18.02.2017
Bell V-280 Valor Prepping for Flight-test Program
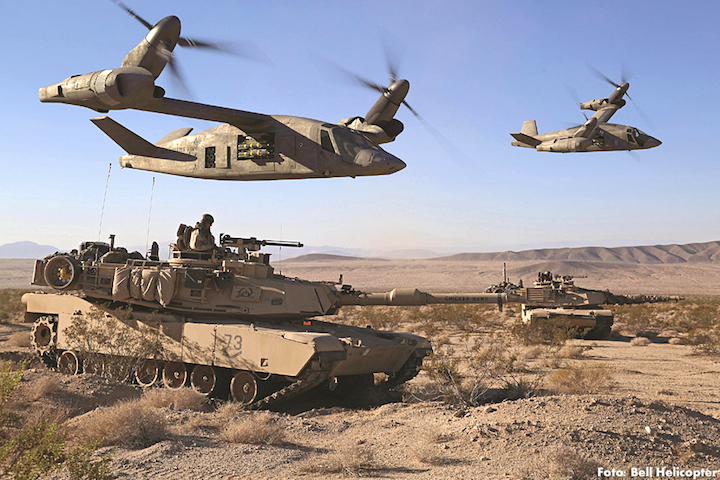
In a well-guarded hangar tucked away on the Bell Helicopter campus at Rick Husband Amarillo International Airport in Texas, a tightly knit team of dedicated technicians and engineers is putting the final touches on Bell’s next-generation tiltrotor, the V-280 Valor. If all goes as planned, the V-280, which was about 93 percent complete in late January, will fly sometime around September this year.
Designed to fulfill a requirement for new cost-effective and more efficient aircraft for the U.S. Department of Defense’s Future Vertical Lift program, the V-280 is the U.S. Army’s Joint Multi-Role Technology Demonstrator (JMR-TD), “the flagship program anchoring the Army Aviation science and technology portfolio,” according to the Army.
Bell leveraged its experience with the V-22—also built in Amarillo—in designing the V-280. Both share design features such as composite wings and other structural elements, but there are significant differences that are apparent when viewing the two aircraft. The V-22 is much larger and capable of carrying a maximum of 32 passengers plus at least three crewmembers, while the V-280 can fit 14 passengers and four crew. The Navy and Marines required a rear ramp for loading/unloading, which adds complexity and weight to the V-22, but the crew enter and exit the V-280 via six-foot-wide fuselage doors under the wings. Also adding complexity to the V-22 is the gigantic spherical bearing mounted under the center wing section and the folding proprotors, which allows the V-22 to fold into a compact and more easily stored unit. The V-280’s wing is fixed to the fuselage, and its proprotors are about a foot shorter than the V-22’s.
Perhaps the biggest difference between the two aircraft is the way the proprotors tilt. On the V-22, the engines tilt up and down to provide the craft’s unique vertical lift and horizontal flight modes. The V-280’s engines are mounted in the nacelles and do not tilt. According to Bell, “The output shaft is connected to the drive system through a spiral bevel gearbox that transfers power to the fixed gearbox and proprotor gearbox, which rotates on two big spherical bearings driven by a conversion actuator mechanism.” The V-280’s tilting gearbox design vastly simplifies the V-22’s complex hydro-mechanical clockwork that provides the necessary tiltrotor action.
The V-280’s powerplant configuration offers other advantages, explained V-280 build team manager Scott Allen. When the V-22’s engines point skyward during vertical flight, the exhaust is directed onto the landing area, and this could cause a fire, say on a grassy area, or damage a ship’s flight deck (the Navy uses protective pads under the V-22 exhaust blast). The V-280 projects only proprotor airflow downwards, while the engines remain fixed in place horizontally, eliminating the hot exhaust problem. Another benefit is that the pilot’s field of view is improved, with much less machinery blocking the view along the wings, he explained.
Allen has been involved with the V-280 JMR-TD for four years, ever since it began as a preliminary design concept. Like Bell’s new 505 and 525, the V-280 was developed in Bell’s new digital design framework, which has helped keep costs down. The V-280 wing, for example, is estimated to cost less than half that of the V-22 wing, according to Allen. Designing the drawings for one of the V-22’s hydraulic systems took 700 to 800 manhours, compared to just 40 for the V-280. “Digital designs present huge opportunities,” he said.
The program faced many challenges, but the hand-picked team of top Bell engineers and technicians has been able to solve every one.
One challenge is because of the fixed wing mounting, which means that the V-280 will have to fly out of Amarillo, as it can’t be folded up like the V-22. Because of this, Bell had to build a ground-run stand, which features large ramps for the V-280 to roll up for installation in the test rig. The Amarillo Economic Development Corporation provided a $3 million grant to Bell to build the run stand.
While Bell built the V-280’s composite wing at its own facilities, the fuselage, made of aluminum frames and composite skins, was built by Spirit AeroSystems. The fuselage could eventually be all-composite, made using Spirit’s filament-winding machines, but that would depend on the Army’s level of comfort with composite structure. “I’d love to get to zero fasteners,” Allen said.
Flight control surfaces are composite, as are the proprotors. The V-280’s wing has 22 percent of the parts count of the V-22 wing; the V-22 wing is also more complex, with some dihedral that isn’t present in the V-280’s flat wing. Like the V-22, an interconnect shaft runs in the back of the wing, allowing either engine to power both proprotors in case of engine failure.
The V-280’s landing gear configuration is also unique; basically, it’s a taildragger, with two main landing gear up front and a large wheel on the aft fuselage, and all are retractable.
The empennage is a V-tail configuration, which some observers note is not the same as early drawings of Marine Corps V-280s with downward-tilting anhedral stabilizers. “That is one potential solution, but we haven’t evaluated it yet,” said Allen.
The V-280 is equipped with its own APU, mounted toward the top of the aft fuselage, and this can power utility systems and help start the aircraft’s GE T64-419 engines, each with more than 5,000 shp. The V-280 has three hydraulic systems running at 3,000 psi (compared to the V-22’s 5,000 psi), and up to two systems can fail while the remaining system powers the fly-by-wire flight controls.
Last year, Bell demonstrated a sophisticated new cockpit concept for the V-280, a single-display touchscreen that fills the entire instrument panel. The touchscreen display has integrated night-vision and synthetic vision capabilities and allows the pilot to customize layouts of various kinds of information.
In the V-280 JMR-TD, the cockpit is more standard, with dual Lockheed Martin PFDs and MFDs and dual FMSs. The fly-by-wire collective and cyclic are a similar shape as the Bell 525’s, and they are mechanically interconnected to provide a visual cue of control movement for both pilots.
V-280 specifications include a maximum speed of 280 knots, combat range of 500 to 800 nm, maximum self-deployable range of more than 2,100 nm and 13,000+ pounds of useful load.
Quelle: AIN