.
A lid is lifted off to reveal the interim cryogenic propulsion stage test article, which is similar to the upper part of NASA’s Space Launch System. On the first flight of SLS with NASA's deep-space craft, the ICPS is the liquid oxygen/liquid hydrogen-based system that will give Orion the big, in-space push needed to fly beyond the moon before it returns to Earth.
Credits: NASA/MSFC Image: Emmett Given
-
A key piece of hardware for NASA's new rocket, the Space Launch System, completed a five-hour journey by barge June 19 along the Tennessee River in North Alabama. Fishermen may have caught a glimpse of it on its way from United Launch Alliance in Decatur, Alabama, to the agency's Marshall Space Flight Center in Huntsville, Alabama. SLS will be the most powerful rocket in the world and enable human missions to deep space, including the journey to Mars.
The transported hardware is a prototype of the interim cryogenic propulsion stage (ICPS), and will be a "big catch" for testing later this year. On the first flight of SLS with NASA's deep-space craft, the ICPS is the liquid oxygen/liquid hydrogen-based system that will give Orion the big, in-space push needed to fly beyond the moon before it returns to Earth.
The test version ICPS joins other structural test articles and simulators that make up the upper portion of the rocket. When all the hardware is completed, engineers will stack them together and move the 56-foot-tall structure to a test stand at Marshall.
"The delivery of this test hardware is critical to preparing for a big test series later this year," said Chris Calfee, ICPS project manager at Marshall, where the SLS Program is managed for NASA. "For that test series, we will subject the hardware to forces similar to those experienced in flight. This will ensure the hardware can handle the forces without compromising the structural integrity of each piece."
In addition to the ICPS, structural test articles have been completed for the:
Orion spacecraft simulator – a replica of the bottom portion of the exploration vehicle that will carry the crew to space, provide emergency abort capability, sustain the crew during the space travel, and provide safe re-entry from deep space return velocities.
Orion stage adapter -- connects the Orion to the ICPS. The adapter technology was used for Orion’s first test flight in December 2014.
Core stage simulator -- a duplicate of the top of the SLS core stage that is approximately 10 feet tall and 27 feet in diameter. The rocket's entire core stage will tower more than 200 feet tall and house the vehicle’s avionics and software, and the flight computer. It also will store cryogenic liquid hydrogen and liquid oxygen that will feed the vehicle’s RS-25 engines.
A structural test article for the launch vehicle stage adapter (LVSA), which connects the core stage and the upper stage, has completed welding and is now being outfitted with hundreds of sensors to collect test data. Engineers also are continuing work on the logistics behind such a large test operation, including building handling equipment that will transport the hardware to the test stand. "Testing is probably the most important part of building a rocket," said Steve Creech, acting director of the Spacecraft and Payload Integration and Evolution Office at Marshall. "We look forward to the test series coming up, and continuing work on flight hardware that is currently in production for the ICPS, Orion stage adapter and LVSA."
For the ICPS, Boeing modified the design of the existing ULA Delta Cryogenic Second Stage, used on United Launch Alliance’s Delta IV family of launch vehicles. It will be powered by an Aerojet Rocketdyne RL-10B engine – also currently used on the Delta Cryogenic Second Stage. Modifications to the Delta Cryogenic Second Stage include lengthening the liquid hydrogen tank, adding hydrazine bottles for attitude control and making some minor avionics changes to meet the design parameters and performance characteristics as needed by NASA to meet the flight objectives.
The Boeing/ULA team is working to complete production of the ICPS flight hardware that will launch on the first SLS flight with Orion in late 2018. “We are making great progress on the flight hardware with our ULA and NASA partners,” said Cataldo Mazzola, the Boeing ICPS test manager.
The SLS Block I configuration, the first version of SLS, will have a minimum 70-metric-ton (77-ton) lift capability and be powered by twin solid rocket boosters and four RS-25 engines. The next planned upgrade of SLS, Block 1B, will use a more powerful exploration upper stage for more ambitious missions with a 105-metric-ton (115-ton) lift capacity. Block 2 will add a pair of advanced solid or liquid propellant boosters to provide a 130-metric-ton (143-ton) lift capacity. In each configuration, SLS will continue to use the same core stage and four RS-25 engines.
.
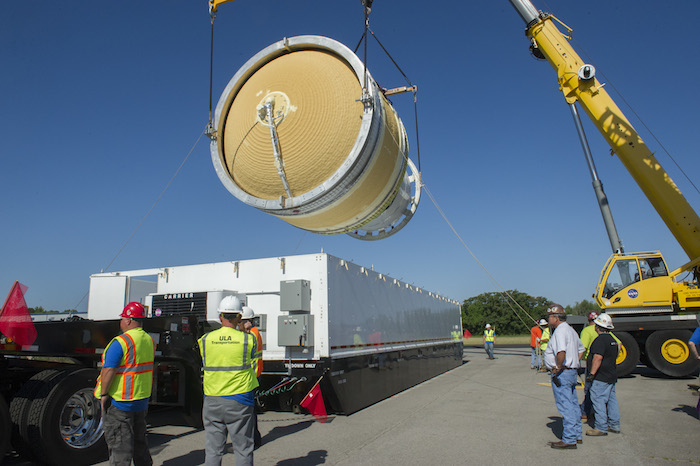
Two cranes lift the interim cryogenic propulsion stage test article, built and delivered by United Launch Alliance in Decatur to NASA’s Marshall Space Flight Center in Huntsville, Alabama. The ICPS test article joins other structural test articles and simulators that make up the upper portion of the SLS rocket. They will be stacked and tested later this year at Marshall.
Credits: NASA/MSFC Image: Emmett Given
Quelle: NASA
4296 Views