.
NASA is very good about being on the cutting edge of space exploration, but it's less good about making non-cutting edge space exploration efficient and cost effective. The agency is acutely aware of this, which is why it's been trying to get commercial carriers to handle deliveries of (now) supplies and (soon) astronauts to the ISS.
The next step is for private companies to take over space station construction for (soon) Earth orbit and (eventually) deep space. To that end, NASA has selected six partner companies to develop full-sized ground prototypes and concepts for deep space habitats, with the eventual goal of deploying habitats near the moon as a stepping stone to Mars.
Five of the partners, including Bigelow Aerospace, Boeing, Lockheed Martin, Orbital ATK, and Sierra Nevada will be designing habitats that are built on Earth and launched into space on rockets. It makes sense to do this, because it's how habitats have always been sent into space. The sixth partner, NanoRacks, is teaming up with Space Systems Loral and United Launch Alliance to try something completely different: taking empty fuel tanks from the upper stages of rockets and turning them into space habitats on-orbit.
A rocket like the the Atlas V, which can deliver payloads of nearly 19,000 kg to low Earth orbit, consists of three primary pieces: on the bottom, you've got the first stage booster, which consists of a huge engine and some big tanks holding kerosene fuel and oxidizer. Above that, there's the second stage, which consists of one or two smaller engines, a big tank for storing liquid hydrogen fuel, and a smaller tank for oxidizer. The payload, which is what all of the fuss is about, sits on top.
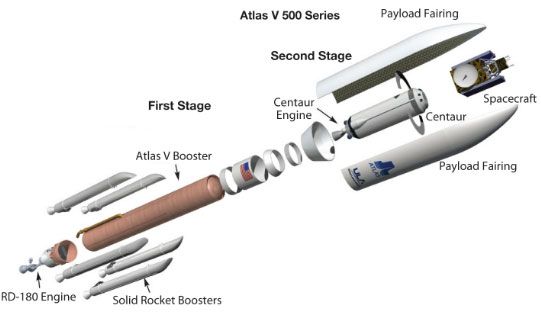
A cutaway view of the ULA Atlas V 500 Series.
The first stage launches the rocket off of the pad and continues firing for about four minutes. Once the first stage is out of fuel, it separates, and if it's a SpaceX Falcon 9, flies back home to be reused. If it's anything else, including the Atlas V, the first stage crash lands in the ocean and sinks. Meanwhile, the second stage fires up its own engine (or engines) to boost the payload the rest of the way into orbit. On the Atlas V, the second stage is called Centaur. Once Centaur gets its payload where it needs to go, it separates, and then suicides down into Earth's atmosphere.
Getting a payload into space is so expensive because you have to build up this huge and complicated rocket, with engines and guidance systems and fuel tanks and stuff, and then you basically use it for like 15 minutes and throw it all away. This is why SpaceX is trying so hard to recover the first stage of the Falcon 9. But what about the second stage? You've got a whole bunch of hardware that made it to orbit, and when getting stuff to orbit costs something like $2,500 per kilogram, you then tell it to go it burn itself up in the atmosphere, because otherwise it's just useless space junk.

NanoRacks, a company that (among other things) helps NASA with payload management on the ISS, feels like this is wasteful. And they're right. The hydrogen fuel tank on a Centaur upper stage has a diameter of over 4 meters, and an interior volume of 54 cubic meters. By way of comparison, the inflatable BEAM module that arrived at the ISS earlier this year has an interior volume of 16 cubic meters. Centaur's fuel tank is pressurized, rugged, and most importantly, already in space for free, and NanoRacks wants to leverage that to create inexpensive space habitats for humans.
The partnership that NanoRacks has formed with Space Systems Loral(they make spacecraft hardware) and United Launch Alliance (they make rockets) is called Ixion (pronounced "exeon"). NASA is funding Ixion under its Next Space Technologies for Exploration Partnerships (NextSTEP) Broad Agency Announcement to "advance commercial development of space while advancing deep space exploration capabilities to support more extensive human space flight missions in the area of space near the moon that will be the proving ground for Mars."
Here's what Ixion wants to do:
The Ixion Team is a new addition to NASA’s NextSTEP effort, and will begin by conducting a comprehensive feasibility study evaluating the conversion of rocket upper stages into habitats. This innovative approach offers a pathway that is more affordable and involves less risk than fabricating modules on the ground and subsequently launching them into orbit.
The Ixion Team proposes demonstrating this revolutionary, low-cost concept via the conversion of a Centaur rocket upper stage which will be attached to the International Space Station (“ISS”). After the converted Centaur upper stage is attached to the ISS, the Ixion Team will leverage the habitat as a proving ground for a variety of private sector activities leading to a new era in commercial low Earth orbit (“LEO”) utilization.

For more details, we spoke with Jeff Manber, CEO of NanoRacks, as well as Mike Johnson, NanoRacks' Chief Designer.
IEEE Spectrum: Can you take us through the concept that you'll be studying, reusing upper stage fuel tanks as habitats?
Mike Johnson: Most people ignore these upper stages, but they're actually very sophisticated spacecraft. They have their own guidance systems, their own propulsion, their own attitude control systems, and they have large, lightweight [propellant] tanks that can handle atmospheric pressure. [These tanks] are durable and tough: obviously, they're made to take launch loads, which is six or seven gees. Typically, the upper stage orbits with the payload that's on top of it, and eventually it gets deorbited as a piece of, at that point, space junk. But it's really a shame, because these things are huge, with this huge volume that you could use for a space station.

This is the original concept—we'd take a Centaur, add a docking hatch on it, put a Cygnus spacecraft on top of that, and staple it all to an Atlas V 500 Series rocket. We'd launch it into orbit, and then the Cygnus would take over and tug itself [and the Centaur] to the ISS. Cygnus would berth like it does normally, except it would have the Centaur upper stage hanging off the back end. At that point, we'd take the [station's] robotic arm, grapple the Centaur, and move it over to another hatch. We'd vent the [Centaur's] tank and repressurize it with air, and once that's completed, the crew could open up the hatch and start outfitting the inside of the Centaur. Basically, you get kind of a free space station module from this spent upper stage.

When we started working on the proposal for NASA, we saw that there were some additional requirements: they wanted additional docking ports, some form of airlock that could be used for crew EVAs, and an equipment airlock. You can't really put all of this on the Centaur without affecting its ability as an upper stage, so what we decided to do was put another module between the Centaur and the Cygnus: there's enough room under the Atlas V fairing to stack all this stuff up. We're not talking about making any special new hardware: it's all snapping pieces together from existing inventory.
IEEE Spectrum: Can you give us a sense of what the cost savings would be over building and launching a habitat from scratch?
Mike Johnson: At the very least, you're using one rocket to launch a spacecraft and your habitat at the same time. If you did it the normal way, you'd be using two rockets: one to launch the spacecraft, and one to launch the habitat. You know how much rockets cost. The tradeoff, of course, is how much you have to spend to outfit the second stage [as a habitat], but no matter what, the cost savings is at least one launch vehicle.
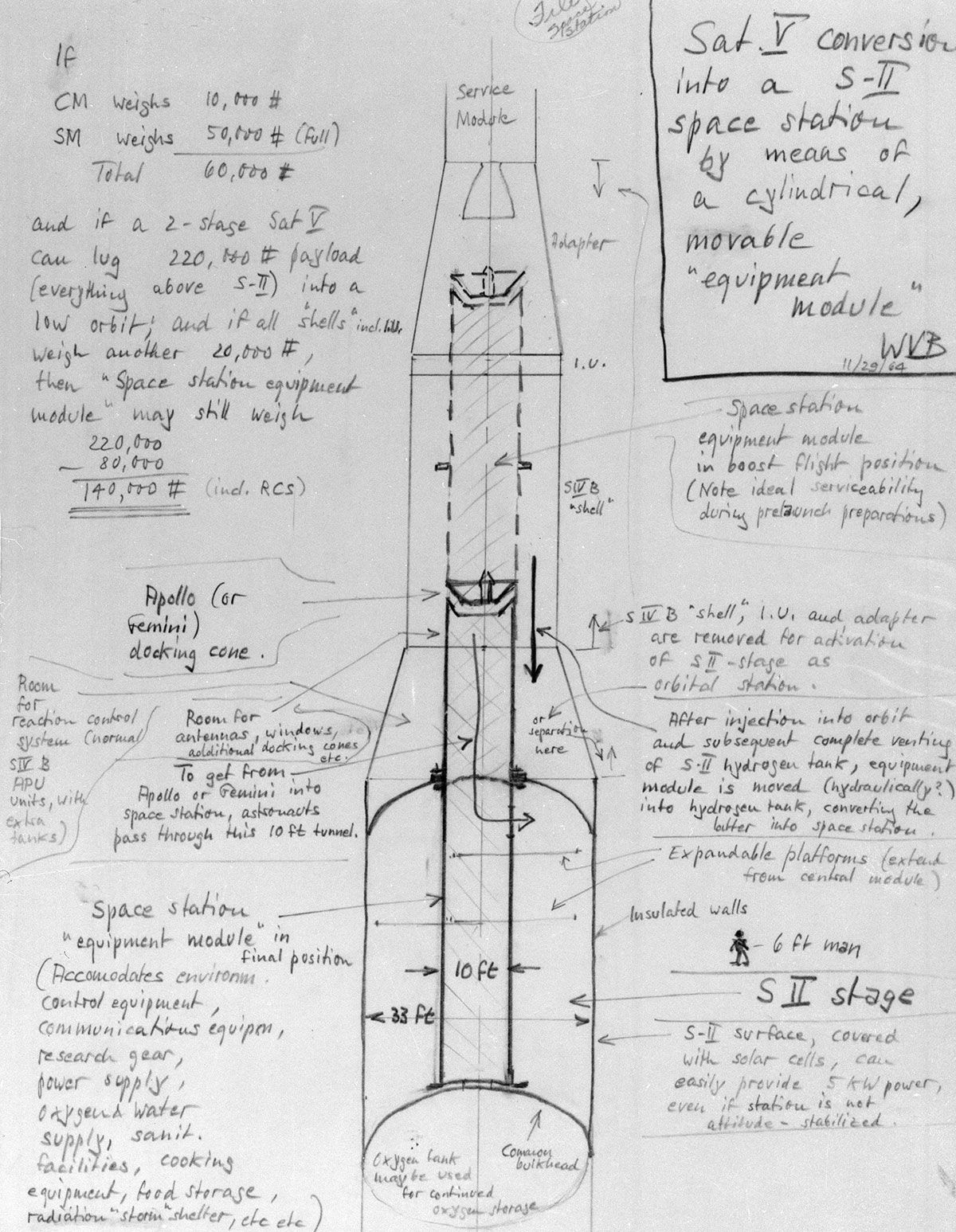
IEEE Spectrum: This is something that NASA has considered before, right?
Mike Johnson: This concept has been around for a while. In the 1960s, Werner von Braun and others proposed using an upper stage propellant tank as a habitable volume. The original Skylab concept was to use the second stage of the Saturn 1B rocket. It was going to fly up "wet" [full of fuel] and once it was in orbit and the fuel was depleted, an Apollo spacecraft would dock with it and the crew would go in and outfit the now empty propellant tank with habitation equipment.
The reason that Skylab wasn't build like this is kind of a strange story: [NASA] had fewer Saturn IBs than they had Saturn Vs, so von Braun just decided to use a Saturn V and fly up a "dry" lab, with all of the equipment aboard it already.
IEEE Spectrum: So you're saying that NASA didn't go with the idea of reusing a wet Saturn 1B stage for Skylab mostly because they had spare Saturn Vs lying around that could lift an entire dry lab all at once?
Mike Johnson: That's correct. They had extra Saturn Vs, leftovers from the Apollo program.
IEEE Spectrum: It must have been nice to have had access to leftover Saturn Vs like that, but since we don't anymore, the wet lab idea seems like it has a lot going for it. Why hasn't it been done already?
Jeff Manber: NASA, as an agency funded solely by Congress, has many objectives. Especially during the cold war, low cost was not one of the highest objectives. Other objectives included ensuring a base of talent and space expertise, and an industrial base. In that scenario, you want to build things new, and throw them away.
For fifty years, everybody allowed unmanned rockets to send up satellites, and then they threw away the rockets. And then along comes Elon Musk and Jeff Bezos, who are focused on the bottom line, and they're now reusing the first stage of the rocket. There are some inherent risks in it, but when perfected, you have a lower cost system. There was never incentive for the government to fund the development of a reusable satellite launch vehicle, but there is motivation in the commercial sector to do this.
For example, today, with the ISS, we have several launch vehicles that take cargo up to the station. They unload the cargo, we load them with the station's trash, and you then have a perfectly functional spacecraft that burns up in the atmosphere. That is counterproductive from a commercial viewpoint.
IEEE Spectrum: As SpaceX has experienced, trying to reuse hardware can be challenging. Are you concerned about the risk involved in sending an unfinished habitat into space?
Mike Johnson: One thing about spacecraft, and building satellites and building rockets, is that it's extremely risk averse. In the past, with Skylab for example, it was really easy to spend more money to build a system that was delivered ready to go. If you look at most spacecraft, everything that's built today, it's guaranteed ready to go, right away. Especially with human spaceflight, it's got to work.
In the commercial sector, it's getting interesting, because people are taking more risks. Not unnecessary risks, but acceptable risks to reduce costs. For example, when Ixion gets to orbit, we don't have a completely outfitted habitable volume yet. We have an empty propellant tank. And we have to do things to that tank to make it work. There's a trade-off, and that's what we're going to try to determine through this study: we're going to try to retire the risks, to get a low-cost working system.
IEEE Spectrum: How come you're the only group working on reusing hardware?
Jeff Manber: Much of the NEXTStep program is aimed at deep space. There, of course, it's not as clear what the commercial utilization is. The Ixion team elected to focus on a smaller part of NASA's request: the first step, which is low Earth orbit utilization that builds a robust space to allow us to go farther. I think the other five are really focused on deep space and Mars, and in that sense, we complement them.
IEEE Spectrum: NanoRacks doesn't currently work with launch vehicles or the habitation part of the ISS. Why are you interested in turning rockets into space habitats?
Jeff Manber: We're a customer-driven space company making use of the ISS. As we look around for new platforms, the U.S. has made it clear that [the ISS] is the last space station that they will operate in low Earth orbit, and they want to see a transition to commercial platforms. And so do we. We want to keep hardware costs as low as possible: it's not about building something on the ground that could cost hundreds of millions of dollars. Why do that when you have perfectly good hardware going to space, paid for already? That's what we're looking at with ULA and [SSL], at NASA's behest. In general, we see a future where we can repurpose and reuse platforms that are in space to offer our customers space services at the most economical price.
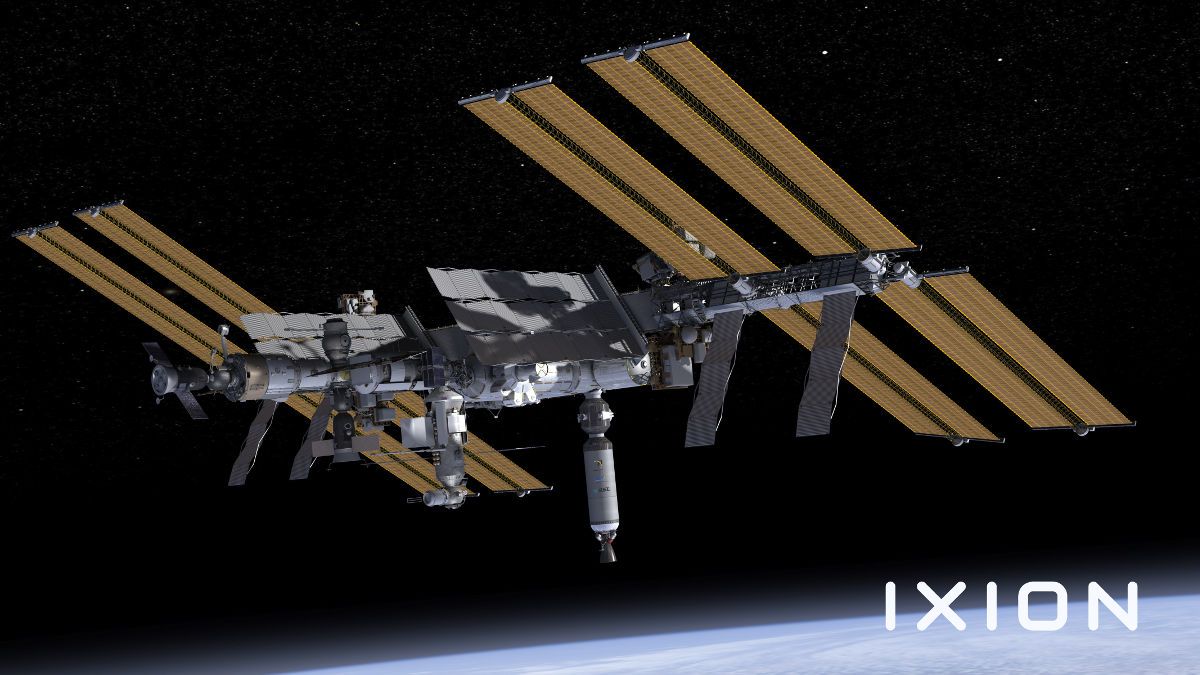
Ixion hopes that their feasibility investigation will last less than a year, and they seem confident that they'll be able to convince NASA that the project is worth taking from concept to reality. That reality could potentially involve a flying demonstrator mission within the next five years. Beyond that, there's an enormous amount of potential here: for example, Ixion is considering deploying its own space station, partially staffed by robots, to assemble and deploy commercial satellites. What's more exciting, though, is that if this concept proves itself to be viable, there's no reason it can't be extended beyond Centaur. When the SLS Block 1B launches in 2021, it'll be carrying a hydrogen fuel tank that looks something like this:
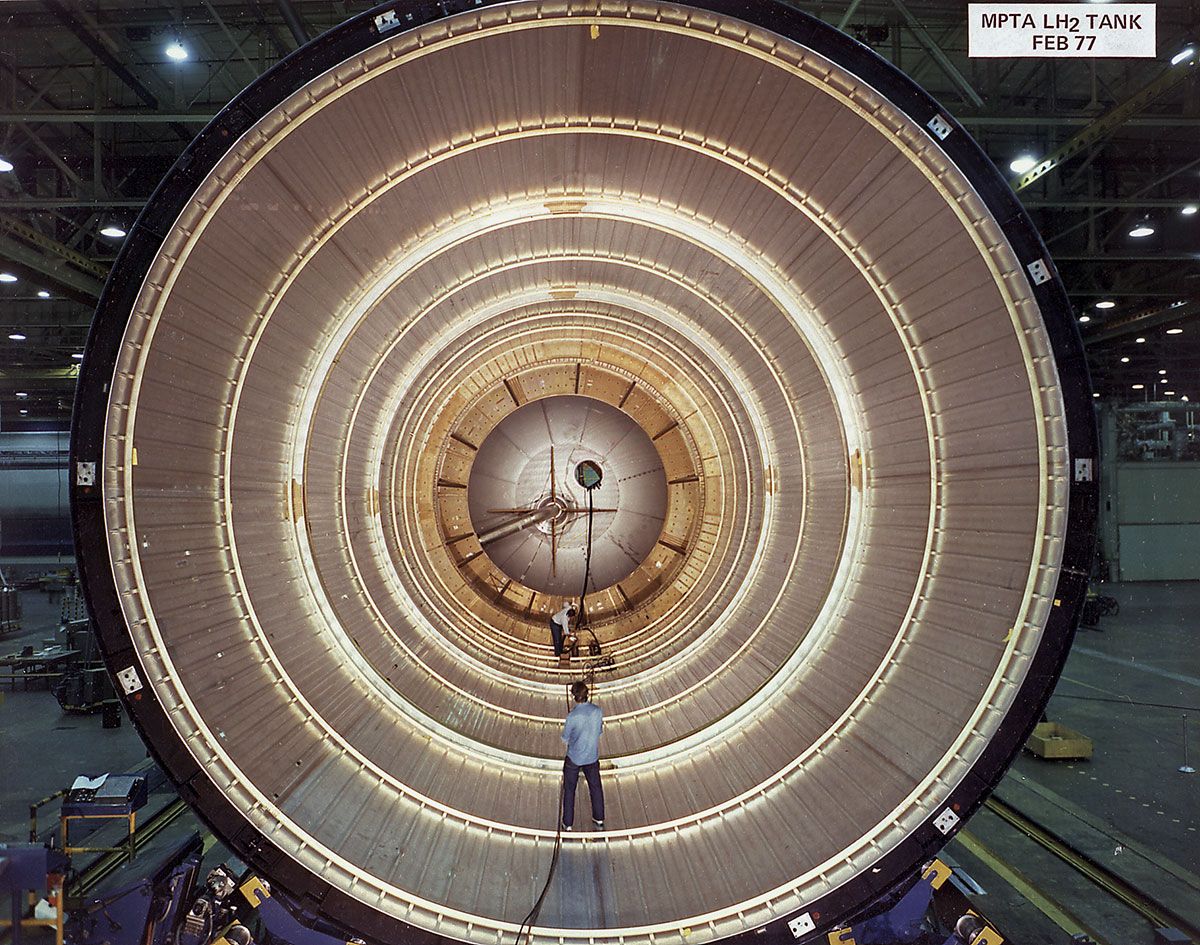
The picture shows the inside of the Space Shuttle’s external H2 tank, but the SLS Block 1B second stage tank will be the same diameter (8.5 meters), albeit only 11 meters long. Its interior volume will be a massive 495 m3, which would give you well over half the volume of the entire ISS to play with in just one single launch. Furthermore, you'd get all that volume in one enormous open space, rather than spread out through a maze of tunnel-like modules, which could enable all kinds of new science projects and hardware testing.
If we want to go back to the moon, and then to Mars, and then even farther into the solar system, we're going to have to find ways of making it affordable. NASA doesn't have Apollo-era budgets anymore, and even if it did, they're only going to spend it on the first wave. Everyone who comes after that, all people who want to turn space into a business and perhaps even into a home, are going to have to do it on their own. Ixion thinks that the best way to do that is to make use of all of the resources we have available, rather than tossing potential space habitats back to Earth like junk, and we're hoping they get a chance to prove that they can make it work.
Quelle: IEEE