.
SpiderFab
Although SpiderFab is reminiscent of a creepy Halloween spider, this space technology could radically change the way we build and deploy spacecraft. The SpiderFab process for on-orbit construction of large, lightweight structures could dramatically reduce the launch mass and stowed volume of NASA systems for astronomy, Earth-observation, and other missions requiring large apertures or large baselines, enabling them to be deployed using much smaller, less expensive launch vehicles and thereby reducing total life cycle cost for these missions. This Phase II NASA Innovative Advanced Concepts (NIAC)-funded research is developing and demonstrating methods to address the key risk of fabrication in the thermal and vacuum environment of space.
.
SpiderFab: Architecture for On-Orbit Construction of Kilometer-Scale Apertures
.
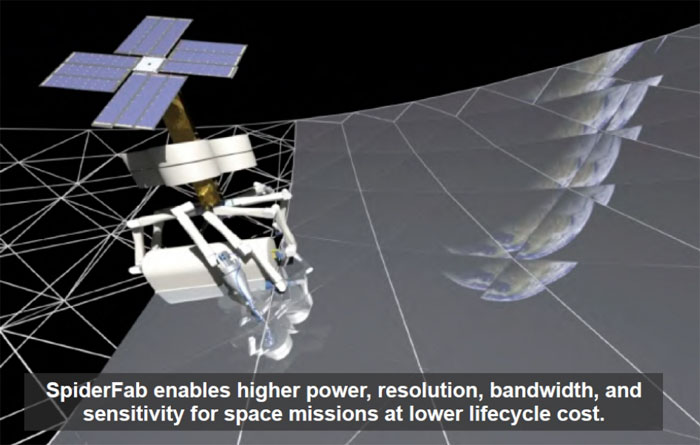
Currently, satellites are built and tested on the ground, and then launched into space aboard rockets. As a result, a large fraction of the engineering cost and launch mass of space systems is required exclusively to ensure the system survives the launch environment. This is particularly true for systems with physically large components, such as antennas, booms, and panels, which must be designed to stow for launch and then deploy reliably on orbit. Furthermore, the performance of these systems are largely determined by the sizes of their apertures, solar panels, and other key components, and the sizes of these structures are limited by the requirement to stow them within available launch shrouds. Current State-Of-the-Art (SOA) deployable technologiess enable apertures, baselines, and arrays of up to several dozen meters to be stowed within existing launch shrouds. However, the cost deployables increases quickly with increased size, driven by the complexity of the mechanisms required to enable them to fold up within the available volume as well as the testing necessary to ensure they deploy reliably on orbit. As a result, aperture sizes significantly beyond 100 meters are not feasible or affordable with current technologies.
The SpiderFab effort has investigated the value proposition and technical feasibility of radically changing the way we build and deploy spacecraft in order to escape the size constraints and cost scaling of current space systems. The vision that has motivated this effort is that of creating a satellite ‘chrysalis’, composed of raw material in a compact and durable form, ‘software DNA’ assembly instructions, and the capability to transform itself on-orbit to form a high-performance operational space system. SpiderFab enables this transformational capability by adapting additive manufacturing techniques and robotic assembly technologies to fabricate and integrate large space systems on-orbit. Fabricating spacecraft components on-orbit enables order-of-magnitude increases in packing efficiency and structural performance. These improvements will enable NASA to escape the volumetric limitations of launch shrouds to create systems with extremely large apertures and very long baselines. The larger solar panels, antennas, booms, concentrators, and optics created with SpiderFab will deliver higher power, higher resolution, higher bandwidth, and higher sensitivity for a wide range of missions. Our Phase I analyses have established that on-orbit fabrication changes the cost equation for large space systems, enabling apertures to scale to hundreds or even thousands of meters in size while providing order-of-magnitude improvements in system performance-per-cost.
The transition potential of the SpiderFab concept is demonstrated by the fact that our Phase I NIAC effort has already resulted in a successful transition to post-NIAC efforts under a NASA/LaRC SBIR to further develop a process for on-orbit fabrication of support structures for high-power solar arrays. The proposed Phase II NIAC effort will build upon this success by developing and demonstrating methods to address the key risk of fabrication in the thermal and vacuum environment of space. It will also develop to PDR-level a concept design for a mission to demonstrate on-orbit fabrication and integration of a large RF aperture, and establish the value proposition for this capability by comparing key performance-to-cost metrics relative to conventional deployable technologies.
These Phase II SpiderFab efforts will enable a game-changing transition from the current method of deploying space systems, where we build, qualify, and launch a product unique to each mission, to one where we qualify and launch one process that can be used many times to reduce life-cycle costs, risks, and schedule for wide range of NASA missions.
Quelle: NASA
4239 Views