESO's ELT project team. SCHOTT has developed special casting molds for the production of the M1 segments.
"The glass consumption factor will be as low as possible, so we can work very efficiently," explains Dr. Thomas Westerhoff, Director of Strategic Marketing for ZERODUR at SCHOTT.
After ceramization, each of the round ZERODUR blocks will be cut into five slices of approximately 60 - 70 mm in thickness. Further processing at SCHOTT will take place on state-of-the-art computer-controlled 5-axis CNC machines. SAFRAN Reosc, a company based in France, will polish the M1 segments.
ZERODUR is a proven material that has been selected for four of the five high-precision mirror elements of the ELT. In addition to the segmented 39-meter giant mirror, these will be a convex mirror 4.2 meters in diameter (M2), the M3 concave mirror (3.8 meters in diameter) and a 2.4-meter diameter adaptive mirror (M4).
"Thanks to significant expansion of production capacity at the Mainz site, SCHOTT is very well prepared for the production of ZERODUR glass-ceramic, both for the ELT project and for the currently very gratifying high demand from the high-tech industry," said Dr. Thomas Westerhoff, director of strategic marketing, ZERODUR at SCHOTT Advanced Optics.
Two glass melting tanks are in parallel operation due to the high demand. Furthermore, new jobs were created for around 50 employees, and additional capacity-expanding investments are planned for the coming year.
Quelle: SD
+++
Erste ELT-Hauptspiegelsegmente erfolgreich gegossen
Die deutsche Firma SCHOTT in Mainz hat ersten sechs hexagonalen Segmente für den Hauptspiegel des Extremely Large Telescope (ELT) der ESO erfolgreich gegossen. Diese Segmente werden Teil des 39 Meter durchmessenden Hauptspiegels des ELT sein, der nach Fertigstellung insgesamt 798 Segmente umfassen wird. Das ELT wird das größte optische Teleskop der Welt sein, wenn es 2024 in Betrieb geht.
Der Hauptspiegel des Extremely Large Telescope der ESO wird mit 39 Metern Durchmesser der mit Abstand größte Spiegel sein, der jemals für ein optisches Infrarot-Teleskop hergestellt wurde. Ein solcher Spiegel-Riese ist viel zu groß, als dass er aus einem einzigen Glasrohling gefertigt werden könnte. Er wird aus 798 einzelnen sechseckigen Segmenten bestehen, die jeweils 1,4 Meter Durchmesser haben und etwa 5 Zentimeter dick sind. Die Segmente werden wie ein einziger großer Spiegel zusammenarbeiten, um mehr als zehn Millionen mal so viel Licht zu sammeln wie das menschliche Auge.
Marc Cayrel, Leiter der ELT-Optomechanik bei der ESO, war beim ersten Gussvorgang anwesend: "Es war ein wunderbares Gefühl, zu sehen wie die ersten Segmente erfolgreich gegossen wurden. Dies ist ein wichtiger Meilenstein für das ELT!"
Die ELT-Hauptspiegelsegmente bestehen wie der Sekundärspiegelrohling des Teleskops aus dem dehnungsarmen Keramikwerkstoff Zerodur© [1] von SCHOTT. Die ESO hat das deutsche Unternehmen mit der Herstellung der Rohlinge der ersten vier ELT-Spiegel beauftragt, die als M1 bis M4 bezeichnet werden, wobei M1 der Hauptspiegel ist (eso1704).
Die ersten Segmentgüsse sind sehr wichtig, da sie es den Ingenieuren von SCHOTT ermöglichen, den Fertigungsprozess und die damit verbundenen Werkzeuge und Verfahren zu validieren und zu optimieren.
Das Gießen der ersten sechs Segmente ist ein wichtiger Meilenstein, aber der Weg zum fertigen Spiegel ist lang - insgesamt müssen mehr als 900 Spiegelsegmente gegossen und poliert werden (798 für den Hauptspiegel selbst, dazu ein Ersatzset aus 133 weiteren Segmenten). Bei voller Auslastung liegt die Produktionsrate bei etwa einem Segment pro Tag.
Nach dem Gießen durchlaufen die Spiegelsegmentrohlinge eine langsame Abkühl- und Wärmebehandlungssequenz und werden anschließend in die richtige Form geschliffen und mit einer Genauigkeit von 15 Nanometern über die gesamte optische Oberfläche poliert. Schliff und Politur werden von der französischen Firma Safran Reosc durchgeführt, die auch für zusätzliche Tests verantwortlich sein wird (eso1717).
Endnoten
[1] Zerodur© wurde ursprünglich in den späten 1960er Jahren für astronomische Teleskope entwickelt. Es hat einen extrem niedrigen Wärmeausdehnungskoeffizienten, so dass sich das Material auch bei großen Temperaturschwankungen nicht ausdehnt. Chemisch gesehen ist Zerodur© sehr widerstandsfähig und kann auf einen hohen Standard poliert werden. Die die extrem glatte Oberfläche wird in der Regel kurz vor der Inbetriebnahme eines Teleskops und danach in regelmäßigen Abständen erneut mit der eigentlichen Spiegelschicht aus Aluminium oder Silber bedampft. Viele bekannte Teleskope mit Zerodur©-Spiegeln arbeiten seit Jahrzehnten zuverlässig, darunter auch das Very Large Telescope der ESO in Chile.
Quelle: ESO