.
31.07.2015
Lockheed Martin Successfully Tests Design Changes for Orion Spacecraft’s Fairing Separation System
Data from First Test Flight Makes Technology Safer, Lighter and More Reliable
Sunnyvale, Calif., July 30, 2015 – Lockheed Martin (NYSE:LMT) engineers have successfully completed testing of design changes made to the NASA Orion spacecraft’s fairing separation system. These changes resulted from data collected during Orion’s first test flight on Dec. 5, 2014.
.
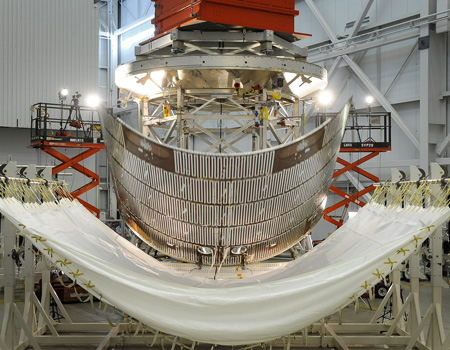
A protective panel for Orion’s service module is jettisoned during testing at Lockheed Martin’s Sunnyvale, California facility. This test series evaluated design changes to the spacecraft’s fairing separation system.
A finished Orion spacecraft has three fairings, or panels, that protect the service module radiators and solar arrays from heat, wind and acoustics during ascent into space. For the purposes of collecting data during these tests, only one fairing was separated.
The separation took about three seconds and the design changes tested were:
New push-off springs that push on the fairing for a longer period of time to provide increased safety and reliability.
As part of an ongoing mass reduction effort, the team used four crew module structural attachments instead of six.
Star trackers, or cameras that provide positioning from the stars, are used for navigation on the spacecraft. The fairing separation system pulls off the star tracker covers which prevent contamination before launch, and this process was tested for the first time.
In addition, these tests evaluated different pyrotechnic variances and higher load cases in order to prepare for Exploration Mission-1, when Orion is launched on NASA’s new Space Launch System rocket. The team was also able to collect shock data, which will be provided to the European Space Agency (ESA) to support their work designing, building and testing the service module. In fact, these same fairings will be used for service module acoustics and vibe testing taking place at NASA’s Plum Brook facility in Ohio later this year.
“The fairing separation is one of our very first critical events,” said Mike Hawes, Lockheed Martin Orion vice president and program manager. “If it doesn’t work as planned, it’s probable the mission cannot continue, and tests like this help ensure it will work right the first time and every time.”
.
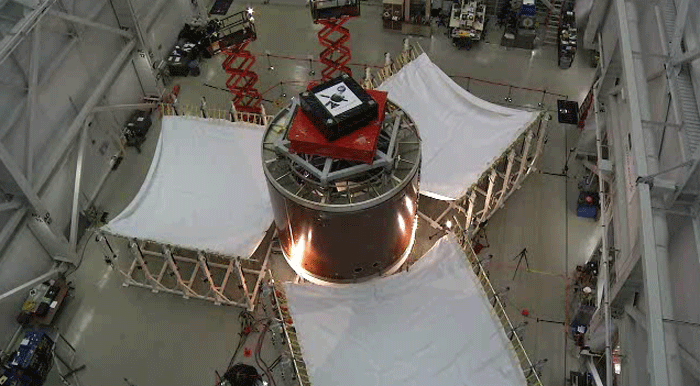
Quelle: Lockheed Martin
.
Update: 4.08.2015
.
Der erste Flug des NASA SLS Orion service module ist derzeit zwischen Juli und September 2018 geplant
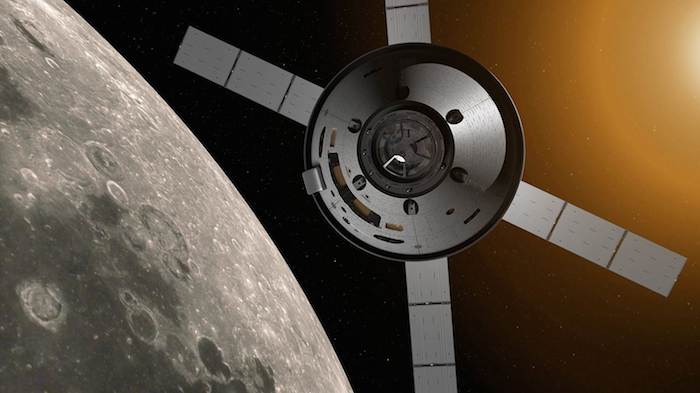
Artist’s concept of the Orion spacecraft with the European service module’s distinctive X-wing solar panels. Credit: NASA
-
The pace of the European Space Agency’s development of a power and propulsion module for NASA’s Orion crew capsule will likely determine when an unpiloted test flight of the spaceship and its heavy-lift rocket will take off, NASA officials said last week.
The first flight of NASA’s Space Launch System is currently penciled in some time between July and September 2018, according to Bill Hill, NASA’s deputy associate administrator for exploration systems development.
“We’re a little more than three years away,” Hill told members of the NASA Advisory Council’s human exploration subcommittee July 28.
The mission will send an uncrewed Orion spacecraft into lunar orbit for a mission lasting more than 20 days. The capsule will return to Earth for a parachute-assisted ocean splashdown in a final shakedown before NASA adds final life support systems and crew accommodations for a manned flight around 2021.
NASA working on the deep space exploration rocket and capsule programs under a budget projected at approximately $3 billion per year.
Bill Gerstenmaier, head of NASA’s human spaceflight directorate, told members of the subcommittee the Orion capsule’s European-made service module, which is being developed by Airbus Defense and Space, will probably be the last piece of the critical test flight to be ready for launch.
NASA and ESA officials, together with contractors from Orion-builder Lockheed Martin and Airbus, have discussed shipping the Orion service module from Europe to NASA’s Kennedy Space Center in Florida before it is finished. European engineers could travel to the Florida spaceport to complete construction of the service module before its integration with the Orion crew capsule, which is to be assembled by Lockheed Martin at KSC’s Armstrong Operations and Checkout Building.
Engineers plan to introduce changes to the Orion crew module after a successful orbital test flight in December 2014. The upgrades include a switch from a monolithic heat shield made of ablative Avcoat material to blocks of Avcoat, a change intended to improve the manufacturability of the thermal protection system.
.
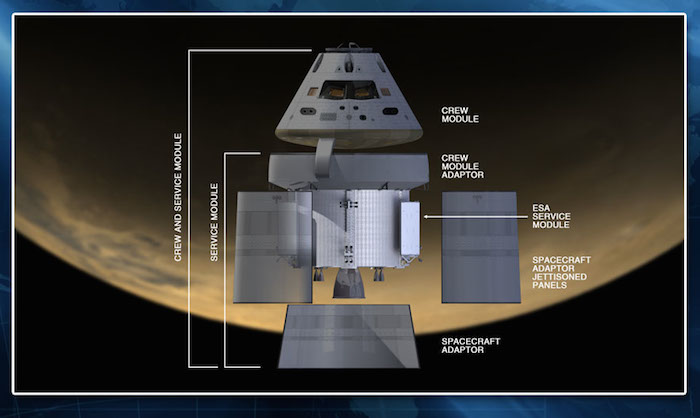
A diagram of the Orion crew capsule. Credit: NASA
-
Last year’s Orion demonstration, called Exploration Flight Test-1, launched on top of a United Launch Alliance Delta 4-Heavy booster, which sent the capsule to an altitude of approximately 3,600 miles on a four-and-a-half hour mission.
The Orion service module, which did not fly on EFT-1, will include propellant tanks, batteries, pressure vessels, four solar array wings and a hypergolic engine for major burns during the mission. NASA is supplying ESA with a space shuttle Orbital Maneuvering System engine to power the Orion spacecraft, with delivery of the engine to Europe expected in early 2016, according to a schedule chart presented by Hill.
ESA is in charge of the service module’s structure, electrical system and fuel tanks. It is the first time NASA has entrusted an international partner with a major component in the critical path of a human spaceflight program.
Without ESA’s part, NASA officials said the first SLS/Orion flight — known as Exploration Mission-1 — could be delayed even further due to U.S. budget constraints. Before partnering with ESA, NASA did not have funding to complete development of the service module in time for a flight in 2017, the original target launch date for EM-1.
The ESA-funded development of the Orion service module counts as Europe’s contribution to the International Space Station’s annual operating costs from 2017 through 2020. ESA discontinued flights of its cargo delivery craft, the Automated Transfer Vehicle, in 2014.
The Orion service module builds on technologies flown on the ATV’s space station resupply missions.
ESA is responsible for paying NASA for 8.3 percent of the space station’s operating budget each year, but the agencies prefer to process the payment through a barter agreement instead of cash. For the years 2017 through 2020, ESA says the service module agreement represents a payment to NASA of 450 million euros, or about $500 million.
Gerstenmaier said the schedule for the Orion service module was always cramped. NASA did not cinch the agreement with ESA to produce the power and propulsion element until early 2013, after European member states formally agreed to the program.
.
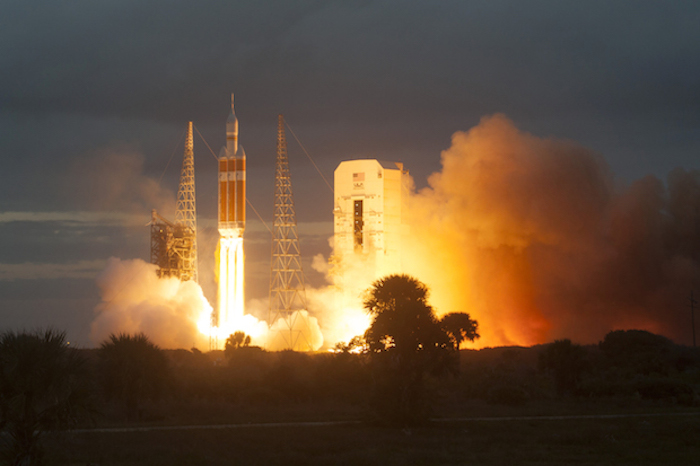
The first Orion test flight launched Dec. 5, 2014, on a United Launch Alliance Delta 4-Heavy rocket. It flew without a functioning service module. Credit: ULA
-
Other components for the EM-1 test flight have been in design for years longer. In the case of the Orion crew module, where astronauts will live on manned missions set to begin in 2021, development kicked off with NASA’s signing of a contract with Lockheed Martin in 2006 for the agency’s now-canceled Constellation moon program.
Construction of the Space Launch System’s core stage, a huge reservoir of liquid hydrogen and liquid oxygen for the rocket’s four RS-25 main engines, is also a schedule driver for the 2018 test flight.
The Boeing-built core stage is 27.5 feet in diameter and stands more than 200 feet tall. Special tools were installed at NASA’s Michoud Assembly Facility in New Orleans to assemble the rocket’s tanks and cylindrical primary structure.
The schedule is too tight to build a full-up test article, so the core stage intended to fly on EM-1 will be shipped to nearby Stennis Space Center in Mississippi in mid-2017 for an all-up test firing with its four RS-25 engines. If the ground verification goes well, the rocket will head to the launch base at the Kennedy Space Center in early 2018.
“I think getting the core stage integrated and tested at Stennis is one of the primary challenges,” Hill told the NASA advisory subcommittee. “I think the Orion (crew module) will make it, only because we’ve been through EFT-1. The European service module will probably be the pacing item to get through launch.”
The Orion program’s confirmation review, a key milestone in any NASA project, is nearing completion, according to Greg Williams, a deputy associate administrator for policy and plans.
The outcome of the confirmation review will bring clarity to the Orion program’s total cost and schedule.
Williams told the NASA Advisory Council that the agency’s leadership has declared the Orion program technically ready to continue into the next phase of development. Formal schedule and cost commitments are still being worked out.
Technicians at Michoud plan to begin welding pieces of the pressure shell for the next Orion crew module in September, according to Hill. The final welds should be complete by December, and Lockheed Martin will transport the craft to KSC in January for pressure testing and outfitting with computers, fuel tanks, thrusters, a heat shield and other systems.
Thales Alenia Space, a subcontractor to Airbus on the Orion service module, is testing a structural pathfinder of the element in Italy. The test article will go to NASA’s Plum Brook Station in Ohio for shake tests in October, Hill said.
.
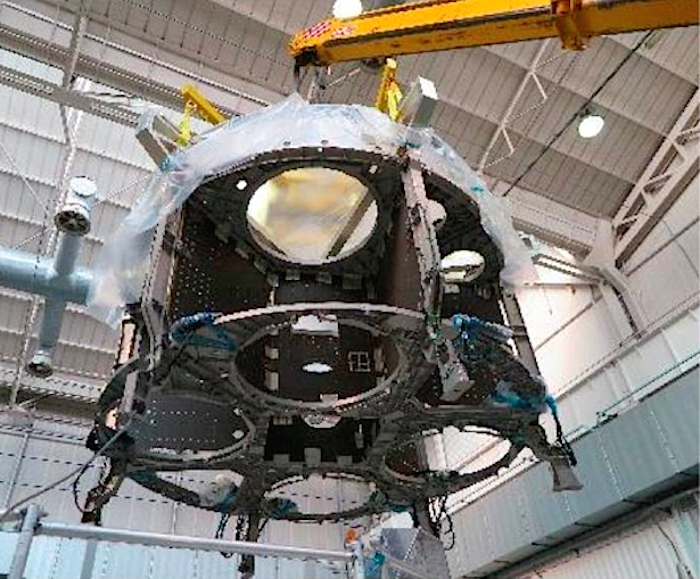
A structural test article of the Orion spacecraft’s service module is undergoing testing at Thales Alenia Space in Italy. It will be shipped to NASA’s Plum Brook Station in Ohio in October for further tests. Credit: NASA/ESA
-
Once the Orion crew and service modules are finished, NASA will send the units to Plum Brook in 2017 for combined testing in a huge thermal vacuum chamber to mimic the conditions of space. They will return to KSC for final flight preps.
ULA is kicking off production of the SLS upper stage’s first flight unit, which is propelled by an Aerojet Rocketdyne RL10 engine. The rocket is an interim upper stage for the heavy-lift launcher, and it is based on the Delta 4 booster’s five-meter (16.4-foot) second stage.
Preparations on the Space Launch System’s twin solid rocket boosters is also due to start soon at Orbital ATK’s facilities in Utah. A final qualification firing of a stationary booster is scheduled for April 2016.
Work on SLS ground systems at KSC is also proceeding, Hill said.
Structural modifications to the SLS mobile launch platform, originally built for the ill-fated Ares 1 rocket, were finished in July under a $20 million contract with a local Florida construction firm, Hill said.
A new contract should be signed within weeks to add cladding and support arms to the mobile launch tower, which is sitting outside the Vehicle Assembly Building at KSC. The addition of new work platforms inside the cavernous VAB’s High Bay 3 is about 30 percent complete, according to Hill.
Eleven construction projects are underway at launch pad 39B, where SLS missions will take off. The work includes refurbishment of the flame trench and sound suppression water system.
Ground systems at KSC should be ready around the end of 2017, officials said.
Quelle: SN
-
Update: 13.08.2015
.
Orion Begins Critical Design Review Milestone
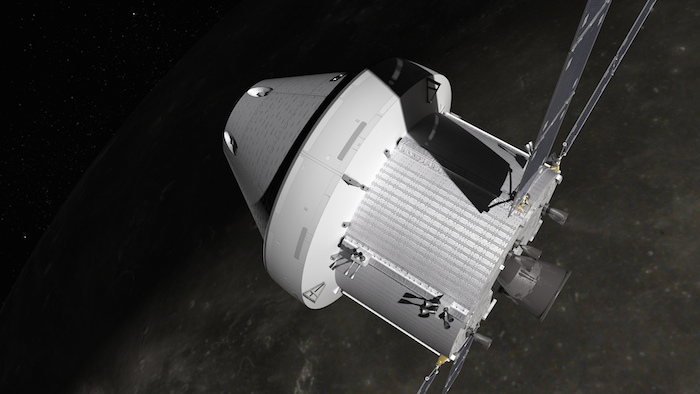
NASA’s Orion Program kicked off its critical design review at the agency’s Johnson Space Center in Houston the week of Aug. 3, a major program milestone that will ensure the spacecraft’s design is ready for its deep space missions atop NASA’s Space Launch System (SLS) rocket.
Orion, which successfully flew about 3,600 miles into space last year during an uncrewed flight test, is being developed to send astronauts to new destinations in the solar system, including an asteroid and on toward Mars. During its next mission, Orion will venture to a distant lunar orbit beyond the far side of the moon.
“Our team across the country has been working incredibly hard to develop a spacecraft capable of expanding humanity’s frontier in the solar system,” said Mark Geyer, Orion Program manager. “Since even before flying Orion in space last year, we’ve been moving at full steam toward our first flight on SLS, and this review gives us a chance to make sure all systems and their designs meet our requirements and are in sync before we continue pressing ahead.”
The review is a months-long process where engineers delve into the details of the spacecraft’s systems and subsystems to evaluate their maturity and involves thousands of documents. The milestone is a rallying point for those with technical stakes in successfully building and flying future Orion missions to ensure all elements are in sync before moving ahead with full-scale fabrication, assembly, integration and testing.
It will include an evaluation of common aspects of the spacecraft for Exploration Mission (EM)-1 and the spacecraft for EM-2, the first Orion mission with astronauts, such as the spacecraft’s structures, pyrotechnics, Launch Abort System, guidance, navigation and control and software, among many other elements. Systems unique to EM-2 will be addressed at a later critical design review for the mission in the fall of 2017.
Not only will Orion technical experts take a close look at the spacecraft, but engineers working on SLS, which recently completed its own critical design review, the ground systems needed for launch and other elements needed to execute successful missions, such as mission operations and safety and mission assurance, will be on hand during the review to provide insight.
“We’re working through our critical design review now so that we can balance evaluating individual components with the hardware manufacturing needs we have to start our assembly and integration activities,” said Geyer.
The Orion Program’s critical design review is targeted for completion in late October.
.
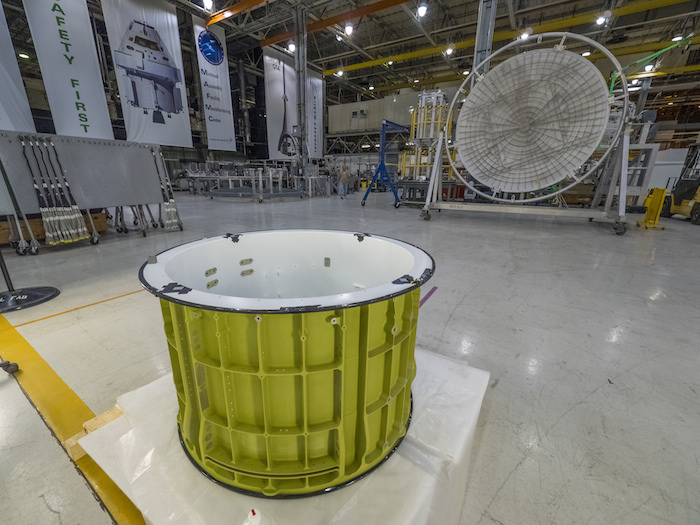
Pieces of the Orion spacecraft that will fly on Exploration Mission-1 already are being prepared for welding at NASA’s Michoud Assembly Facility in New Orleans.
Quelle: NASA
-
Update: 26.08.2015
.
Orion-Kapsel-Tests
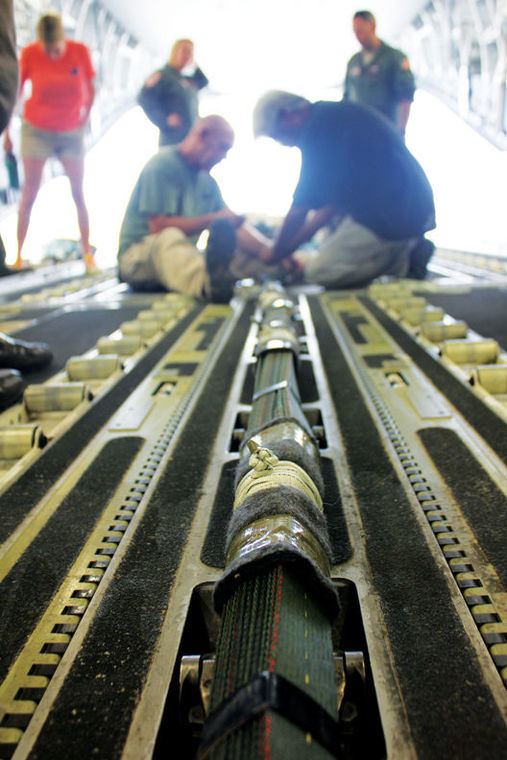
Deployment system work
Workers prepare the deployment system in the cargo bay of a C-17 that will drop the test vehicle from 35,000 feet in the air. This round of testing is looking at the Capsule Parachute Assembly System to ensure that it will work up to standards during an actual mission.
.
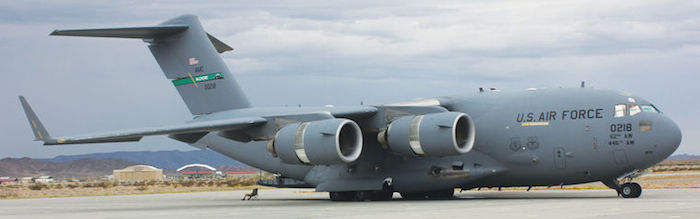
C-17
The C-17 that will take the the test vehicle 35,000 feet in the air in order to conduct a test on the Orion Multi-Purpose Crew Vehicle's parachutes.
.
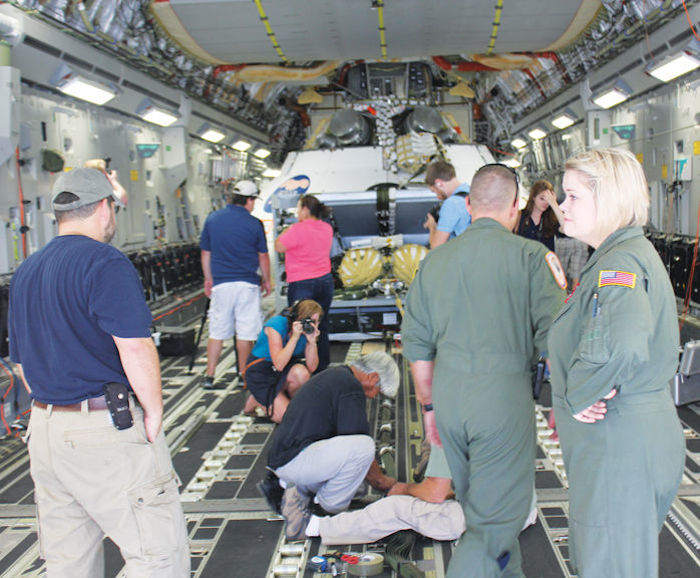
Getting ready
Crew works on preparing the test module, in the background, with media present. There will be approximately 8 parachutes involved in Wednesday's test, although only the drogues and main system would accompany Orion on an actual mission.
.
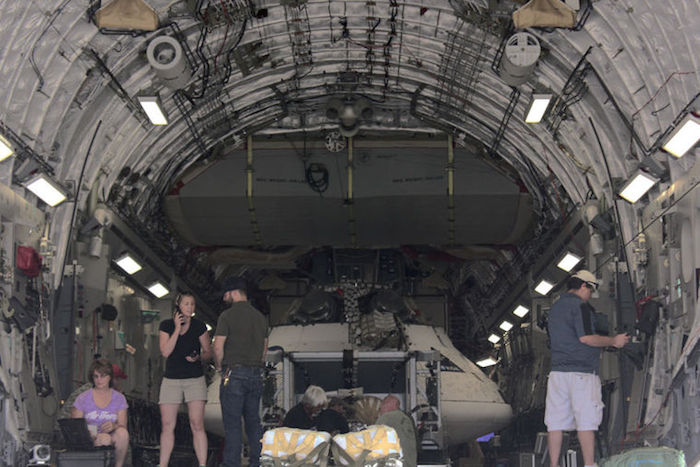
Double checking
The test module for the Orion capsule sits in the back of the C-17 that will be bringing the craft up to an altitutde of 35,000 feet to test the capsule's parachute system.
.
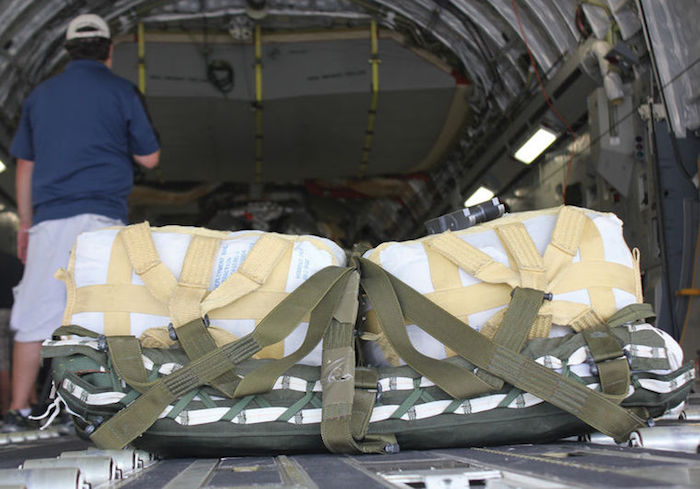
All packed up
One of the parachute systems, in its packed form, ready to go for testing.
.
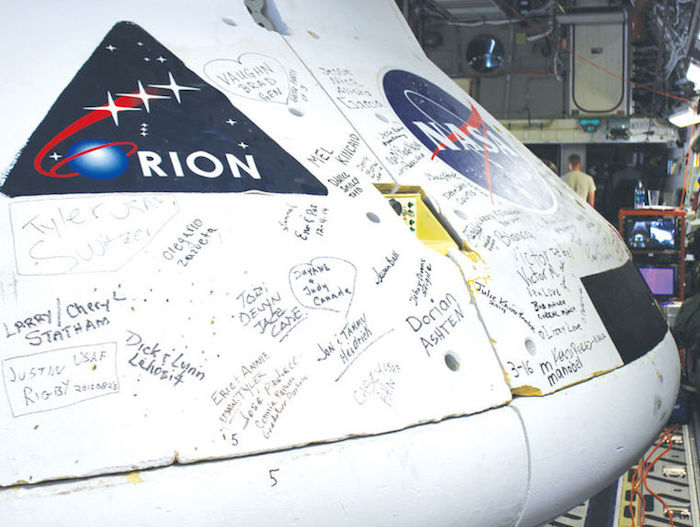
Signing off
The testing module signed by those who have worked on the mission.
Quelle: Yuma Sun
-
Update: 27.08.2015
.
Orion Parachute System Withstands Failure Test
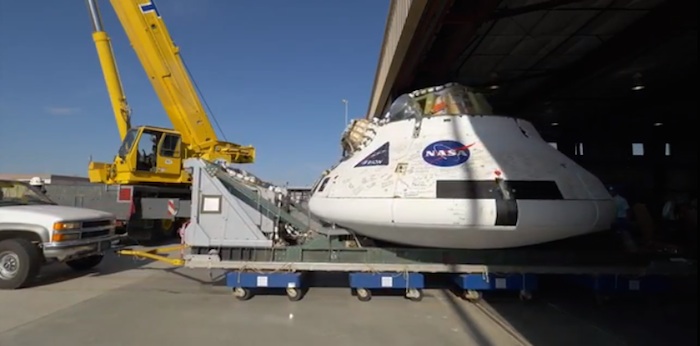
NASA successfully completed a dramatic test of the Orion spacecraft’s parachute system and its ability to perform in the event of a partial deployment on re-entry. On Wednesday, Aug. 26, a test version of Orion touched down in the Arizona desert after engineers intentionally failed two different parachutes used in the sequence that stabilizes and slows the spacecraft for landing.
During the test, a C-17 aircraft dropped a representative Orion capsule from its cargo bay at an altitude of 35,000 feet, or more than 6.5 miles, in the skies above the U.S. Army Yuma Proving Ground in Yuma, Arizona. The engineering model capsule then began its parachute deployment sequence. The model has a mass similar to that of the Orion capsule being developed for deep space missions, and similar interfaces with its parachute system. Engineers purposefully simulated a failure scenario in which one of the two drogue parachutes, used to slow and stabilize Orion at high altitude, and one of its three main parachutes, used to slow the crew module to landing speed, did not deploy.
“We test Orion’s parachutes to the extremes to ensure we have a safe system for bringing crews back to Earth on future flights, even if something goes wrong,” says CJ Johnson, project manager for Orion’s parachute system. “Orion’s parachute performance is difficult to model with computers, so putting them to the test in the air helps us better evaluate and predict how the system works.”
As part of the test, engineers also evaluated a change to the risers, which connect the parachutes to the vehicle from steel to a textile material as well as the use of lighter weight suspension lines for several of the parachutes. Both changes reduce overall mass and volume of the system.
Orion’s parachute system is a critical part of returning future crews who will travel to an asteroid, on toward Mars and return to Earth in the spacecraft. The first parachutes deploy when the crew module is traveling more than 300 mph, and in a matter of minutes, the entire parachute system enables it to touch down in the ocean at about 20 mph.
That system is composed of 11 total parachutes that deploy in a precise sequence. Three parachutes pull off Orion’s forward bay cover, which protects the top of the crew module -- where the packed parachutes reside -- from the heat of reentry through Earth’s atmosphere. Two drogues then deploy to slow the capsule and steady it. Three pilot parachutes then pull out the three orange and white mains, on which Orion rides for the final approximately 8,000 feet of its descent. Orion’s main parachutes are densely packed and sit on the top part of the spacecraft. Once fully inflated, they could cover almost an entire football field.
During Orion’s flight test in space in 2014, the parachute system performed flawlessly, enabling the spacecraft to descend through the Earth’s atmosphere and splash down in the Pacific Ocean after traveling about 3,600 miles into space.
Wednesday’s airdrop test was the penultimate evaluation as part of an engineering series before tests begin next year to qualify the parachute system for crewed flights. The qualification series will include eight airdrops over a three- year period that will put the final design through extreme conditions to ensure a safe return for the astronauts.
.
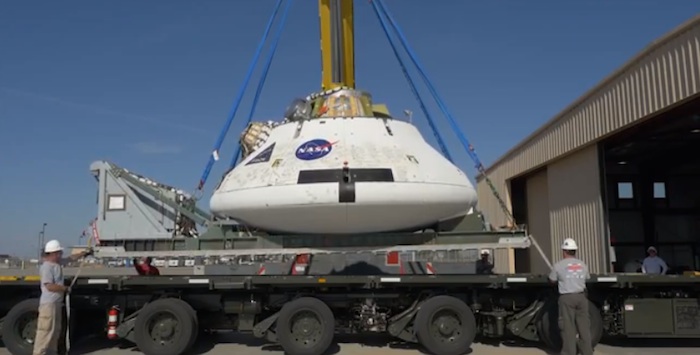
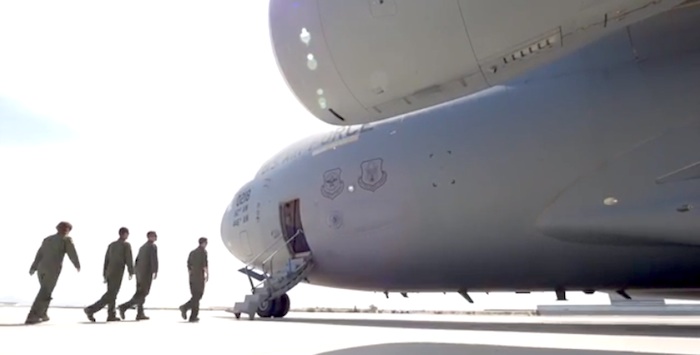
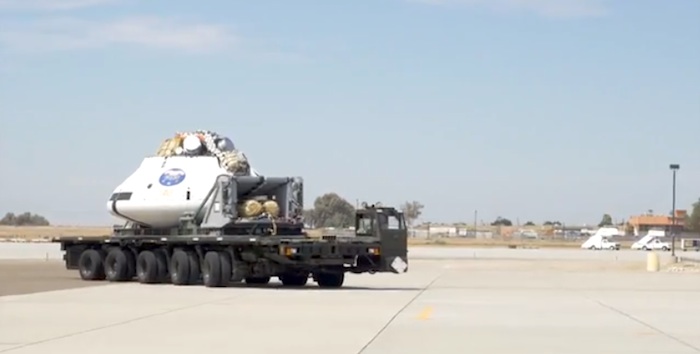
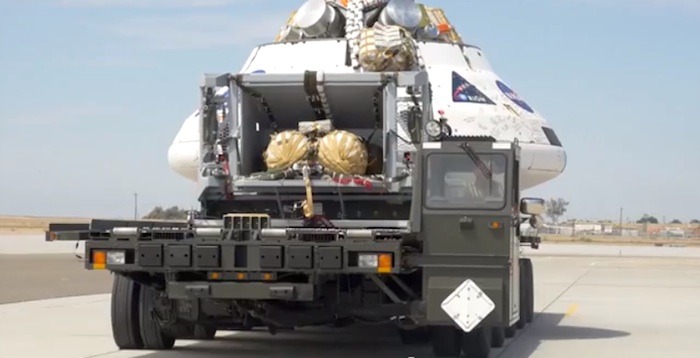
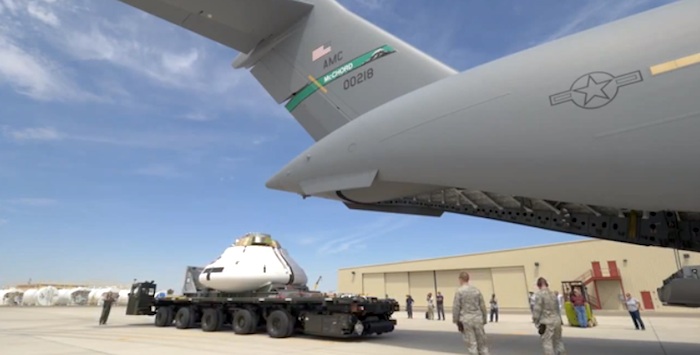
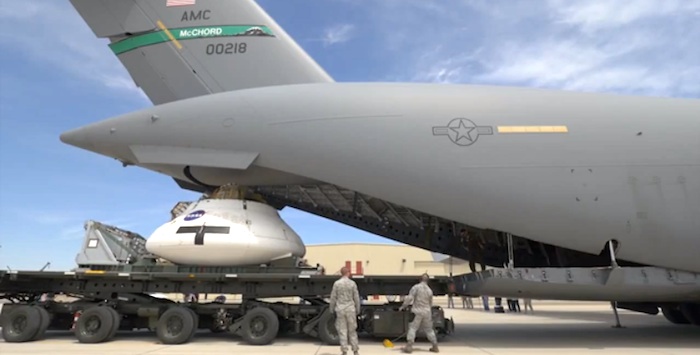
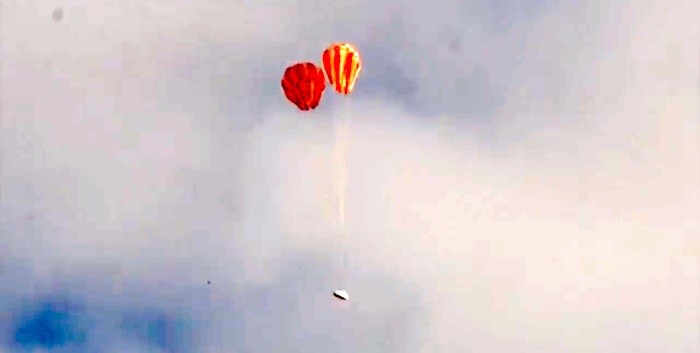
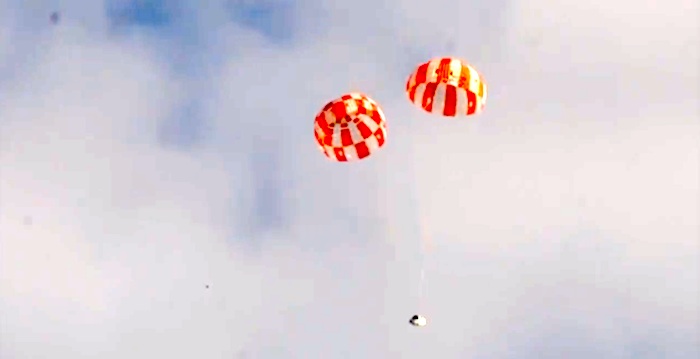
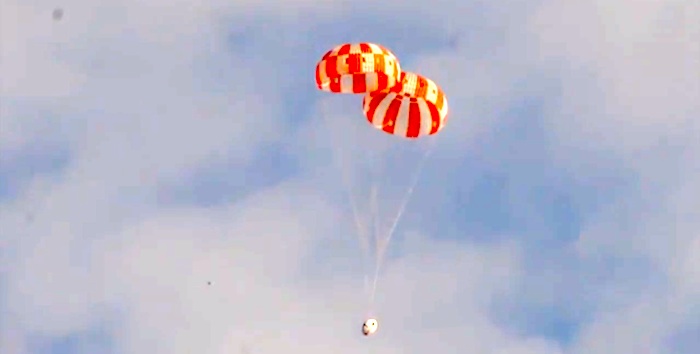
NASA’s successfully completed Aug. 26 a risky test of the Orion spacecraft’s parachute system. A test version of Orion touched down in the Arizona desert after a planned failure of two of its parachutes used to stabilize and slow the spacecraft for landing. During the test, a C-17 aircraft dropped a representative Orion capsule from its cargo bay at an altitude of 35,000 feet, or more than 6.5 miles, in the skies above the U.S. Army Yuma Proving Ground in Yuma, Arizona. The engineering model, which has a similar mass and interfaces with the parachute system as the Orion being developed for deep space missions, then began its parachute deployment sequence. Engineers purposefully simulated the failure of one of its two drogue parachutes, used to slow stabilize Orion in the air, and one of its three main parachutes, used to slow the crew module to landing speed, did not deploy. The airdrop test was the penultimate evaluation as part of an engineering series before tests begin next year to qualify the parachute system for crewed flights.
Quelle: NASA
-
Update: 9.09.2015
.
Erste Teile von NASAs Orion für die nächste Mission treffen in Michoud ein
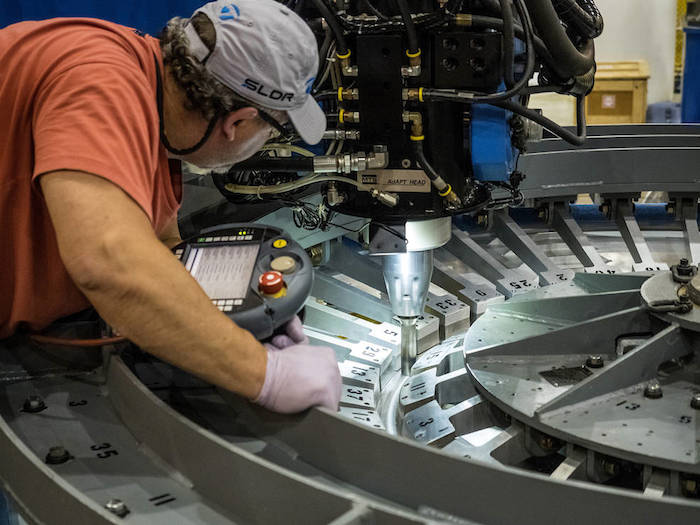
At NASA’s Michoud Assembly Facility in New Orleans, engineers welded together on Sept. 5, two sections of the Orion spacecraft’s primary structure that will fly on Exploration Mission-1, the first flight of Orion atop the agency’s Space Launch System rocket.
Credits: NASA
.
NASA is another small step closer to sending astronauts on a journey to Mars. On Saturday, engineers at the agency’s Michoud Assembly Facility in New Orleans welded together the first two segments of the Orion crew module that will fly atop NASA’s Space Launch System (SLS) rocket on a mission beyond the far side of the moon.
“Every day, teams around the country are moving at full speed to get ready for Exploration Mission-1 (EM-1), when we’ll flight test Orion and SLS together in the proving ground of space, far away from the safety of Earth,” said Bill Hill, deputy associate administrator for Exploration Systems Development at NASA Headquarters in Washington. “We’re progressing toward eventually sending astronauts deep into space.”
The primary structure of Orion’s crew module is made of seven large aluminum pieces that must be welded together in detailed fashion. The first weld connects the tunnel to the forward bulkhead, which is at the top of the spacecraft and houses many of Orion’s critical systems, such as the parachutes that deploy during reentry. Orion’s tunnel, with a docking hatch, will allow crews to move between the crew module and other spacecraft.
“Each of Orion’s systems and subsystems is assembled or integrated onto the primary structure, so starting to weld the underlying elements together is a critical first manufacturing step,” said Mark Geyer, Orion Program manager. “The team has done tremendous work to get to this point and to ensure we have a sound building block for the rest of Orion’s systems.”
Engineers have undertaken a meticulous process to prepare for welding. They have cleaned the segments, coated them with a protective chemical and primed them. They then outfitted each element with strain gauges and wiring to monitor the metal during the fabrication process. Prior to beginning work on the pieces destined for space, technicians practiced their process, refined their techniques and ensured proper tooling configurations by welding together a pathfinder, a full-scale version of the current spacecraft design.
NASA’s prime contractor for the spacecraft, Lockheed Martin, is doing the production of the crew module at Michoud.
.
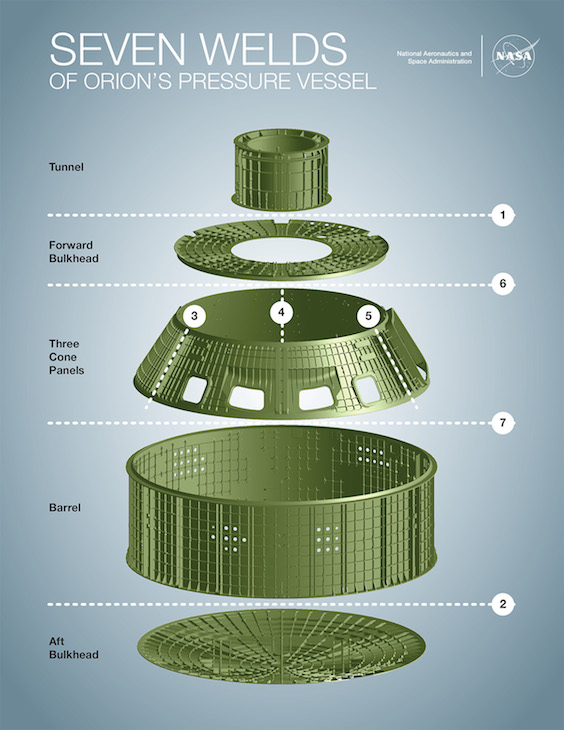
This diagram shows the seven pieces of Orion’s primary structure and the order in which they are welded together.
Credits: NASA
.
NASA’s prime contractor for the spacecraft, Lockheed Martin, is doing the production of the crew module at Michoud.
Through collaborations across design and manufacturing, teams have been able to reduce the number of welds for the crew module by more than half since the first test version of Orion’s primary structure was constructed and flown on the Exploration Flight Test-1 last December. The Exploration Mission-1 structure will include just seven main welds, plus several smaller welds for start and stop holes left by welding tools. Fewer welds will result in a lighter spacecraft.
During the coming months as other pieces of Orion’s primary structure arrive at Michoud from machine houses across the country, engineers will inspect and evaluate them to ensure they meet precise design requirements before welding. Once complete, the structure will be shipped to NASA’s Kennedy Space Center in Florida where it will be assembled with the other elements of the spacecraft, integrated with SLS and processed before launch.
Quelle: NASA
-
Update: 17.09.2015
.
Orion spacecraft may not fly with astronauts until 2023
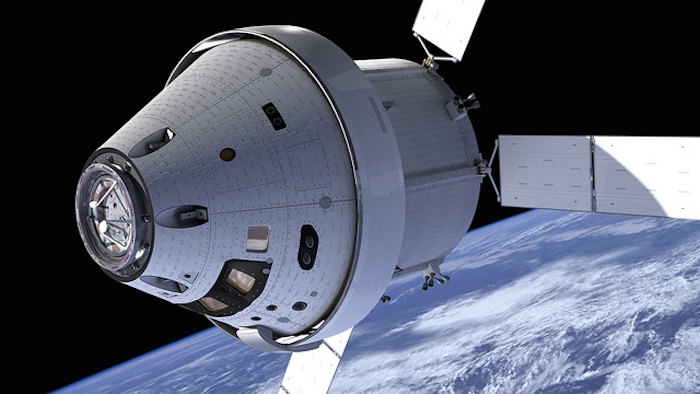
Artist’s concept of the Orion spacecraft. Credit: NASA
-
The first piloted flight of NASA’s Orion space capsule, a vehicle designed to carry astronauts away from Earth for the first time in two generations, may slip from 2021 to 2023, agency officials said Wednesday.
A thorough review of the program in recent weeks highlighted risks that threaten the crewed flight’s target launch date in August 2021, and managers concluded the mission is likely to fly some time later.
NASA officials set April 2023 as the timeframe when they expect the Orion spacecraft to be ready to host humans on a flight around the moon.
“The team is going to continue to work toward the August 2021 date, but we’re committing that we’ll be no later than April 2023,” said Robert Lightfoot, NASA’s associate administrator. “I saw no reason this early in the process to change that ‘working to’ date for the team, and neither did the standing review board.”
Lightfoot said an April 2023 launch for the first Orion mission with astronauts is achievable with 70 percent confidence, keeping with NASA’s policy.
NASA did not run models to calculate a confidence level for the flight’s target launch date in 2021, but “it’s not a very high confidence level, I’ll tell you that, just because of the things we see historically pop up,” Lightfoot said.
The Orion spacecraft, designed to host four astronauts for up to 21 days in deep space, will blast off on top of NASA’s Space Launch System, a huge rocket in development borrowing propulsion and technologies from the retired space shuttle program.
A test flight of the heavy-lift launcher and the Orion capsule without a crew, called Exploration Mission-1, remains on track for late 2018, Lightfoot said, but will undergo another review later this year. The Exploration Mission-2 flight, now targeted for no later than April 2023, is the program’s first space shot with astronauts aboard.
The Orion program’s confirmation review, held at NASA Headquarters in Washington with participation from an independent board, also set a budget to take the spacecraft through its first piloted mission.
NASA says it needs another $6.77 billion to complete development of Orion through 2023, atop $10.5 billion spent on the spacecraft since the project dawned with the Constellation program, an initiative started in 2005 under the Bush administration.
That brings the program’s total projected cost to more than $17 billion through the first flight with astronauts. The Space Launch System budget is forecast to be more than $7 billion from early 2014 through the first demonstration launch in 2018.
-
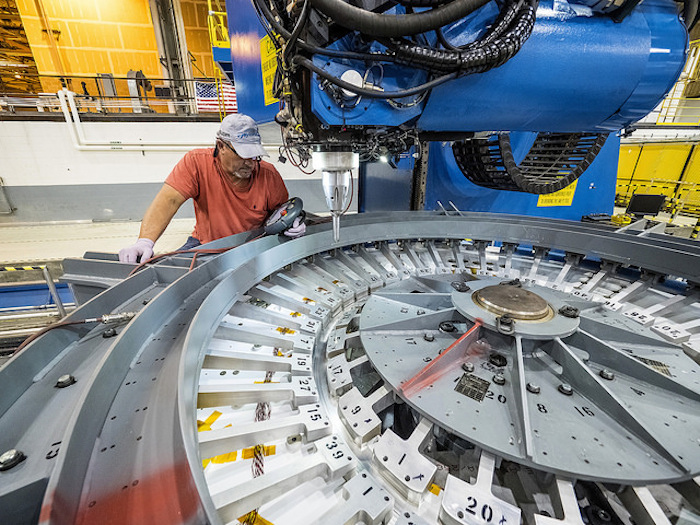
Lockheed Martin engineers perform the first weld for the Exploration Mission-1 Orion crew module at NASA’s Michoud Assembly Facility on Sept. 5. Credit: NASA/Radislav Sinyak
-
Bill Gerstenmaier, head of NASA’s directorate responsible for human exploration and operations, said the Orion project is making “solid technical progress” after a successful orbital test flight in December 2014.
Technicians at NASA’s Michoud Assembly Facility in New Orleans have started welding the pressure shell for the next Orion vehicle, which will fly in 2018 on its next uncrewed test flight. NASA will deliver the capsule’s basic structure to the Kennedy Space Center in Florida early next year for final assembly, outfitting and testing.
Reviewers charged with measuring the progress of the Orion program raised concerns about NASA’s plans to reuse hardware on multiple flights of the capsule, software development efforts, and structural testing, officials said.
NASA and Lockheed Martin, the agency’s prime contractor for Orion, plan to take key avionics boxes from the EM-1 Orion capsule and reuse them for EM-2.
“The intent right now is to refly those boxes on EM-2,” Gerstenmaier said. “The concern is if you have any kind of problem with the box on EM-1, and it’s not available for EM-2, you could run into a problem where that impacts the build of EM-2.”
Lockheed Martin is currently under contract to deliver three complete Orion crew capsules, including the vehicle flown on the EFT-1 demo flight in 2014 and spacecraft for EM-1 and EM-2.
“Right now, we’re not seeing any issues in those areas, but we have to account for those because we’ve got a lot of runway in front of us,” Lightfoot said.
“I think we’re being somewhat conservative,” Gerstenmaier said in a conference call with reporters Wednesday. “My teams will tell you that they’re trying to retire every risk out there.”
“Each times these guys hit a milestone in their testing and their predictions, we either retire risk or actually realize it,” Lightfoot told reporters.
Gerstenmaier gave high marks to engineers working on a redesign of Orion’s heat shield. Instead of installing the thermal shell on to the capsule in one monolithic piece, technicians will bolt on the Avcoat ablative heat shield in blocks for future flights.
It is a lesson learned by engineers after it took ground crews longer than planned to fabricate and install the heat shield for the EFT-1 test flight last year, in which a Delta 4-Heavy rocket lofted the capsule on a trajectory 3,600 miles above Earth in a major test of the craft’s thermal protection system and guidance, navigation and control algorithms.
“We are making a heat shield change, but the engineering test article for that heat shield is already going to be complete by the end of this month, so that’s moving at a very good pace moving forward,” Gerstenmaier said.
Another potential problem area identified by the review board involved the European-built service module for Orion. NASA cinched an agreement with the European Space Agency in early 2013 to supply the power and propulsion unit for the EM-1 robotic test flight in 2018.
ESA and its service module contractor, Airbus Defense and Space, are working on the component with technologies derived from Europe’s Automated Transfer Vehicle, which made five successful supply deliveries to the International Space Station before its retirement earlier this year.
The service module’s schedule is at the top of the list of threats that could delay the EM-1 test flight in 2018, according to Bill Hill, NASA’s deputy associate administrator for exploration systems.
But the concerns coming out of the Orion confirmation review focused on NASA’s plans for the service module for EM-2. NASA and ESA have not agreed on whether Europe will contribute a full-up service module for Orion’s first crewed mission.
“We’ve got the first (European service module) coming in for EM-1, and what we learn from EM-1 actually feeds into what happens for EM-2,” Lightfoot said.
The Exploration Mission-1 flight plan calls for the Orion module and its four-person crew to go into a distant retrograde orbit about 44,000 miles from the moon for a mission lasting up to three weeks.
“We use EM-1 to check out the service module to make sure we can do the burns in and and out of the distrant retrograde orbit around the moon,” Gerstenmaier said. “We’ll make sure the communications systems work, we’ll make sure the navigation stuff works, (and) we’ll make sure all the software works.
“Then comes EM-2, and the big thing there is the crew interfaces,” Gerstenmaier said. “How does the crew interact with the vehicle? What are the displays and controls like? What do they do during entry configuration?”
EM-2 also introduces Orion’s life support systems, such as oxygen supplies, devices to scrub carbon dioxide out of the atmosphere, plus temperature and humidity controls, according to Gerstenmaier.
It is unlikely the EM-2 crew will rendezvous with an asteroid as part of NASA’s asteroid retrieval mission, an initiative to send out a robotic space probe to tow a small rock back into lunar orbit for human visits, according to Gerstenmaier. That mission, if approved by Congress, will come later.
Gerstenmaier said NASA plans to launch an SLS/Orion mission once per year after EM-2, assuming budgets allow. Later missions in a region around the moon dubbed “cis-lunar space” may test out rendezvous techniques, spacewalks, asteroid docking, and in-space habitats to prove out technologies required for Mars missions.
“It’s important to note that we are building a big program,” Lightfoot said. “We’re building a multi-decadal human exploration program, and while the individual launches of EM-1 and EM-2 are very important, and they are great indicators of our progress and how we’re doing, we’ve got to balance those individual missions with the overall context of this exploration journey we’re on.”
Quelle: SN
-
NASA Completes Key Milestone for Orion Spacecraft in Support of Journey to Mars
Spacesuit engineers demonstrate how four crew members would be arranged for launch inside the Orion spacecraft, using a mockup of the vehicle at Johnson Space Center.
Credits: NASA/Robert Markowitz
-
NASA’s mission to send astronauts to deep space destinations where no other human has traveled has taken another important step forward with the completion of a critical milestone for the Orion spacecraft currently in production.
Agency officials have completed a rigorous technical and programmatic review, confirming continued support of the program and establishing NASA’s commitment to the program’s technical, cost, and schedule baseline. This is the first time NASA has reached this level of progress for a spacecraft designed to take humans into deep space beyond the moon, including to an asteroid placed in lunar orbit and on the journey to Mars.
“Our work to send humans out into the solar system is progressing,” said NASA Administrator Charles Bolden. “Orion is a key piece of the flexible architecture that will enable humanity to set foot on the Red Planet, and we are committed to building the spacecraft and other elements necessary to make this a reality.”
A successful test of an uncrewed Orion capsule, Exploration Flight Test-1 (EFT-1), flew in December 2014, providing important data that allowed engineers to identify risks associated with deep space flight and re-entry and use that knowledge to improve the design of Orion for its next test flights, Exploration Missions 1 and 2 (EM-1 and EM-2).
Performance data has helped to improve manufacturing processes, as well. Engineers have already incorporated many of these improvements into elements of the EM-1 design, including the crew compartment or pressure vessel, which now is in fabrication and assembly at companies across the country. The vessel is comprised of seven panels or sections, and the first two of these were welded together last week. When complete, this capsule will launch on NASA’s Space Launch System (SLS) rocket on the first fully integrated flight test, EM-1.
Astronauts will fly on Orion for the first time on EM-2. That mission will build on the results of the EM-1 flight with additional requirements that the Orion capsule includes fully integrated environmental control and life support systems; controls; and communications designed specifically for the human operation; and advanced launch and re-entry spacesuits for the crew. The recent review, culminating in what is known within NASA as Key Decision Point C (KDP-C), includes all of these technological advancements, and approval represents agency support for this work and the Orion program plan.
The decision commits NASA to a development cost baseline of $6.77 billion from October 2015 through the first crewed mission (EM-2) and a commitment to be ready for a launch with astronauts no later than April 2023. The commitment is consistent with funding levels in the president’s budget request. Conservative cost and schedule commitments outlined in the KDP-C align the Orion Program with program management best practices that account for potential technical risks and budgetary uncertainty beyond the program's control.
“As we take these steps to develop the capabilities we need to send astronauts deep into space, we’re also aligning how we manage our human exploration systems development programs to ensure we are prepared for unforeseen future hurdles,” said Robert Lightfoot, NASA associate administrator. “We’re committing to this funding and readiness level to stay on the journey we’ve outlined to get to Mars.”
Orion engineers now are executing a rigorous review of the spacecraft’s engineering design and technical progress of the vehicle systems and subsystems. This critical design review (CDR) will demonstrate Orion is ready to proceed to full-scale fabrication, assembly, integration and testing. NASA’s SLS Program recently completed this milestone, and its Ground Systems Development and Operations (GSDO) Program will begin its review this fall.
“The Orion Program has done incredible work, progressing every day and meeting milestones to prepare for our next missions,” said William Gerstenmaier, the agency’s associate administrator for Human Exploration and Operations at NASA Headquarters. “The team will keep working toward an earlier readiness date for a first crewed flight, but will be ready no later than April 2023, and we will keep the spacecraft, rocket and ground systems moving at their own best possible paces.”
In the coming months, Orion will complete its CDR; see the arrival of a test version for the European Space Agency-provided service module at NASA’s Plum Brook Station near Sandusky, Ohio; perform a series of parachute tests; and complete the welding of the crew pressure vessel. Although Orion’s readiness date for EM-1 was not formally part of the KDP-C milestone commitment, engineers continue to work toward a commitment for SLS and GSDO to be ready for the uncrewed mission in fall 2018, and NASA will set an integrated launch date after GSDO’s critical design review is completed.
Quelle: NASA
-
Update: 23.09.2015
.
Titanium Tanks for ESM
Airbus Defence and Space, prime contractor for NASA’s Orion space vehicle’s European Service Module (ESM), has completed four large titanium tanks for the module that will be delivered for initial testing.
The tanks are the first hardware to be supplied for the Orion space vehicle. Each tank is 2.67 metres high with a diameter of 1.15 metres. The tanks weight approximately 100 kilograms when empty and have a volume of 2,100 litres, giving a total payload capacity of almost nine tonnes of fuel (monomethylhydrazine (MMH) and mixed oxides of nitrogen (MON)). Most of the ESM’s total mass of just over 13 tonnes will consist of fuel.
The tanks will be first transported to Italy, where the structural test model will be assembled before being tested in the United States. The primary goal of these initial tests is to verify whether the structural components can withstand the enormous loads, especially during take-off. The next step is to build the engineering model that will be assembled and tested at Airbus Defence and Space in Bremen. This model will be used to test the inner workings of the tanks, which ensure a continuous, bubble-free flow of propellant to the motors in zero gravity. The actual flight tanks for the ESM – which will be used for the first time when the uncrewed Exploration Mission 1 launches in 2018 – will be built by Airbus Defence and Space in Bremen by mid-2016.
The ESM will provide propulsion, power and thermal control to the Orion space vehicle, and will also supply crew members with water and oxygen during missions to the Moon, asteroids and later, eventually, to Mars.
Quelle: Airbus GROUP
5420 Views