.
12.05.2016
---
Boeing’s Starliner schedule for sending astronauts into orbit slips to 2018
The hull of a CST-100 Starliner structural test vehicle is assembled inside Boeing’s Commercial Crew and Cargo Processing Facility at NASA’s Kennedy Space Center in Florida. (Credit: NASA)
-
A top Boeing executive said today that the company plans to start sending crews into orbit aboard its CST-100 Starliner space taxi in 2018, which represents a slight delay in NASA’s previous development schedule.
“We’re working toward our first unmanned flight in 2017, followed by a manned astronaut flight in 2018,” Leanne Caret, who is Boeing’s executive vice president as well as president and chief executive officer of Boeing’s defense, space and security division, said at a briefing for investors.
Previously, Boeing said both test flights, uncrewed and crewed, were scheduled for 2017. Just this week, Aviation Week reported that Boeing was sticking to the 2017 schedule, even though it’s been working through challenges related to the mass of the spacecraft and aeroacoustic issues related to integration with its United Launch Alliance Atlas 5 launch vehicle.
In a follow-up to Caret’s comments, Boeing spokeswoman Rebecca Regan told GeekWire that those factors contributed to the schedule slip. In addition, NASA software updates have added more work for developers.
.
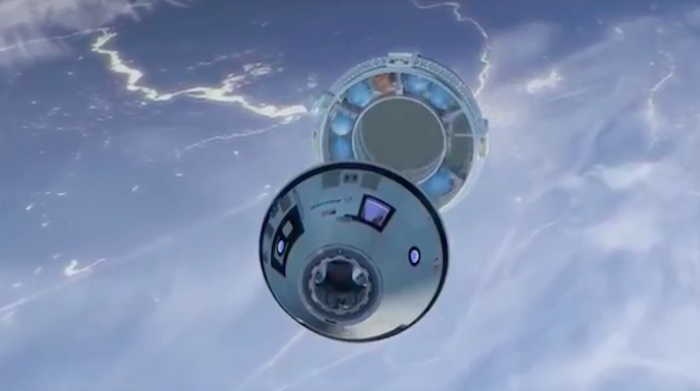
Boeing and SpaceX are building spacecraft to transport astronauts to and from the space station for NASA, under the terms of $6.8 billion in contracts that were awarded in 2014. Boeing was allotted $4.2 billion to work on the Starliner, while SpaceX is getting $2.6 billion to upgrade its Dragon cargo capsule to carry astronauts.
Each space taxi is designed to carry up to seven astronauts plus cargo, at a cost that’s less than the $81 million per seat that the Russians are charging for trips on Soyuz capsules. A smaller crew is expected to fly on the initial missions.
SpaceX conducted a pad abort test of its Crew Dragon (a.k.a. Dragon V2) a year ago. An uncrewed test flight is planned during the first half of 2017, followed by an in-flight abort test and a crewed Dragon flight to the space station later in the year.
This month, Boeing’s team bolted together a structural test version of the Starliner, which will be used to make sure the spacecraft can stand up to the rigors of spaceflight. Astronauts are already training on Starliner flight simulators, and components for the first flight vehicle will soon be put together inside Boeing’s processing facility at NASA’s Kennedy Space Center in Florida.
-
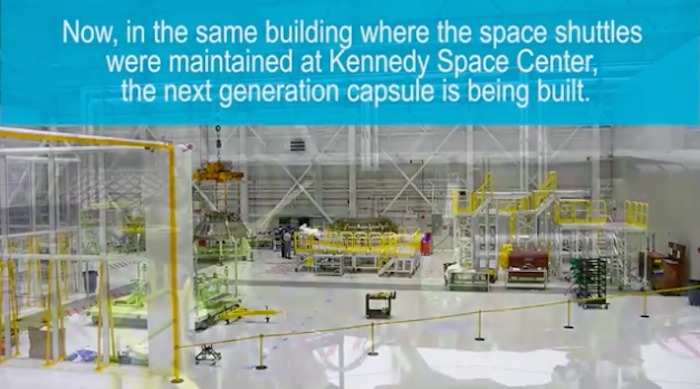
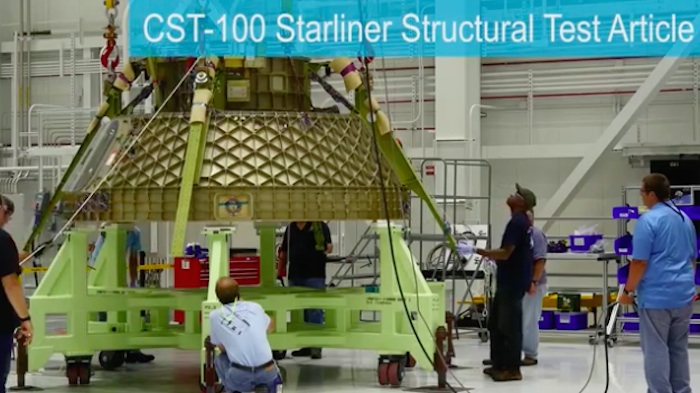
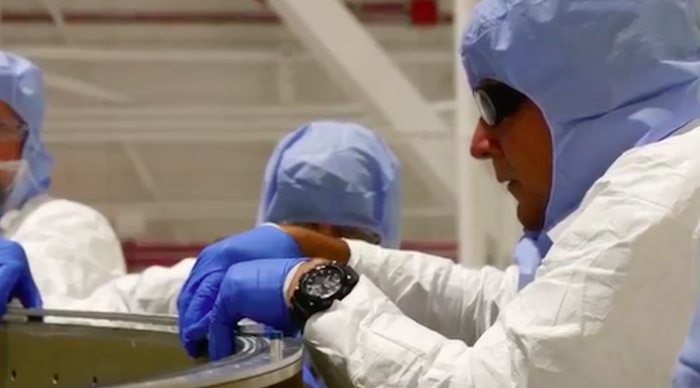
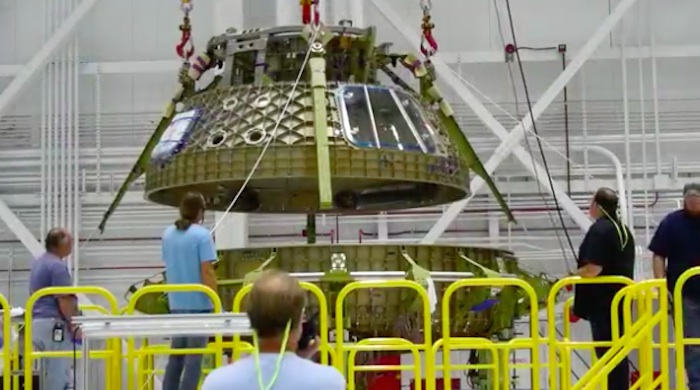
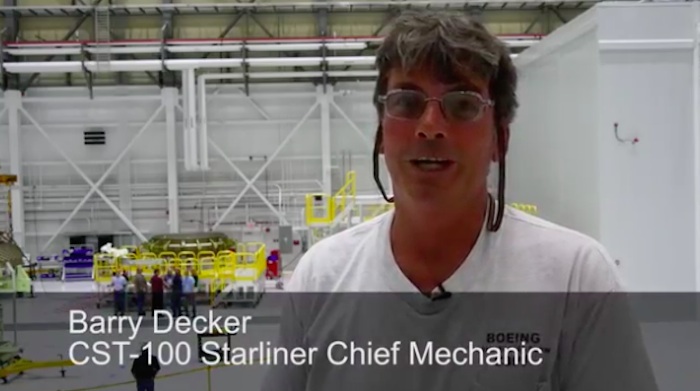
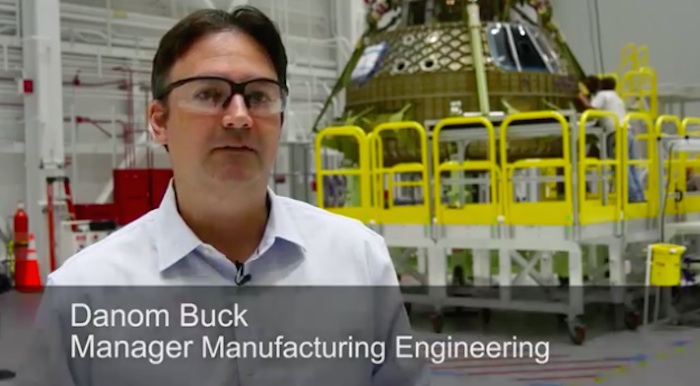
For Boeing to shift its crewed test flight from 2017 to 2018 isn’t as much of a slip as it might sound: The company’s earlier schedule had called for the visit to the space station to take place in mid-December.
However, if both companies stick to their stated schedules, SpaceX would become the first U.S. commercial venture to send astronauts to the space station – and as a result would take possession of a highly prized trophy: a U.S. flag that was left aboard the station by the last space shuttle crew in 2011.
Other news nuggets from Boeing Investor Day:
Boeing CEO Dennis Muilenburg delivered an upbeat outlook for the next five years and beyond. He said the company was aiming for a double-digit profit margin next year and had an aspirational goal of profit margins in the teens toward the end of the decade. Executives indicated that aviation services could grow to account for as much as a third of commercial airplane revenue over the next 20 years.
The head of Boeing Commercial Airplanes, Ray Conner, referred to this year’s wave of voluntary layoffs as a necessary part of the company’s strategy to boost productivity. He said the layoffs were not a defensive move. “We see productivity and cost-competitiveness as playing offense for the future,” Conner said. The reductions are expected to amount to 4,000 jobs by June, with the potential for further cuts in the latter half of the year.
Boeing has been considering the development of a new “middle-of-the-market” jet that would fill the niche once held by the Boeing 757, which is now out of production, but Conner said there’s been no decision on whether to go ahead with the plan. “Naturally we’re in continuing discussions with our customers about the market,” he said. Right now, the main focus is on the 737 MAX, which made its first flight in January and has racked up more than 3,000 orders. Conner said the first 737 MAX would be delivered to Southwest Airlines ahead of schedule, in the first half of 2017 rather than the third quarter.
Caret said Boeing was on track with flight testing for the KC-46A Pegasus tanker, which is being built for the Air Force. She touted Boeing’s work on NASA’s heavy-lift Space Launch System rocket at the Michoud Assembly Facility in Louisiana. And she threw a spotlight on the Echo Voyager unmanned undersea vehicle, which can operate autonomously for months at a time. Caret said Echo Voyager is a “game-changer” for underwater operations.
Quelle: GeekWire
-
Update: 20.05.2016
.
Airbus Defence and Space starts Orion service module assembly
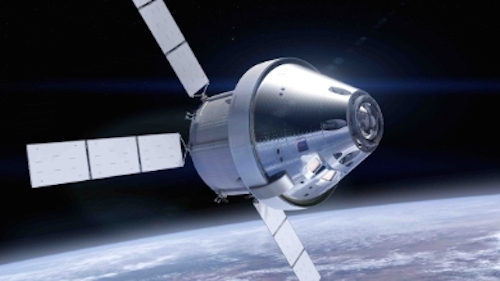
Airbus Defence and Space, the world’s second largest space company, has started assembling the European Service Module (ESM), a key element of NASA’s next-generation Orion spacecraft that will transport astronauts into deep space for the first time since the end of the Apollo program.
In November 2014, Airbus Defence and Space was chosen by the European Space Agency (ESA) as prime contractor to develop and build the ESM, which will supply propulsion, power, thermal control, air and water for astronauts on missions beyond the Moon and to Mars. The ESM sits below the Crew Module.
Integrating more than 20,000 parts and components in the ESM flight model ranging from electrical equipment to rocket engines, solar arrays, tanks for propellant and life support consumables as well as hundreds of meters of cables and tubes marks a major milestone for the Orion program. After the arrival of the flight model structure from Thales Alenia Space Italy the assembly is being carried out at Airbus Defence and Space’s site at Bremen, Germany, where officials from ESA, NASA, Airbus Defence and Space and partners gave an update on the Orion program’s progress on May 19.
“With the Orion Service Module, we are part of an historic space mission,” said François Auque, Head of Space Systems. “We will make sure this mission is a success, working hand in hand with our customers ESA and NASA and our industrial partner Lockheed Martin Space Systems.”
The second test flight of the Orion vehicle and its first atop NASA’s Space Launch System rocket known is known as Exploration Mission-1. This 2018 mission will be un-crewed and travel more than 64,000 km beyond the Moon to demonstrate the spacecraft’s performance. The first crewed mission, Exploration Mission-2, will be launched as early as 2021.
The Orion spacecraft is designed to take humans further than they have ever been before. The exploration vehicle will carry the crew to space, provide emergency abort capability, sustain the crew during space travel, and provide safe re-entry from deep space return velocities. Orion ushers in a new era of space exploration, with missions envisaged beyond the Moon, to an asteroid mass delivered to lunar orbit and Mars.
The ESM is cylindrical in shape and about four metres in diameter and in height. It features the ATV’s distinctive four-wing solar array (19 metres across unfurled) that generates enough electricity to power two households. Its 8.6 tonnes of propellant will power one main engine and 32 smaller thrusters. The ESM has a total mass of just over 13 tonnes. In addition to the main propulsion capability for the Orion spacecraft, the ESM will perform orbital maneuvering and attitude control functions. It also provides the main elements of the life support system such as water and oxygen for the crew while providing power and thermal control while it is docked to the crew module. The unpressurised service module can also be used to carry additional cargo.
Quelle: Airbus Defence and Space
-
Update: 21.05.2016
.
Europe races to meet Orion deadline
European industry has begun assembling the "back end" of the Orion crewship that is due to make an important 2018 demonstration flight around the Moon.
Orion is the next-generation vehicle that the US space agency (Nasa) will use to send astronauts beyond Earth, to destinations like asteroids and Mars.
But it needs a "service module" to provide propulsion, power, temperature control, and to carry water and air.
That job will be done by the unit now being built by Airbus in Germany.
It is an immense piece of hardware in the shape of a 4m-wide cylinder. In flight configuration, it will weigh some 13 tonnes.
"What you see at the moment is just the primary structure, but over the coming months the empty space within it will be packed," said Philippe Deloo, the top European Space Agency (Esa) official overseeing the project.
"What needs to go in is the propulsion system, the power system, the thermal system, and the consumables storage - the items that deliver water and gas to the [Orion capsule]. All have to be integrated and verified to complete the vehicle."
.
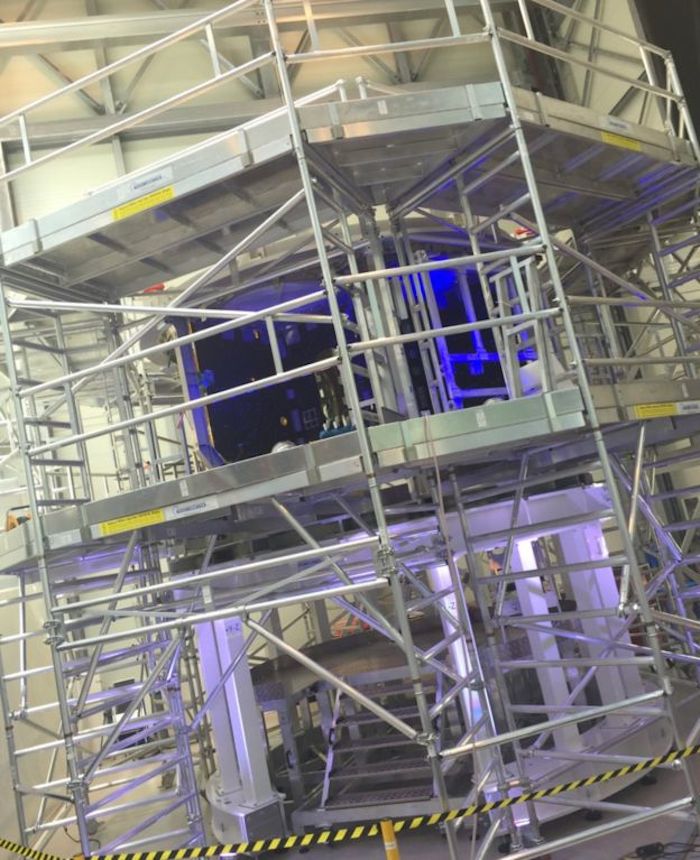
The service module is just a shell at the moment
-
This is the first time the Americans have gone overseas for a critical element of one of their astronaut transportation systems.
The key parts for Mercury, Gemini, Apollo and the space shuttles were all US-made.
"[Europe's] position on 'the critical path' has never been done before, and to be frank: we do not fly without the service module," stressed Jim Free, a Nasa deputy associate administrator.
No 'big contingencies'
Mr Free attended a ceremony in Bremen on Thursday to kick off the latest construction phase. He was joined on the American side by representatives of the Orion capsule's prime contractor, Lockheed Martin.
Airbus is hopeful of getting the completed module out the door by early 2017 - a timeline the company acknowledges will be challenging.
.
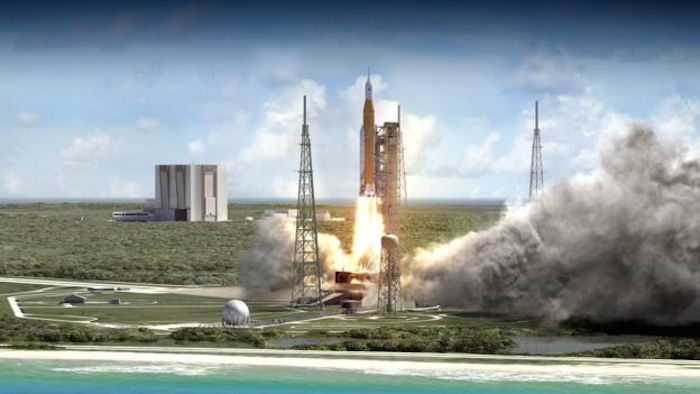
The 2018 mission will see Orion and its service module launch atop the Space Launch System rocket
-
An indication of just how much pressure everyone is under can be seen in the fact that final assembly is proceeding even before the module has had its so-called Critical Design Review.
The CDR is usually the moment when all the final drawings are signed off; no further changes can be introduced.
But Bart Reijnen, who leads the service module project at Airbus, says he is very comfortable with the current state of affairs.
"It's true you don't see this on all space programmes, but it's something we do knowing the risk we are taking, managing that risk, and burning it down in the coming days and weeks.
"We have concluded it's a viable way or we wouldn't have done it, but it doesn't allow certainly for any big contingencies in the current schedule," he told BBC News.
.
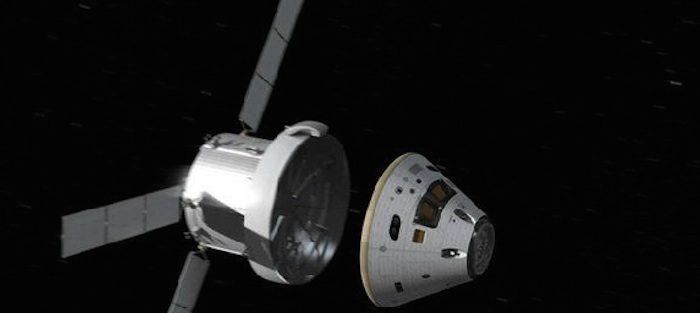
Orion has already flown once, in 2014, making a quick sweep around Earth. For that unmanned sortie, it used a dummy service module.
That will not be the case for the next outing, in 2018, when the capsule (still without a crew) will be mated to its European aft section for a three-week loop behind the Moon.
Known as Exploration Mission 1 (EM1), the venture will also witness the debut of Nasa's new "monster rocket", the Space Launch System (SLS).
This Goliath will have the muscle to hurl the mission in the direction of the Moon, but it will be the task of the European service module to maintain the correct trajectory and to make the essential engine burns required to bring the capsule safely back to Earth.
.
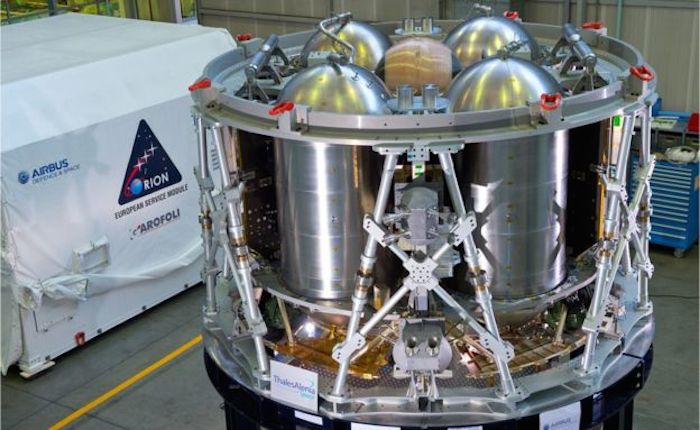
One made earlier: Airbus has already built a test version of the service module
For the moment, Europe is formally committed to making just the one module. But Esa member states will be asked in December to put the funds behind a second unit. The current, first unit was priced with Airbus at 390m euros; a second module would be used on Orion's first manned outing, EM2, a mission scheduled for "no later than April 2023".
It would be a major surprise if the member states rejected the proposal. For one thing, the first module has been given "free" to Nasa as an in-kind payment to cover Esa's costs at the space station. If Europe does not offer another module, it will have to cover those ongoing costs in some other way.
But, more than all that, Orion and the SLS are regarded by many as the future of human exploration beyond Earth, and Europe wants to be - as Esa boss Jan Woerner put it - "part of that game".
"I hope we can convince the member states as well as Nasa that we should go beyond this first flight model, for a second and maybe even more, and through that having a barter element for European astronauts flying on the SLS system," the director general added.
If European participation does become routine - and Nasa is talking about one or two flights per year eventually - then an industrial role in the service module will likely have to be found for the United Kingdom. It only recently joined Esa's human spaceflight programme, and has no components in the first vehicle.
But it is entitled to some sort of manufacturing return on its Esa investment.
Agency and Airbus officials said on Thursday they were already looking at how that "juste retour" could be fulfilled in the future.
Quelle: BBC
-
Update: 26.05.2016
.
Orion Service Module Testing Sounds Off
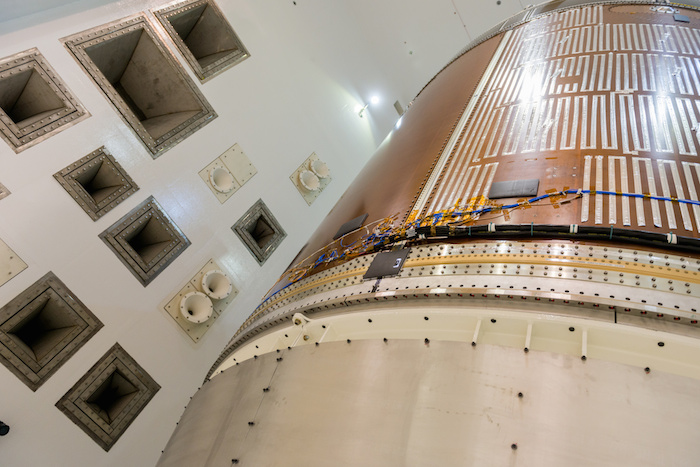
This image shows a close-up view of the structural representation of Orion's service module which was recently tested in the Reverberant Acoustic Test Facility at NASA Glenn's Plum Brook Station in Sandusky, Ohio.
Replicating the thunderous noise of a rocket launch is no easy task, but engineers at NASA Glenn’s Plum Brook Station in Sandusky, Ohio are mimicking the launch environment the Orion spacecraft will experience on a 2018 mission beyond the moon. They recently concluded a series of tests on a structural representation of the Orion service module to help ensure it can withstand the force and pressure of the acoustics environment it will experience as it makes its way from the launch pad to space atop NASA’s Space Launch System rocket.
Orion’s service module is a critical piece of the overall spacecraft. Provided by ESA (European Space Agency) and built by Airbus Defence & Space, the 13 ton component will be responsible for propelling, powering and cooling the vehicle, as well as providing air and water for its eventual crew.
When a powerful rocket launches, it can produce noise of up to 180 decibels, levels so high that it can vibrate and damage spacecraft components if they aren’t designed and built to be strong enough to withstand the environment. For comparison, a person standing about 325 feet away from a jet taking off would experience approximately 130 decibels of sound pressure, and for every additional 10 decibels, sound intensity increases 10-fold.
While engineers have designed Orion components to endure a range of harsh environments like launch and missions in space, testing on the ground helps to validate computer modeling predictions.
“Orion is undertaking an unprecedented mission, so the acoustics testing we’ve done is helping us make sure the service module will fare as we expect it to,” said Aron Hozman, lead engineer for the acoustics testing campaign.
Engineers performed numerous evaluations at different decibel levels over the course of several weeks in Plum Brook Station’s Reverberant Acoustic Test Facility. The facility is the world’s most powerful spacecraft acoustic test chamber. In it, a series of modulators or horns embedded on one of the facility’s walls and supporting subsystems such as a gaseous nitrogen generation system and a hydraulic supply system were used to modulate noise and produce a wide range of acoustic spectrums.
The series of testing was done in two configurations – one with “wet” tanks where the service module’s propellant tanks were filled with a simulant that modeled the density of Orion fuel, and with them empty to determine if the noise affected the structure differently. The maximum test with fuel simulant lasted approximately three minutes. Engineers also used the testing to help qualify the service module’s solar array wing. They placed a microphone inside the test article and determined that the noise in the test chamber matched the expected acoustic environment inside the service module where the wing is housed.
The service module structural test article will next move to Plum Brook Station’s Mechanical Vibration Facility, a powerful spacecraft shaker system that will help assess the component’s ability to withstand the tremor that an SLS launch will produce. As these ground tests continue to validate the service module’s design, the first flight unit service module for EM-1 is now being built in Europe. This unit, which will be built by the same teams who built the structural test article, recently arrived to Airbus’ facility in Bremen, Germany for integration. It is expected to be shipped to the United States in 2017.
Quelle: NASA
.
Update: 6.06.2016
.
Second Starliner Begins Assembly in Florida Factory
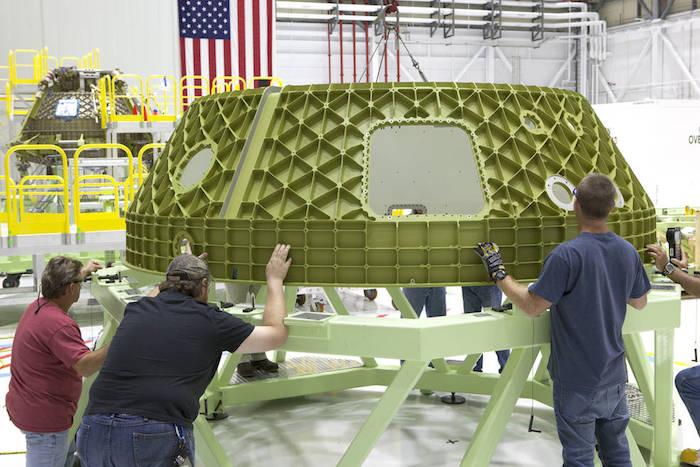
Technicians lower the upper dome of a Boeing Starliner spacecraft onto a work stand inside the company’s Commercial Crew and Cargo Processing Facility at NASA’s Kennedy Space Center in Florida. The upper dome is part of Spacecraft 1, a Starliner that will perform a pad abort flight test as part of the development process of the spacecraft in partnership with NASA’s Commercial Crew Program. In the background is the Starliner Structural Test Article.
Credits: Photo credit: NASA/Dimitri Gerondidakis
.
Another major hardware component for Boeing's second Starliner spacecraft recently arrived at the company’s assembly facility at NASA's Kennedy Space Center in Florida. The upper dome – basically one half of the Starliner pressure vessel – arrived at the Commercial Crew and Cargo Processing Facility, closely following the arrival of the lower dome and docking hatch in early May.
The three components will be outfitted separately with wiring and lines, avionics and other systems before the pieces are connected to form a complete Starliner the company is calling Spacecraft 1. From there, it will be outfitted with electrical and fluid systems before engineers will attach the outer thermal protection shielding and the base heat shield that will protect the crew during re-entry.
The upper and lower domes are distinctive with the honeycomb pattern machined into the aluminum to reduce weight and increase strength to handle the flight stresses. The domes are created using a weldless spin forming process that is then machined into the honeycomb pattern.
Later, engineers will use bolts to connect the upper and lower domes for final outfitting. It takes a team of Boeing suppliers across the country to develop the domes before they arrive in Florida, including Spincraft based in North Billerica, Massachusetts, performing the spin-form work, Janicki Industries in Layton, Utah, machining the lower domes and Major Tool & Machine in Indianapolis machining the upper domes.
This vehicle will be the first Starliner to fly in the company’s pad abort test to prove the launch abort system planned for the spacecraft will be able to lift astronauts away from danger in the event of an emergency during launch operations. The test is planned to occur prior to true flight tests of the Starliner atop a United Launch Alliance Atlas V rocket.
NASA's Commercial Crew Program contracted Boeing to build the Starliner as part of the effort to return America's ability to launch crews to the International Space Station. The agency also selected SpaceX to build that company's Crew Dragon which will also deliver astronauts to the space station.
Currently, only Russian Soyuz spacecraft are able to take astronauts to the orbiting laboratory where research is under way in numerous disciplines that will improve life on Earth and to understand and find solutions for the challenges that astronauts will face in the future on deep space missions.
The work on this Starliner is beginning as the Boeing team finalizes construction of the first Starliner, a structural test article that will be used for ground testing. The NASA and Boeing teams will compare test results to the requirements and expectations for the spacecraft as it nears flight tests with and without crew members aboard.
After completion of assembly at Kennedy, the structural test article will be shipped to Huntington Beach, California, where it will be subjected to numerous structural tests including a modal survey, critical load conditions, structural integrity, ordnance-actuated shock levels and the performance of the system that will separate the crew module from the service module.
Thermal, vacuum, and electronic interference chambers will be used to evaluate aspects of the Starliner's ability to withstand the rigors of flying astronauts in the hazardous environment of low-Earth orbit. The service module for the test article was shipped at the end of May to Huntington Beach and is expected to be joined by the spacecraft in June.
The service module, which is discarded at the end of the mission just before the Starliner and crew descend into Earth's atmosphere and land, holds propellant tanks along with the four large launch abort system engines that will push a Starliner and its astronauts out of danger in the unlikely event of an emergency during launch countdown or on ascent into space.
Starliners will fly into space aboard Atlas V rockets built by United Launch Alliance. Space Launch Complex 41 at Cape Canaveral Air Force Station, a few miles south of the Starliner assembly building, is being modified to host astronauts to enter the spacecraft and their ground support team ahead of a launch.
The Crew Access Tower's main structure is complete and the Crew Access Arm will be installed later this year. Boeing is targeting 2017 for an uncrewed orbital flight, then a flight test with astronauts in early 2018 that will dock with the space station before returning to Earth.
.
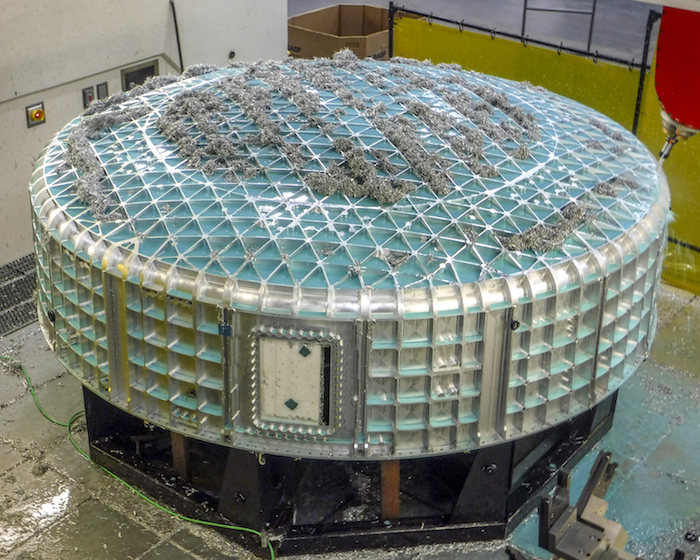
One of the lower domes for Boeing’s CST-100 Starliner spacecraft is machined to create 1,500 pockets in the formed blank of space-grade aluminum alloy. The pockets required hundreds of machining hours and leave the domes with a honeycomb pattern that reduces weight but preserves the structure's strength.
Credits: Janicki Industries
.
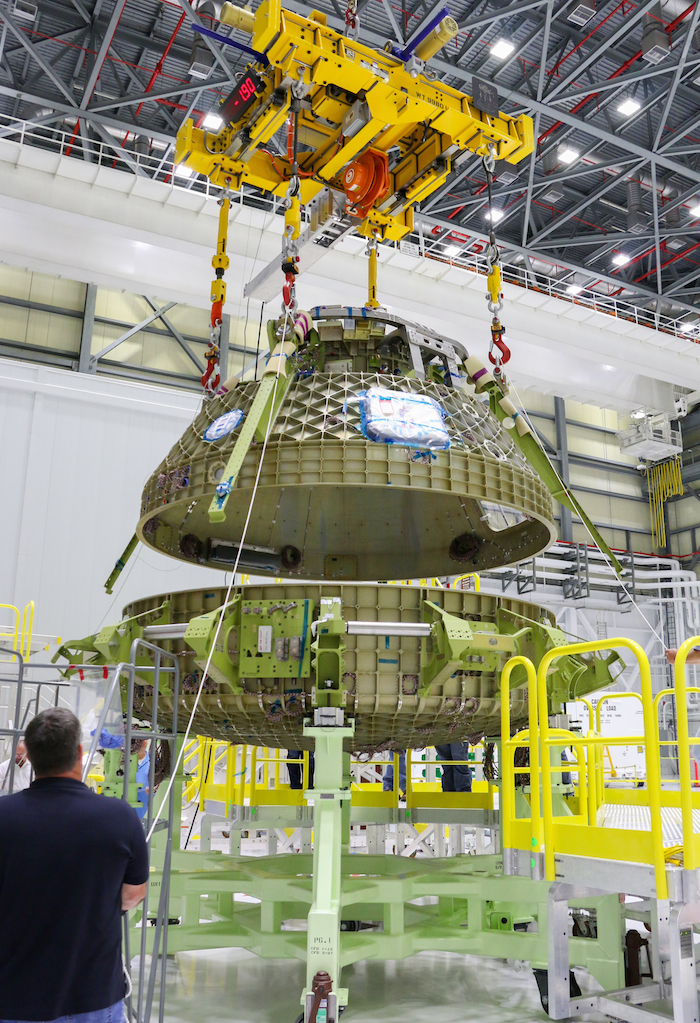
The upper and lower domes of the Starliner structural test article are joined inside the Commercial Crew and Cargo Processing Facility.
Credits: Boeing
.
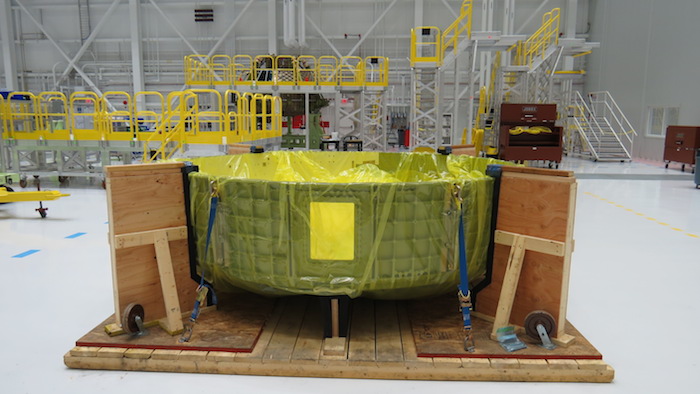
The lower dome of the Starliner's Spacecraft 1 assembly as it arrived in Florida for manufacturing.
Credits: Boeing
Quelle: NASA
6105 Views