.
4.03.2016
Test Dummies to Help Assess Crew Safety in Orion
NASA engineers install a male and female test dummy into a water landing Orion test article. Test dummies are used to collect data on the impact astronauts could experience when splashing down in the Pacific Ocean during a NASA space mission.
Credits: NASA/David C. Bowman
-
Engineers at NASA's Langley Research Center in Hampton, Virginia, are preparing for a series of water-impact tests to evaluate the Orion spacecraft and crew safety when they return from deep-space missions and touch down on Earth’s surface.
After venturing thousands of miles beyond Earth, Orion will splash down in the Pacific Ocean off the coast of California. At Langley, engineers are preparing to mimic various mission finale scenarios this year by dropping a mockup of Orion, coupled with the heat shield from the spacecraft’s first flight, into Langley’s 20-foot-deep Hydro Impact Basin. NASA is building Orion to launch atop the world’s most powerful rocket, the Space Launch System (SLS), and carry astronauts to deep space destinations, including on the journey to Mars.
“We are excited about this testing because we’ll have suited-up test dummies inside the capsule,” said Ellen Carpenter, Langley project manager. “Including test dummies will help NASA ensure the crew is protected from injury during splashdown in future missions.”
Water-impact testing will help NASA evaluate how the spacecraft may behave when landing under its parachutes in different wind conditions and wave heights. Langley has already conducted dozens of splash tests with a less sophisticated capsule mockup, but this is the first time it will assess the higher fidelity Orion ground test article.
Two test dummies – one representing a 105-pound woman and the other a 220-pound man to assess the impact on different-sized people – have been installed in the crew seats of the Orion mockup.
“These test dummies are the same type of test dummies that are used in the automotive industry for front collisions,” said Rick Ybarra, test engineer at NASA’s Johnson Space Flight Center.
Each dummy was lifted and then manually installed into the interior of the capsule. Prior to installation, engineers placed tiny sensors inside the test dummies, which will be used to help NASA understand the loads the crew could experience when returning from deep space destinations.
Within the next few weeks, engineers will apply a waterproof coat to the capsule and complete final sensor checks with a data acquisition system. The capsule itself is wired with sensors that allow engineers to collect data during the water-impact testing.
“Preliminary work is key to a successful drop,” Carpenter explained. “It allows the sensors to be verified ahead of time, so that the most accurate test data can be acquired.”
Engineers will start the series of nine drop tests in early spring. During the first three tests, engineers will drop the capsule vertically at different angles into the basin. For those tests the dummies won't be equipped with suits and helmets. After the third test, the dummies will be outfitted with spacesuits and helmets. After the four vertical tests are completed, the capsule will undergo a series of five swing tests. The dummies will remain in the seats fully suited for those.
According to Carpenter, collecting data on the dummies with and without suits allows engineers to make comparisons, which will aid in the computer modeling of Orion’s splashdown.
“The suit has some influence on how the body responds to the loads,” added Langley project engineer Jim Corliss. “Imagine you have a helmet on your head that has some weight to it. Lateral loads contribute to throwing your head side to side so there’s an advantage to understanding how the test dummies respond with and without the helmet.”
Water-impact testing is one of many steps required to ensure Orion will meet the demands of sending humans to deep space for the first time and in the future on the journey to Mars.
During Orion’s next mission, Exploration Mission-1, the uncrewed spacecraft will launch atop the SLS, travel more than 40,000 miles beyond the moon and return at speeds up to 25,000 mph.
.
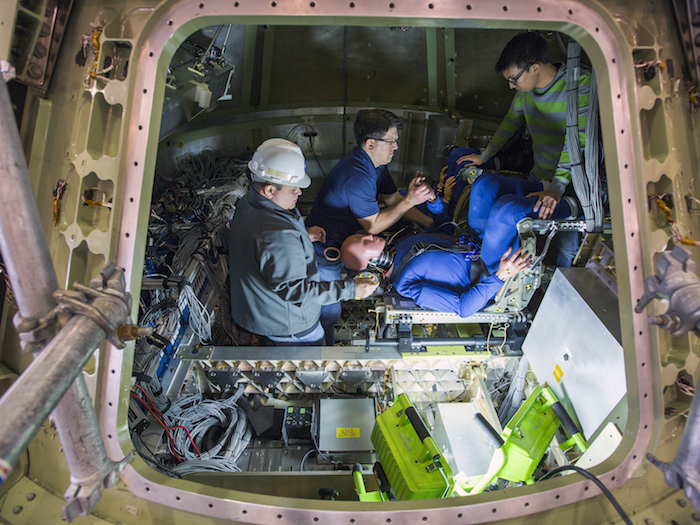
Engineers at NASA’s Langley Research Center in Hampton, Virginia, install test dummies into the crew suits of an Orion test article. The capsule, coupled with the heat shield from the spacecraft’s first flight, will be used for water-impact testing to simulate what astronauts would experience when landing in the Pacific Ocean during a real mission.
Quelle: NASA
-
Update: 15.04.2016
.
Space Treasures in the Rockies: Inside Lockheed Martin Spaceship Factory
.
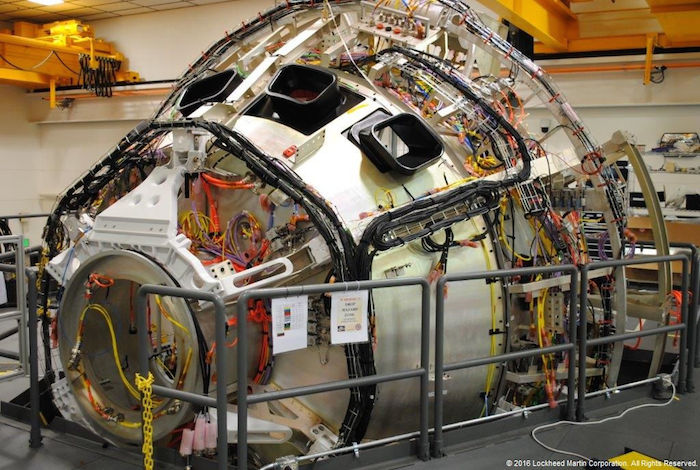
At the Lockheed Martin facility in Littleton, Colorado, scientists and engineers are working on the software and computer hardware that will operate on NASA's Orion spacecraft. Here, the front end of a mock Orion capsule at the Lockheed Martin facility. The company is currently conducting tests for Orion's Exploration Mission 1 (EM-1), when the spacecraft will fly (with no humans aboard) on a test flight around the moon.
Credit: Lockheed Martin
-
LITTLETON, CO. — The Lockheed Martin facility in Littleton, Colorado, is overflowing with NASA projects, including the Orion space capsule, a possible lunar habitat and the Osirus Rex probe that will return a sample from an asteroid to Earth.
I had the chance to visit the facility while I'm in Colorado for the National Space Symposium. Lockheed's Littleton, Colorado, campus is nestled between a small mountain range and a ridge of steep rock formations. Wildlife prowls the area, regularly sharing the space with employees.
Inside the many buildings that dot the massive campus (one employee told me the company owns 4,600 acres in total), Lockheed Martin is working on lots of space missions. The company is building the software and computer hardware for Orion, which could one day help send astronauts to the moon and Mars.
In addition, Lockheed is doing some early work on a habitat that would orbit the moon, and provide a sort of way station for people going to the lunar surface or beyond. And the company is getting ready to launch a space probe that will capture a sample of material from the surface of a comet, then bring it back to Earth.
Orion, NASA's next ship
.
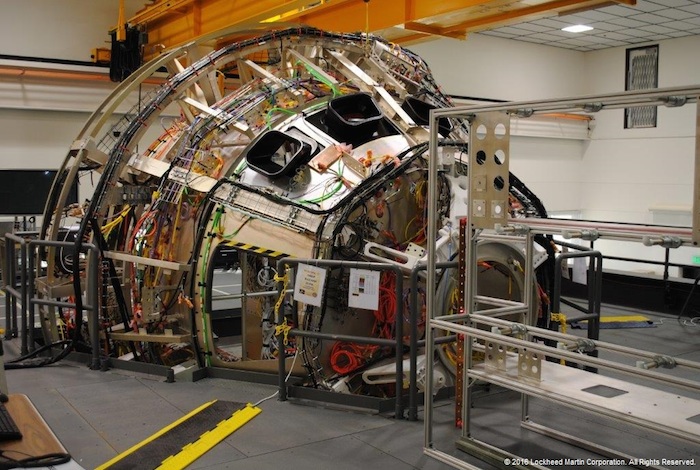
The front end of a mock Orion capsule at the Lockheed Martin facility in Littleton, Colorado.
Credit: Lockheed Martin
The Orion space capsule is NASA's next planned human spaceflight vehicle. The software that runs all the systems on Orion — all the diagnostics for the ship and the life support — is being designed and built at Lockheed Martin, along with the computer hardware for the spacecraft.
Larry Price, Orion deputy program manager at Lockheed Martin, said there are over a million lines of code in the Orion software, and 250,000 pieces of the spacecraft that are monitored.
The team at Lockheed has a mock-up of the spacecraft that they use to test the software and hardware, to work out bugs and to make sure the various pieces come together and function as a whole. Visitors to the site have to wear jackets that diffuse static electricity, which in the dry Colorado air can create quite a strong charge that could affect the electronics on the mock spacecraft.
The setup at Lockheed Martin allows the people there to run the system as if it were actually operating during a mission to space. They're currently running real-time tests of Orion's unmanned Exploration Mission 1 (EM-1) mission, scheduled for November 2018. For the first crewed missions, Lockheed will have astronauts come and potentially spend hours doing a run-through of the mission, once again to make sure bugs in the system get worked out.
For Orion's Exploration Flight Test 1 (EFT-1), in December 2014, Price said there were 600 contingency plans in place. If any part of the system had failed, the team had a plan in place to deal with the problem. Price said the only thing that went wrong was that an external camera shut down due to high radiation, so the Lockheed Martin team got to execute at least one of those contingency plans they had worked so hard to prepare.
Living around the moon
.
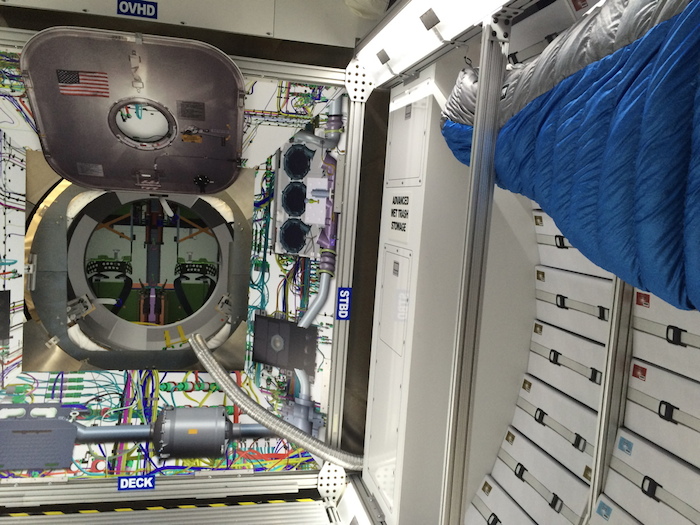
Inside the orbiting lunar habitat mock-up built by Lockheed Martin. The hatch on the left would lead into the Orion spacecraft cockpit. The blue thing on the right is a sleeping bag. Food and other supplies would line the walls of the habitat.
Credit: Calla Cofield/Space.com
-
As part of NASA's Next Space Technologies for Exploration Partnerships (NextSTEP) program, Lockheed is starting to investigate technologies to be used in a space habitat that would be positioned in orbit around the moon. The habitat could launch with an Orion spacecraft and fly with it to the moon, and could support four astronauts for 30 to 60 days.
A mock-up of the habitat at the Lockheed facilities seems like a fairly cramped space to spend a month or two with three friends, but of course this has always been one of the trials of traveling to space. Food and supplies are strategically packed around the outside of the habitat, and the packaging would actually serve as an additional layer of radiation protection, Lockheed Martin representatives said. Sleeping bags attached to tethers around the walls would create floating sleep spaces.
Quelle: SC
.
Update: 18.04.2016
.
Welding Wonder Completes Hardware for First Flight of NASA's SLS Rocket
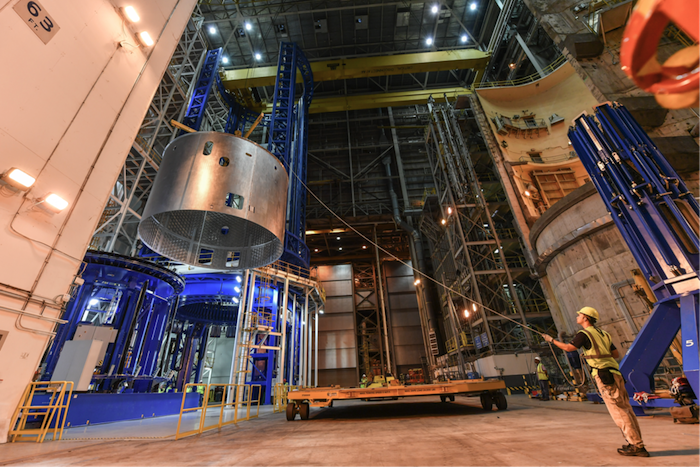
Flight hardware for the core stage of the world's most powerful rocket, NASA's Space Launch System, finishes final welding and is moved off the 170-foot-tall Vertical Assembly Center at the agency's Michoud Assembly Facility in New Orleans. The hardware is for the engine section, and is the first major SLS flight component to finish full welding on the Vertical Assembly Center. The engine section is located at the bottom of the rocket's core stage and will house the four RS-25 engines for the first flight of SLS with NASA's Orion spacecraft in 2018. The SLS core stage will stand at more than 200 feet tall and store cryogenic liquid hydrogen and liquid oxygen that will feed the launch vehicle’s RS-25 engines. A qualification version of the engine section, which also has completed welding on the Vertical Assembly Center at Michoud, will be shipped later this year to NASA's Marshall Space Flight Center in Huntsville, Alabama, to undergo structural loads testing on a 50-foot test structure currently under construction. All welding for the core stage of the SLS Block I configuration -- including confidence, qualification and flight hardware -- will be completed this summer. Traveling to deep space requires a large vehicle that can carry huge payloads, and SLS will have the payload capacity needed to carry crew and cargo for those exploration missions, including Mars.
Quelle: NASA
-
Update: 26.04.2016
.
Booster Segment Answers 'Casting' Call for First Flight of SLS
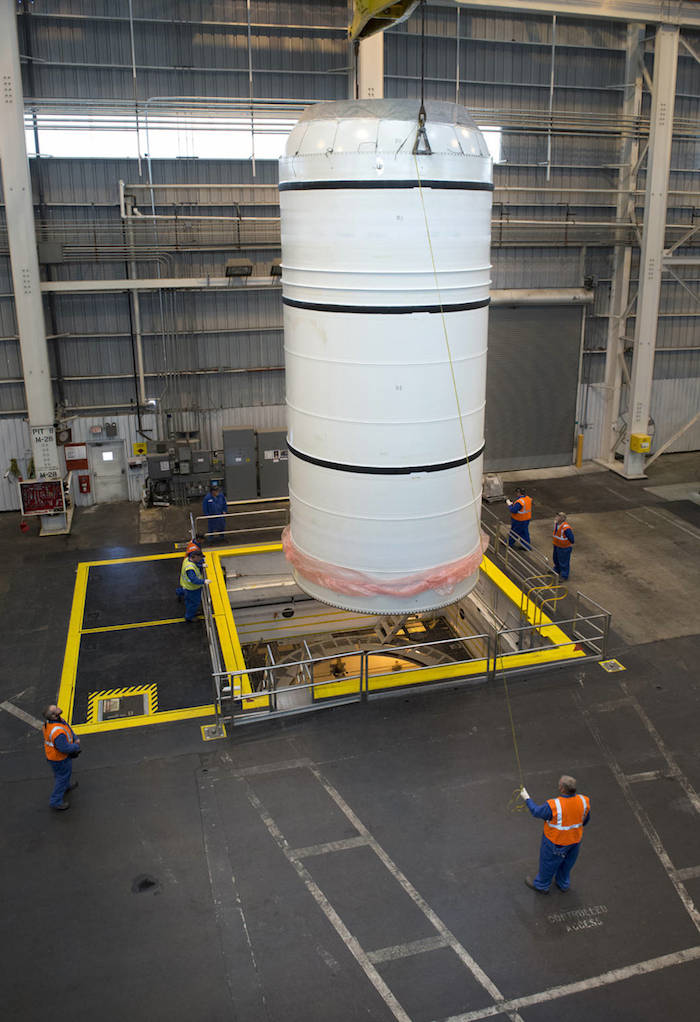
The first of 10 flight segments for the two solid-rocket boosters of NASA’s Space Launch System has been cast at Orbital ATK’s facility in Promontory, Utah. Casting involves filling the insulated metal case with propellant and allowing it to solidify or “cure” for several days. The hardware, which is the aft segment, will eventually be integrated with four other segments to make up one of the two, five-segment solid rocket boosters for the first flight of SLS in 2018. During this flight, called Exploration Mission-1, SLS will carry an unmanned Orion spacecraft to travel thousands of miles beyond the moon over the course of about a three-week mission and help NASA prepare for missions to deep space, including Mars. Orbital ATK is the prime contractor for the boosters.
Quelle: NASA
-
Update: 28.04.2016
.
Orion Crew Module for Exploration Mission-1 Lifted to Test Stand

The Orion spacecraft crew module for Exploration Mission-1 (EM-1) is lifted into a test stand for pressure testing in the Neil Armstrong Operations & Checkout Building at NASA’s Kennedy Space Center in Florida. A team from NASA and Lockheed Martin is getting ready for Orion’s proof pressure testing, an evaluation that will help verify the structural integrity of Orion’s underlying structure known as the pressure vessel.
The work is an important milestone on Orion’s journey toward EM-1, its mission atop the Space Launch System rocket in 2018. EM-1 will not have humans aboard, but it will pave the way for future missions with astronauts and for missions to Mars. During this flight, Orion will travel thousands of miles beyond the moon over the course of about three weeks.
Assembling and testing Orion for the EM-1 mission is taking place at locations across the United States and abroad. At NASA Glenn’s Plum Brook Station in Ohio, engineers are testing a structural representation of the service module with sound pressure and vibration. Meanwhile, at Langley Research Center in Hampton, Virginia, engineers are in the thick of a series of tests, dropping a representative Orion crew capsule in Langley’s Hydro Impact Basin to understand what the spacecraft and astronauts may experience when landing in the Pacific Ocean after deep-space missions. Finally, the first flight module of the Orion service module, provided by ESA (European Space Agency), was delivered this week by Thales Alenia Space to the Airbus Defence and Space, which is building it, to its location in Bremen, Germany.
Quelle: NASA
.
Update: 5.05.2016
.
Second SLS Qualification Booster Test Fire Scheduled for June 28
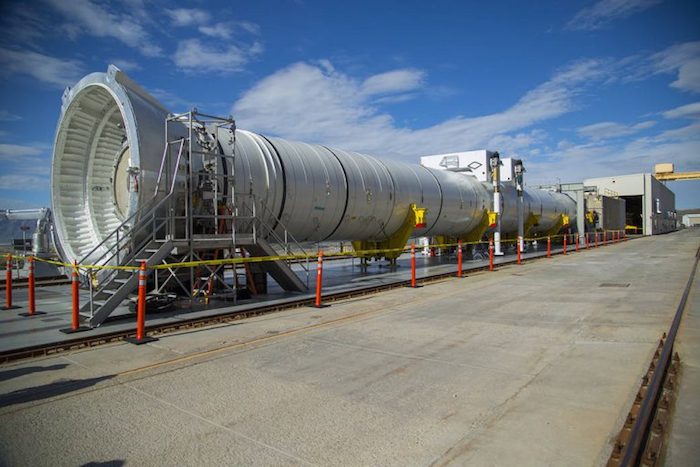
A full-scale, test version of the booster for NASA’s new rocket, the Space Launch System, will fire up for the second of two qualification ground tests June 28 at prime contractor Orbital ATK’s test facility in Promontory, Utah. Photo Credit: Orbital ATK
-
The solid rocket booster that will propel NASA’s skyscraper-size, 300-plus-foot-tall Space Launch System (SLS) rocket and its Orion spacecraft in the coming years marked off a significant development milestone in March 2015, unleashing its fury on a barren mountainside at Orbital ATK’s test stand in Promontory, Utah, for the Qualification Motor-1 test fire (QM-1). The 154-foot-long booster, the largest of its kind in the world, ignited to verify its performance at 90 degrees, the highest end of the booster’s accepted propellant temperature range and the temperature the SLS can expect to encounter at its Florida launch site on Kennedy Space Center (KSC) Launch Complex 39B.
Detailed inspections of the now disassembled booster took place over the course of 2015, with all the data collected confirming the QM-1 test as a resounding success. More than 500 instrumentation channels were used to help evaluate over 100 defined test objectives, and now work is underway at the test stand preparing the second booster for another test fire, Qualification Motor-2 (QM-2), which is scheduled to take place June 28, 2016.
Quelle: AS
.
Update: 10.05.2016
.
Thornton Leads Upgrade of Ground Special Power for Orion
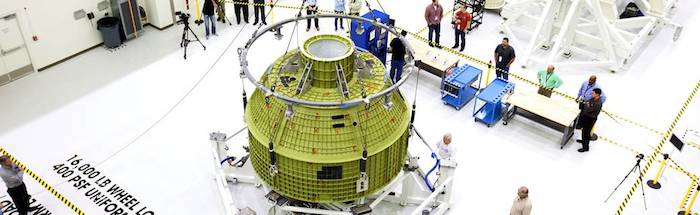
When Michael Thornton was growing up in the small south Florida city of Clewiston, he never dreamed of working in America's space program. Today, he not only is helping NASA prepare for the Journey to Mars, he recently was selected as the agency's Kennedy Space Center Employee of the Year.
As software lead for the Ground Special Power Branch of NASA Engineering, Thornton traveled to Denver in 2015 for a meeting between officials with NASA and Lockheed Martin, prime contractor for the Orion spacecraft. Following the review, he realized there was a need to upgrade ground power systems to adequately support the new vehicle.
According to Ralonda Farrant, a management and program analyst in the Avionics Division of NASA Engineering, Thornton found that some of Kennedy's ground power interfaces were lacking the ability to take full advantage of several features included in Lockheed Martin's plans for Orion to receive electrical power during ground processing.
"He brought those issues to the attention of the Engineering Directorate's lead design engineer and management team," she said in nominating Thornton for special recognition. "Michael has also identified and presented solutions to the design team which were approved for correction and implementation."
For this achievement, Thornton was selected as NASA's Employee of the Month for September 2015. From among last year's Employees of the Month, he was recently honored further as the spaceport's 2015 Employee of the Year
Thornton prefers to give credit to those he works with on a daily basis.
"I don't think I would be here without my team," he said. "They definitely work hard and we work together as one. We all listen and understand each other. That's what makes us jell as a team."
Having been raised in Clewiston, a city of just over 7,000 citizens, the Florida spaceport seemed to be far away. Thornton thought he had "no chance" of ever working in the Space Shuttle Program he heard and read about.
But in 1999 Thornton graduated from the University of Central Florida with a bachelor's degree in electrical engineering. A few months later, he had an opportunity to interview with and go to work for United Space Alliance, or USA, NASA's Space Program Operations Contractor at Kennedy.
"It was very exciting to actually get to work in the Shuttle Program," he said.
USA was formed as a limited liability company between Lockheed Martin and Boeing to operate the Shuttle Program at Kennedy, the Johnson Space Center in Houston and Marshall Space Flight Center in Huntsville, Alabama.
In 2005, Thornton was offered a new opportunity to go to work in NASA's Engineering Directorate. Today, he is leading a team that is preparing Ground Special Power, or GSP, to support the agency's Orion spacecraft.
Built to take humans farther than they have ever gone before, Orion will be the exploration vehicle that will carry crews to space launched atop NASA’s new Space Launch System rocket, the largest and most powerful ever flown. The SLS rocket will be capable of sending humans aboard Orion to deep-space destinations such as an asteroid and Mars.
During the times Orion spacecraft are assembled and processed at Kennedy, Thornton's group acts as the "power company."
"Anytime Orion needs electricity, we make sure the spacecraft gets what it needs," he said. "We convert AC power to DC through the ground power unit."
AC, or alternating current, is an electric stream in which the flow of electric charge periodically reverses direction, whereas in DC, direct current, the flow of electric charge is only in one direction.
Thornton noted that electrical support would be needed anyplace the vehicle needs power, including the Neil Armstrong Operations and Checkout Building where Orion will undergo assembly and testing. As processing moves along, other key locations will include the Vehicle Assembly Building where it will be stacked atop the SLS rocket, and Launch Pad 39B right up until the final moments before liftoff.
Recently, Thornton and his team have been designing and developing the integrated launch operations applications software for the electrical power distribution and control, or EPD&C, systems. This effort has included the fabrication, installation and verification of GSP hardware racks, which include power supply, backup battery modules and interface control displays.
"Michael has provided invaluable leadership during the development of the software requirements documents, programmable logic controller code, displays and models," Farrant said. "His knowledge of the EPD&C and GSP systems continues to be a driving force to the team."
During his recent visit to Lockheed Martin in Denver, Thornton learned about many of the Orion capabilities that will require GPU support.
"I realized that we'd need to modify the center's GPU systems to take full advantage of Orion's capabilities from voltage monitors to the spacecraft's avionics," he said.
Looking ahead, Thornton and his team already are planning for Exploration Mission 1, or EM-1, the first Orion launch atop an SLS rocket slated for late 2018.
EM-1 will be the first mission in which the Orion spacecraft will be integrated with the large SLS booster. The multi-week mission will send the spacecraft farther into space than any human-capable spacecraft has gone before. Flying nearly 40,000 miles beyond the orbit of the moon, the mission is designed to test the vehicle, making sure it's safe to put humans aboard the next launch of an SLS.
Thornton says that he is looking forward to that first SLS liftoff and hopes to be in the Launch Control Center Firing Room.
"Down the road, I definitely would like to be in the Firing Room with my headset on," he said. "As the NASA test director is polling his people on that first EM-1 mission – a big step on our way to Mars -- I want to be the person to say, 'yes, we are go.' "
EDITOR'S NOTE: In response to an employee suggestion, individuals honored in the future as NASA's Kennedy Space Center Employee of the Year will be featured in upcoming articles.
.
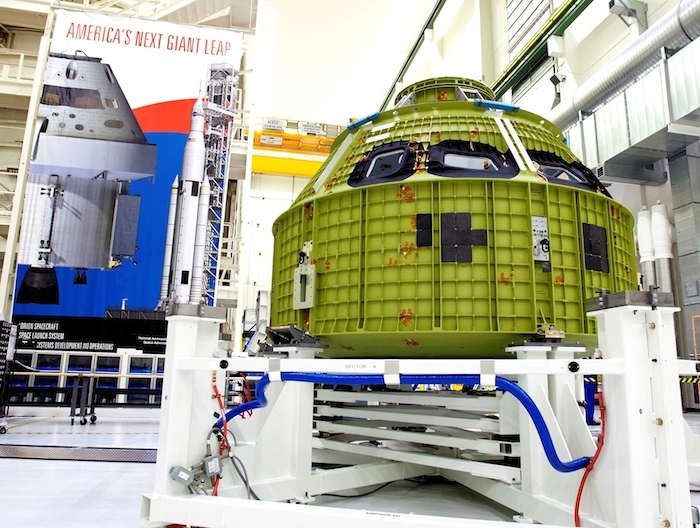
Inside the Neil Armstrong Operations and Checkout Building high bay at NASA's Kennedy Space Center, the Orion crew module pressure vessel is undergoing testing and assembly leading to Exploration Mission-1 in 2018. EM-1 will be an unpiloted flight test in which the spacecraft will launch atop NASA’s Space Launch System rocket.
Quelle: NASA
-
Update: 11.05.2016
-
Orion Passes the Pressure Test
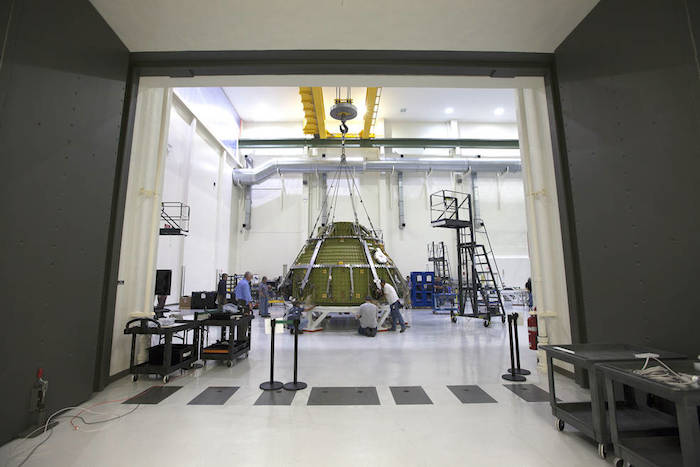
Lockheed Martin engineers and technicians prepare the Orion pressure vessel for a series of tests inside the proof pressure cell in the Neil Armstrong Operations and Checkout Building at NASA's Kennedy Space Center in Florida. Photo credit: NASA/Kim Shiflett
-
Engineers at Kennedy Space Center in Florida recently conducted a series of pressure tests of the Orion pressure vessel. Orion is the NASA spacecraft that will send astronauts to deep space destinations, including on the journey to Mars. The tests confirmed that the weld points of the underlying structure will contain and protect astronauts during the launch, in-space, re-entry and landing phases on the Exploration Mission 1 (EM-1), when the spacecraft performs its first uncrewed test flight atop the Space Launch System rocket.
The Orion pressure vessel contains the atmosphere that a crew would breathe during a mission. It also will provide living and working space for the crew, and withstand the loads and forces experienced during launch and landing.
In late April, Orion was lifted by crane from its assembly and tooling stand and moved to a test stand inside the proof pressure cell. The assembly and tooling stand is called the birdcage because it closely resembles a birdcage, but on a much larger scale.
To prepare for the test, technicians attached hundreds of strain gauges to the interior and exterior surfaces of the vehicle. The strain gauges were attached to provide real time data to the analysts monitoring the changes during the pressurization. The analysts were located in the control room next to the pressure cell. The large doors were closed and sealed and Orion was pressurized to over the maximum pressure it is expected to encounter on orbit.
Lockheed Martin, the manufacturer of the Orion crew module, ran the test at incremental steps over two days to reach the maximum pressure. During each step, the team pressurized the chamber and then evaluated the data to identify changes for the next test parameter. The results revealed the workmanship of the crew module pressure vessel welds and how the welds reacted to the stresses from the pressurization.
“We are very pleased with the performance of the spacecraft during proof pressure testing,” said Scott Wilson, NASA manager of production operations for the Orion Program. “The successful completion of this test represents another major step forward in our march toward completing the EM-1 spacecraft, and ultimately, our crewed missions to deep space.”
“It gives the team a lot of pride to see Orion coming together for EM-1,” said Ed Stanton, a systems engineer for Orion Production Operations in the Ground Systems Development and Operations Program.
Orion was tested inside the proof pressure cell in the high bay of the Neil Armstrong Operations and Checkout Building. After being moved back to the birdcage assembly stand, technicians will begin the intricate work of attaching hundreds of brackets to the vessel’s exterior to hold the tubing for the vehicle’s hydraulics and other systems.
Future tests include a launch simulation and power on. Orion also will be sent to NASA Glenn Research Center’s Plum Brook Station facility in Sandusky, Ohio, for acoustics and vibration tests. The uncrewed Orion will be outfitted with most of the systems needed for a crewed mission.
NASA’s Space Launch System rocket with the Orion spacecraft atop will roar into space from Kennedy’s Launch Pad 39B. EM-1 will send Orion on a path thousands of miles beyond the moon over a course of three weeks, farther into space than human spaceflight has ever travelled before. The spacecraft will return to Earth and safely splash down in the Pacific Ocean off the coast of California. This mission will advance and validate capabilities required for human exploration of Mars.
5261 Views