NASA's Orion spacecraft is just about ready to turn up the heat. The spacecraft's heat shield arrived at the agency's Kennedy Space Center in Florida Wednesday night aboard the agency's Super Guppy aircraft.
The heat shield, the largest of its kind ever built, is to be unloaded Thursday and is scheduled for installation on the Orion crew module in March, in preparation for Orion's first flight test in September 2014.
"The heat shield completion and delivery to Kennedy, where Orion is being prepared, is a major step toward Exploration Flight Test-1 next year," said Dan Dumbacher, NASA's deputy associate administrator for exploration systems development in Washington. "Sending Orion into space for the first time is going to give us crucial data to improve our design decisions and develop Orion to send humans on future missions to an asteroid and Mars."
The heat shield began its journey in January 2012 in Colorado, at Orion prime contractor Lockheed Martin's Waterton Facility near Denver. That was the manufacturing site for a titanium skeleton and carbon fiber skin that give the heat shield its shape and provide structural support during landing. They were shipped in March to Textron Defense Systems near Boston, where they were used in construction of the heat shield itself.
Textron installed a fiberglass-phenolic honeycomb structure on the skin, filled each of the honeycomb's 320,000 cells with the ablative material Avcoat, then X-rayed and sanded each cell to match Orion's design specifications. The Avcoat-treated shell will shield Orion from the extreme heat it will experience as it returns to Earth. The ablative material will wear away as it heats up during Orion's re-entry into the atmosphere, preventing heat from being transferred to the rest of the capsule.
"Many people across the country have poured a tremendous amount of hard work into building this heat shield," said Orion Program Manager Mark Geyer. "Their efforts are a critical part of helping us understand what it takes to bring a human-rated spacecraft back safely from deep space."
Before and during its manufacture, the heat shield material was subjected to arc-jet testing NASA's Ames Research Center in California and NASA's Johnson Space Center in Houston. Arc jets heat and expand gasses to very high temperatures and supersonic and hypersonic speeds, thus simulating the heating conditions that a returning spacecraft will experience.
The heat shield delivered to Kennedy will be used during Exploration Flight Test-1, a two-orbit flight that will take an uncrewed Orion capsule to an altitude of 3,600 miles. The returning capsule is expected to encounter temperatures of almost 4,000 degrees Fahrenheit as it travels through Earth's atmosphere at up to 20,000 mph, faster than any spacecraft in the last 40 years.
Data gathered during the flight will influence decisions about design improvements on the heat shield and other Orion systems, authenticate existing computer models, and innovative new approaches to space systems and development. It also will reduce overall mission risks and costs for future Orion missions, which include exploring an asteroid and Mars.
.
NASA’s Super Guppy aircraft takes off from Manchester, N.H., carrying the heat shield that will protect Orion on its first mission, Exploration Flight Test-1, to Kennedy Space Center for installation.
Image Credit: NASA
.
Update: 12.12.2013
.
NASA's Orion Spacecraft Heads Cross Country
.
A test version of NASA’s Orion spacecraft gears up to take a long road trip. Starting from NASA’s Langley Research Center in Hampton, Va., the mockup will take a four-week journey across the nation to Naval Base San Diego in California. There, the test article will be used to support NASA’s Underway Recovery Test in February 2014. The test will simulate the recovery of Orion during its first mission, Exploration Flight Test – 1 (EFT-1), scheduled for September 2014.
The uncrewed EFT-1 mission will take Orion to an altitude of approximately 3,600 miles above the Earth’s surface, reentering the atmosphere at a speed of over 20,000 miles per hour before landing in the Pacific Ocean.
During the recovery test in San Diego, the spacecraft will be set adrift in open and unstable waters, providing NASA and the Navy the opportunity to recover the capsule into the well deck of the USS San Diego. While deployed, the team will seek out various sea states in which to practice the capsule recovery procedure in an effort to build their knowledge base of how the capsule recovery differs in calm and rough seas and what are the true physical limits.
NASA and the Navy practiced recovery in calm seas during a Stationary Recovery Test in August where the spacecraft was set adrift in the waters of Naval Station Norfolk in Virginia and recovered into the docked well deck of the USS Arlington.
The Orion mockup will travel through Virginia, Tennessee, Arkansas, Texas, New Mexico, Arizona and then reach its final destination in California.
.
.
.
.
Quelle: NASA
.
Update: 15.12.2013
.
Raumschiff Orion On Tour
.
Update: 26.12.2013
.
Work on NASA’s New Orion Spacecraft Progresses as Engineers Pivot to 2014
Orion’s first mission, Exploration Flight Test-1, or EFT-1, is less than a year away now, and the team building the spacecraft is meeting milestones left and right as they prepare the vehicle for its debut.
The Orion crew module that will fly 3,600 miles above Earth on the spacecraft’s first mission is continuing to come together inside the Operations and Checkout Building at NASA’s Kennedy Space Center in Florida. Since the heat shield that will protect it from temperatures near 4,000 degrees Fahrenheit was delivered to Kennedy in early December, the Orion team has been preparing it for installation. They’ve placed it on a work stand and begun drilling the holes necessary to attach it to the module. The heat shield is scheduled be put in place in the spring.
Once the heat shield has done its job getting Orion through the Earth’s atmosphere after its two orbits around Earth, it will be up to the parachutes to do the heavy lifting, literally. A total of 11 parachutes will be used for various landing functions, but three main parachutes that together could almost cover a football field ultimately will slow Orion’s descent down to less than 20 miles per hour for the finale: a relatively gentle splashdown in the Pacific Ocean.
The three main parachutes that will be used for EFT-1 were installed on the vehicle this month. A crane lowered each of the 300-pound main parachutes into place near the top of the capsule, and technicians in clean suits fit them into their compartments. They’ll be deployed using three smaller pilot parachutes that pull them out after the preceding drogue parachutes have done the initial work of slowing the vehicle down.
While those activities are preparing the spacecraft in Florida, the rockets that will launch Orion into space are nearing completion in Decatur, Ala., home of United Launch Alliance’s final assembly facility. The core, port and starboard boosters of the Delta IV heavy lift rocket that will be used for EFT-1 are all final assembly, with the starboard section leading the charge. It’s currently in final acceptance testing, while the RS-68 engine was recently installed on the core booster, and the propulsion and wire harness assemblies are being integrated into the port booster.
The rocket is scheduled to be completed and shipped to Florida in the spring.
With all this activity wrapping up 12 months of arrivals, installations and tests, 2013 has been a good year for the Orion Program. In fact, the only thing that could top it would be 2014 and the launch of EFT-1.
.
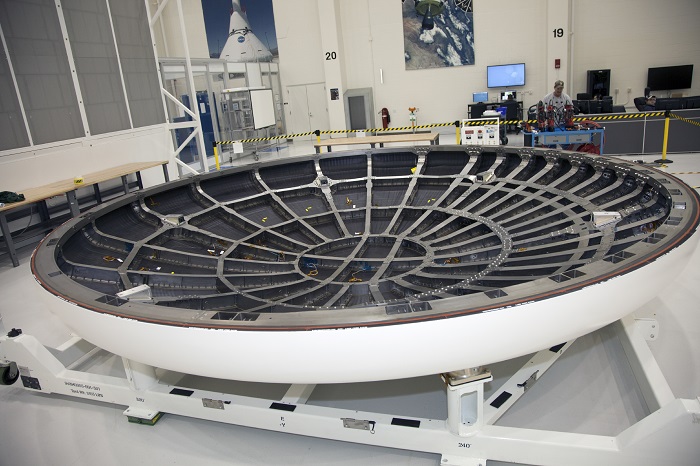
The heat shield for the Orion spacecraft has been placed on a work stand inside the Operations and Checkout Building high bay at NASA’s Kennedy Space Center in Florida.
Image Credit:
NASA/Mike Chambers
.
The Delta IV Heavy Lift rocket that will be used for Orion’s first mission, Exploration Flight Test-1, is in the final assembly area at United Launch Alliance’s factory in Decatur, Ala.
.
.
Engineers testing the parachute system for NASA's Orion spacecraft increased the complexity of their tests Thursday, Jan. 16, adding the jettison of hardware designed to keep the capsule safe during flight.
The test was the first to give engineers in-air data on the performance of the system that jettisons Orion's forward bay cover. The cover is a shell that fits over Orion's crew module to protect the spacecraft during launch, orbital flight and re-entry into Earth's atmosphere. When Orion returns from space, the cover must come off before the spacecraft's parachutes can deploy. It must be jettisoned high above the ground in order for the parachutes to unfurl.
"This was a tough one," said Mark Geyer, Orion program manager. "We'd done our homework, of course, but there were elements here that could only be tested in the air, with the entire system working together. It's one of the most complicated tests that we'll do, so we were all excited to see it work just as it was meant to."
Previous parachute tests at the U.S. Army's Yuma Proving Grounds in Arizona tested the performance of the parachutes in various conditions without a forward bay cover. Adding the cover and its jettison, along with the deployment of three additional parachutes to pull the cover away from the crew module and lower it to the ground, added a level of complexity to the testing.
"The parachute deployment and forward bay cover jettisons are two of the most difficult things for us to model on computers," said Chris Johnson, project manager for the parachutes. "That's why we test them so extensively. These systems have to work for Orion to make it safely to the ground, and every bit of data we can gather in tests like these helps us improve our models and gives us more confidence that when we do it for real, we can count on them."
The forward bay cover is jettisoned using a thruster separation system built by Systima Technologies Inc. of Bothell, Wash. Lockheed Martin, prime contractor for Orion, tested the system for the first time on the ground in December. Two more ground tests will simulate different types of stresses on the cover, such as a potential parachute failure or loads on the spacecraft. NASA also plans a second airborne test with the forward bay cover to evaluate its performance with a failed parachute.
Orion will be put to its first test in space during its first mission, Exploration Flight Test-1(EFT-1), in September. EFT-1 will have an uncrewed Orion launch to an orbit 3,600 miles above Earth, well beyond the distance traveled by spacecraft built for humans in more than 40 years. After circling Earth twice, Orion will re-enter the atmosphere at speeds as fast as 20,000 mph before the parachute system slows it down for a splashdown in the Pacific Ocean.
.
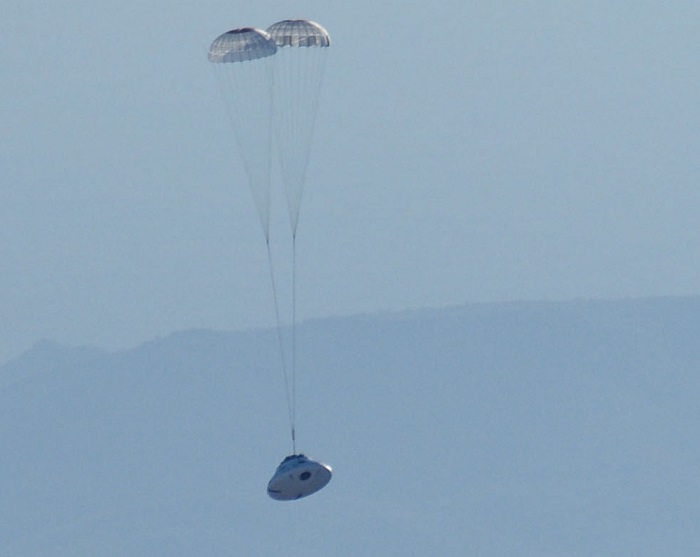
A test version of NASA’s Orion spacecraft floats through the sky about the U.S. Army’s Yuma Proving Ground in Arizona under the two drogue parachutes that precede the release of its three main parachutes.
Image Credit:
NASA
.
A test version of NASA’s Orion spacecraft touches down in the Arizona desert after its most complicated parachute test to date.
.
Update: 21.01.2014
.
ESA chief says Orion service module will be ready in 2017
The head of the European Space Agency says he has promised NASA the service module for the Orion crew exploration capsule will be delivered in time for an unmanned test flight by the end of 2017 despite problems with mass and development delays.
The service module's preliminary design review, a major developmental milestone in which engineers assess the maturity of the spacecraft's design, was delayed late last year from November to the spring.
Jean-Jacques Dordain, ESA's director general, told reporters Friday the design review will kick off at the beginning of April and run until May 15.
"The delay is linked to a number of technical problems, including mass-related issues," Dordain said.
But Dordain said he has assured NASA the six-month delay will not affect the service module's delivery schedule.
"I have undertaken to NASA that the delay in the PDR will not lead to any delay of the delivery of the service module," Dordain said Friday.
The service module is the Orion crew capsule's propulsion and power element and is based on Europe's Automated Transfer Vehicle, a robotic resupply freighter for the International Space Station.
Technicians will assemble the service module at Airbus Defence and Space's facility in Bremen, Germany, the site of ATV integration. Airbus will ship the service module to the Kennedy Space Center in Florida for attachment to the Orion crew vehicle built by Lockheed Martin Corp.
The European-built propulsion section has a height and diameter of about four meters, or 13 feet.
The schedule calls for the service module's arrival in Florida by the first quarter of 2017, but Dordain and Thomas Reiter, ESA's human spaceflight division chief, said the plan will be reassessed in June following the completion of the preliminary design review.
In a Jan. 10 interview, Reiter said engineers have made good progress on the service module's design documentation in the last few weeks.
Despite the delay of the PDR, Reiter said ESA will authorize Airbus Defence and Space to start procurement of "long-lead items which are more or less independent of the outcome of the PDR."
"We are trying to be as flexible and creative as possible," Reiter said.
ESA is ordering service module work to Airbus in slices and is waiting to award the next big contract, known as the Phase C/D contract, after the preliminary design review.
The PDR delay "cuts down the time we have to prepare our C/D contract with industry, but it's achievable," Reiter said.
The flight at the end of 2017 will be the first full-up space mission for the Orion multipurpose crew vehicle, but it will not carry astronauts. The spacecraft will blast off on NASA's heavy-lift Space Launch System, a mega-rocket under development using recycled and redesigned space shuttle technologies.
.
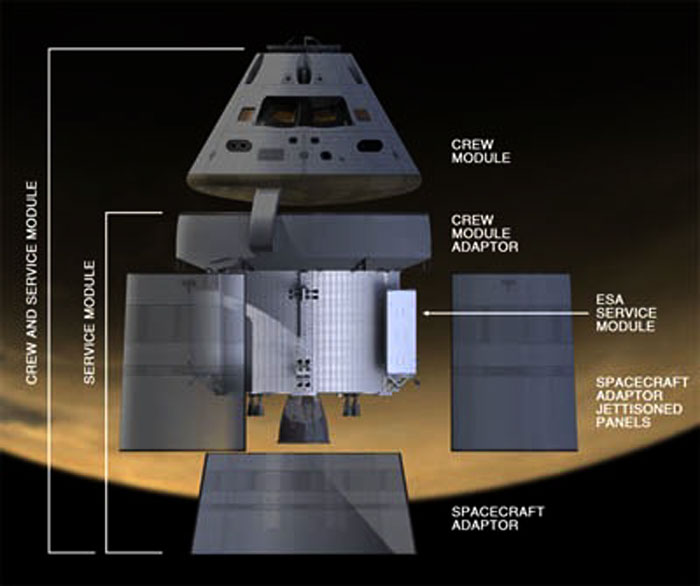
Diagram of the key components of the Orion spacecraft. Photo credit: NASA
.
The 2017 flight, known as Exploration Mission 1, is planned to conduct a lunar fly and enter a so-called "distant retrograde orbit" about 43,000 miles from the moon.
The 2017 test flight, planned to last more than three weeks, will be a pathfinder for NASA's asteroid redirect mission, an effort to send a robotic spacecraft into deep space and guide a 500-ton rock to a stable location near the moon for visits by human crews aboard the Orion spacecraft. The first crewed flight to an asteroid is expected no sooner than 2021.
A partially-functional Orion crew module will launch on an unmanned test flight in Earth orbit in September on-board a United Launch Alliance Delta 4-Heavy rocket. This year's test flight will not include a European service module.
European industry is designing and building the service module's primary structure, power-generating solar arrays, and hardware for the craft's main propulsion system. NASA is providing an orbital maneuvering system engine from the space shuttle program.
ESA and NASA agreed on the service module contribution in a barter agreement for Europe to pay for its share of the space station's operating costs. ESA pays for its part of the space station by providing in-kind services, such as cargo transportation with the Automated Transfer Vehicle.
The service module initiative is valued at 450 million euros, or more than $600 million, and pays for ESA's share of the station's costs from 2017 to 2020.
ESA's member states signed off more than half of service module's 450 million euro budget at a meeting in November 2012. Member states will meet again in December to approve the rest of the funding.
Quelle: SN
.
Update: 23.01.2014
.
At Your Service: Orion Service Module Complete
.
The second of three major parts of the spacecraft that will launch into orbit on Orion’s first mission this fall is complete.
Work has been progressing steadily on all three main parts of Orion – the service module, the crew module and the launch abort system – and this month the service module joined the launch abort system in crossing the finish line.
Orion’s service module sits below the crew module and above the rocket that will launch Orion into space. The recently completed service module, which will fly during Orion's first test flight, is a structural representation and will lack many of the key capabilities of the final service module. Service modules on future missions will provide power, heat rejection, the in-space propulsion capability for orbital transfer, attitude control and high-altitude ascent aborts. It will also house water, oxygen and nitrogen for the trip. But because Orion’s first mission will be a four-hour-long, unmanned flight test, many of those systems aren’t needed just yet. Instead, this first service module will primarily be responsible for the structural support involved in carrying the crew module and launch abort system as they’re launched into space.
Since the crew module and launch abort system together weigh more than 37,000 pounds at liftoff, that’s no easy task. The crew module gets some help with it from three massive panels, called fairings, that encase the service module and shield it from heat, wind and acoustics. They support half of the crew module and launch abort system’s weight during launch and ascent, before they’re jettisoned more than 100 miles up. After that, the loads on Orion are much lower and can be carried by the service module alone.
To ensure that the service module and its fairings are up to the challenge, it will spend two weeks in February undergoing tests. Engineers will carefully apply small amounts of stress to the structure to test its stiffness and verify it reacts as predicted. If it does, they’ll up the ante, pushing and twisting it from multiple directions.
If it can withstand the strain, the engineers will know it’s ready for flight.
The launch abort system was completed in December, and the crew module is coming right along. Engineers at Kennedy Space Center recently completed the complex welding that’s required to make sure Orion’s propulsion and life support fluid systems are leak tight.
To minimize the number of mechanical joints, which are invitations for leaks, the fluid systems are welded together as one piece into a virtual spaghetti bowl that surrounds the Orion pressure vessel. The process required more than 260 individual welds in complicated geometries, each of which was then X-rayed to ensure that it was good.
Over the next three months, Orion’s thermal protection system will be installed – tiles on the top of the crew module and the largest heat shield of its kind ever built. With that in place, the crew module, service module and launch abort system will be ready to mate this spring.
.
Engineers prepare Orion’s service module for installation of the fairings that will protect it during launch this fall when Orion launches on its first mission. The service module, along with its fairings, is now complete.
Image Credit: NASA
.
The fairings that will protect it during launch are added to Orion’s service module at the Operations and Checkout facility at Kennedy Space Center.
Image Credit: NASA
.
Engineers work on Orion’s crew module inside a temporary clean room set up inside the Operations and Checkout facility at Kennedy Space Center. Welding on the crew module was completed this month.
Image Credit: NASA
.
Quelle: NASA
HOUSTON, Feb. 13, 2014 -- Boeing's [NYSE: BA] Commercial Crew Program (CCP) recently completed a hardware design review and software safety test, bringing it closer to launching the Crew Space Transportation (CST)-100 spacecraft that will return Americans to space. A portion of the CST-100 spacecraft's integrated system testing is shown during testing at United Launch Alliance's System Integration Lab.
.
HOUSTON, Boeing's [NYSE: BA] Commercial Crew Program (CCP) recently completed a hardware design review and software safety test, bringing it closer to launching the Crew Space Transportation (CST)-100 spacecraft that will return Americans to space.
Boeing completed a Critical Design Review for the the system's Launch Vehicle Adapter (LVA), which connects CST-100 to the United Launch Alliance Atlas V rocket. The CDR, which included wind tunnel tests verifying flight stability, confirmed that the LVA design is suitable for production.
Separately, the Atlas V rocket's emergency detection system, which communicates with the capsule and initiates emergency procedures, if needed, passed its evaluation.
"Safety is a key element of the CST-100, from the drawing board to design implementation and beyond," said John Mulholland, vice president and program manager, Boeing Commercial Programs. "These tests help to validate that the launch vehicle adapter and emergency detection system are fully functioning and able to ensure a safe launch for our future passengers."
These two milestones are part of NASA's Commercial Crew Integrated Capability (CCiCap) agreement with Boeing. Next in line for the program is a software review this spring and the more comprehensive Integrated CDR this summer. Boeing is on track to meet all 20 of its CCiCap milestones in 2014.
.
.
.
.
Quelle: Boeing
.
Update: 19.02.2014
.
Orion Underway Recovery Testing Begins off the Coast of California
Preparations are underway to load a test version of the Orion crew module on a U.S. Navy ship in San Diego, California, for an underway recovery test in the Pacific Ocean.
.
About a hundred miles off the coast of San Diego, in the Pacific Ocean, a U.S. Navy ship’s well deck filled with water as underway recovery operations began Feb. 18 on a test version of NASA's Orion crew module to prepare for its first mission, Exploration Flight Test-1, in September. Orion was undocked from its cradle and allowed to float out to sea.
Building on the knowledge gained from previous Orion recovery tests performed in calm waters near NASA's Langley Research Center in Virginia, the agency's Ground Systems Development and Operations (GSDO) Program began the next phase, seeking turbulent water off the west coast in which to practice recovering the Orion crew module, one parachute and a forward bay cover, which keeps Orion's parachutes safe until being jettisoned, just before the parachutes are needed.
“This is an end-to-end test that takes us to the edge of our safe zone,” said Mike Generale, the Orion recovery operations manager and test director at NASA's Kennedy Space Center in Florida. “It will help us see how successful our processes and hardware are to recover Orion in higher sea swells.”
During the recovery test, controllers at Johnson Space Center in Houston simulated the launch and splash down of the Orion capsule. An F-18 jet flew from 13,000 feet into a dive to simulate Orion’s descent through the atmosphere and splashdown, as Johnson confirmed tracking and cleared the air space. Helicopters were stationed in the air to observe the “Orion capsule” during descent, as they would be during an actual retrieval mission.
The ship circled around to the floating test vehicle, and an integrated team of U.S. Navy amphibious specialists, engineers and technicians from Kennedy, Johnson and Lockheed Martin Space Operations practiced retrieving Orion, the forward bay cover and parachute.
A sea anchor and recovery winch was attached to Orion. The recovery winch attachments were secured between Orion’s two main windows, near the heat shield.
For the underway recovery test, even though there are no propellants or coolant on the capsule, the small boat teams examined Orion for leaks, just as they will following Exploration Flight Test-1. Then, two rigid-hull inflatable boats and two smaller Zodiac boats were used to help guide Orion into the Navy ship’s flooded well deck and secure it in a specially designed cradle. Water was drained from the well deck, leaving Orion secure and dry.
Two more rigid-hull inflatable boats were used to secure and reposition the recovered forward bay cover and parachute to the port side of the Navy ship where a crane lifted them on the ship’s main deck.
Generale said the underway recovery test allows GSDO to verify recovery operations and procedures, demonstrates capabilities and incorporates partnership efforts with the U.S. Navy and Lockheed Martin.
“The next steps will be to incorporate lessons learned and, if needed, modify Orion recovery hardware,” Generale said.
The underway recovery test will continue through Feb. 21.
Quelle: NASA
.
Update: 22.02.2014
.
Above: This Wednesday Feb. 19, 2014 photo released by NASA shows a test version of the Orion spacecraft, tethered inside the well deck of the USS San Diego prior to testing between NASA and the U.S. Navy.
.
A training exercise designed to showcase the government's ability to recover a space capsule at sea was scrubbed after NASA ran into trouble off the Southern California coast, the space agency said Friday.
Crews had difficulty tying down a mock-up of the Orion capsule aboard an amphibious warship off the shores of San Diego.
NASA said cables attached to the capsule weren't strong enough to handle turbulence and snapped off twice while it was in the well deck of the USS San Diego before it could be moved out to sea on Thursday.
With the Orion mock-up still on the Navy ship, teams could not practice fetching the spacecraft from the ocean.
"Even though the testing didn't go as we had planned, we're learning lessons that will help us be better prepared to retrieve Orion," Bill Hill of NASA headquarters said in a statement.
Engineers were troubleshooting the problem, and it was not clear when the test would be rescheduled.
NASA has been developing a next-generation spacecraft to carry astronauts beyond low-Earth orbit, possibly to an asteroid or Mars. Orion, which will make its first unmanned test flight this fall, is being designed to travel to deep space and return at speeds of 25,000 mph by splashing down into the Pacific.
The water landing is a throwback to the 1960s and 1970s when Navy ships routinely tracked and recovered Mercury, Gemini and Apollo spacecraft after re-entering Earth's atmosphere.
With the space shuttle fleet retired, NASA has decided to go with an ocean splashdown. Unlike in the past, when helicopters would hoist astronauts after a mission, the new plan calls for an amphibious transport ship to dispatch divers and small boat teams to recover Orion and its crew.
Last year, NASA and the Navy practiced recovering the Orion in the calm waters of the Elizabeth River in Virginia with no problem.
Before the latest test was called off, NASA said crews successfully retrieved parts of the spacecraft, including the parachute and a protective covering.
NASA Administrator Charles Bolden was supposed to visit the test site Saturday, but his appearance was canceled.
.
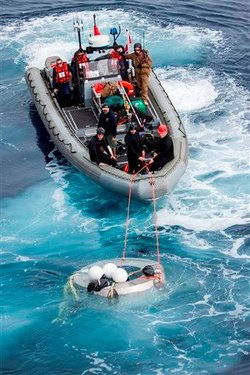
This Wednesday, Feb. 19, 2014 photo released by NASA shows crews testing a test version of Orion's forward bay cover, NASA's next-generation space capsule.
Quelle: KPBS
.
Update: 25.02.2014
.
Two Boosters Complete for Orion Spacecraft's First Flight Test
.
Two of the boosters that will help send NASA’s Orion spacecraft into space for the first time are on their way to Florida.
Orion will launch on top of a Delta IV rocket this fall, and two of the rocket’s three boosters were rolled out of the United Launch Alliance (ULA) facility in Decatur, Ala., and loaded onto a Mariner cargo barge Feb 21.
ULA is constructing the Delta IV for the flight test of Orion, called Exploration Flight Test-1, or EFT-1. From ULA, the boosters will arrive at Cape Canaveral, Fla., in early March for final processing prior to the launch. A third booster is still in fabrication at the Decatur facility.
"This is a very exciting time for NASA," said Bill Hill, NASA assistant deputy associate administrator for exploration systems. "EFT-1 is a big milestone for us, and is the start of venturing further into space than we ever have before. Seeing these rocket boosters roll out headed for the Cape is a testament of the hard work taking place to help further NASA’s space exploration goals.”
During the flight test, Orion will travel 3,600 miles into space -- farther than a spacecraft built for humans has been in more than 40 years -- and orbit the Earth twice. The capsule will re-enter Earth’s atmosphere at speeds approaching 20,000 mph, generating temperatures as high as 4,000 degrees Fahrenheit, before splashing down in the Pacific Ocean.
The uncrewed flight will provide engineers with important data about Orion's heat shield and other elements, including the spacecraft adapter’s performance. The spacecraft adapter will connect Orion to the Delta IV and also will connect Orion to NASA’s new rocket, the Space Launch System (SLS), on its first mission in 2017. The adapter was completed earlier this month at NASA’s Marshall Space Flight Center and will be delivered to ULA in mid-March. SLS, NASA's new rocket, will be capable of taking humans to deep space missions, including Mars.
“NASA and our partners have worked very hard to get Orion ready for EFT-1,” said Paul Marshall, NASA’s Orion assistant program manager. “It truly is a team effort, and that has been showcased here today. We really can’t wait to see Orion fly this fall on the Delta IV, and use that data to get us ready for the first SLS flight in 2017.”
.
One of the Delta IV Heavy boosters that will be used in Orion’s launch this fall is turned around for loading onto the Mariner cargo barge.
.
One of two completed boosters for the Delta IV Heavy rocket that will launch Orion on its first flight to space this fall is loaded onto a barge for transport to Cape Canaveral, Fla.
Quelle: NASA
.
Update: 28.02.2014
.
Engineers Continue Pushing Orion Parachute System to Its Limits
.
The parachute system designed for NASA’s Orion spacecraft passed another hurdle on Feb. 26, in a test that put extra stress on its drogue parachutes and simulated a failure of one of its three main parachutes.
Engineers dropped a dart-shaped test vehicle that simulates Orion’s parachute compartment from a C-17 flying 35,000 feet above the U.S. Army’s Yuma Proving Ground in Arizona. Although one test has been conducted from that height before, this was the first using the dart-shaped vehicle at that altitude. Using it along with test configuration parachutes to get it into place for the test put more stress than ever before on the two drogue parachutes that precede the main parachutes and begin the job of slowing Orion down before it lands.
“We are trying to push these parachute to the extreme limits,” said Chris Johnson, project manager for the parachutes. “We want to explore all of the boundaries possible, so that we know we can count on them when it really matters and get our astronauts home safely.”
This test verified that the drogue parachutes will perform successfully during the most extreme speed, altitude and pressure loads they would see in a mission, providing invaluable information to add to the computer models used to design the system that will allow crews in Orion to splashdown safely in the Pacific Ocean.
“As much as we’d like to, we can’t actually test every imaginable scenario,” Johnson said. “But the more data we have, the better our models and the more confident we can be that we’ve covered all of our bases.”
The additional information increases engineers' confidence that they can accurately virtually simulate an array of scenarios. During this test, engineers repeated the failure of one of the three main parachutes from a previous test to provide more data and opened the two main parachutes at different rates from previous tests to assess a design improvement. They also were able to use three forward bay cover parachutes as programmers to set the test up, which allowed them to obtain more data on those parachutes, even though no cover was used during the test.
Testing Orion's parachutes will ensure that the system is dependable when the spacecraft reenters Earth's atmosphere. Orion’s first flight to space is scheduled to launch this fall. After an uncrewed, two-orbit flight, the spacecraft will return to Earth at speeds approaching 20,000 mph. Traveling through the Earth’s atmosphere will slow it down dramatically, before the parachutes deploy and bring Orion in for a splashdown at only about 20 mph.
The next parachute test, set for April 23rd, will skip the drogue parachutes altogether, demonstrating a launch abort scenario that relies only on the three main parachutes to slow the spacecraft safely.
.
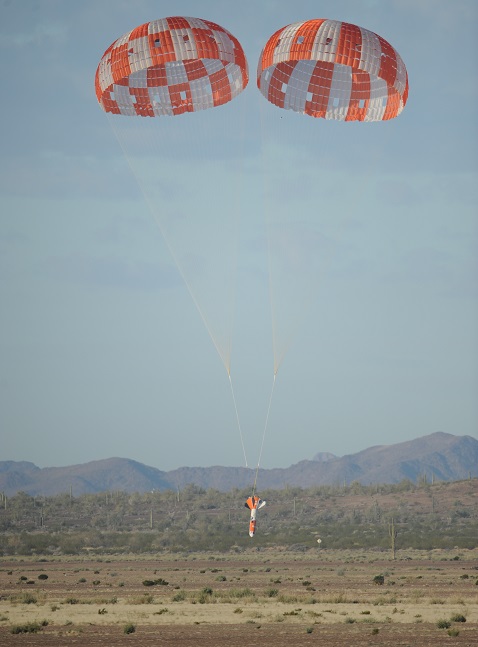
A dart-shaped test vehicle that simulates Orion’s parachute compartment touches safely down on the U.S. Army’s Yuma Proving Ground using only two of Orion’s three main parachutes. The parachute test simulated a failure of the third parachute.
Quelle: NASA
.
Update: 13.03.2014
.
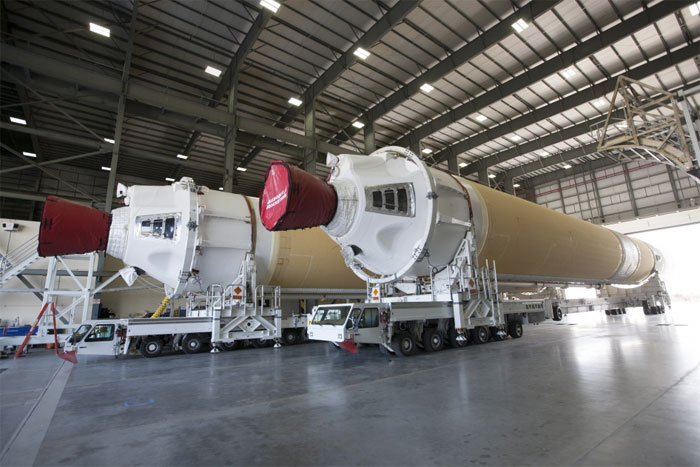
Boosters for Orion Spacecraft's First Flight Test Arrive at Port Canaveral, Florida
.
A barge arrives at the U.S. Army Outpost wharf at Port Canaveral in Florida, carrying two of the three United Launch Alliance Delta IV heavy boosters for NASA’s upcoming Exploration Flight Test-1 (EFT-1) with the Orion spacecraft. The core booster and starboard booster will be offloaded and then transported to the Horizontal Integration Facility, or HIF, at Space Launch Complex 37 on Cape Canaveral Air Force Station. The port booster and the upper stage are planned to be shipped to Cape Canaveral in April. At the HIF, all three boosters will be processed and checked out before being moved to the nearby launch pad and hoisted into position.
Orion is the exploration spacecraft designed to carry astronauts to destinations in deep space, including an asteroid and Mars. It will have emergency abort capability, sustain the crew during space travel and provide safe re-entry from deep space return velocities. During the uncrewed EFT-1 flight, Orion will travel 3,600 miles into space -- farther than a spacecraft built for humans has been in more than 40 years -- and orbit the Earth twice. The capsule will re-enter Earth’s atmosphere at speeds approaching 20,000 mph, generating temperatures as high as 4,000 degrees Fahrenheit, before splashing down in the Pacific Ocean. The data gathered during the flight will influence design decisions, validate existing computer models and innovative new approaches to space systems development, as well as reduce overall mission risks and costs for later Orion flights.
Quelle: NASA
.
Update: 15.03.2014
.
Orion Makes Testing, Integration Strides Ahead of First Launch to Space
.
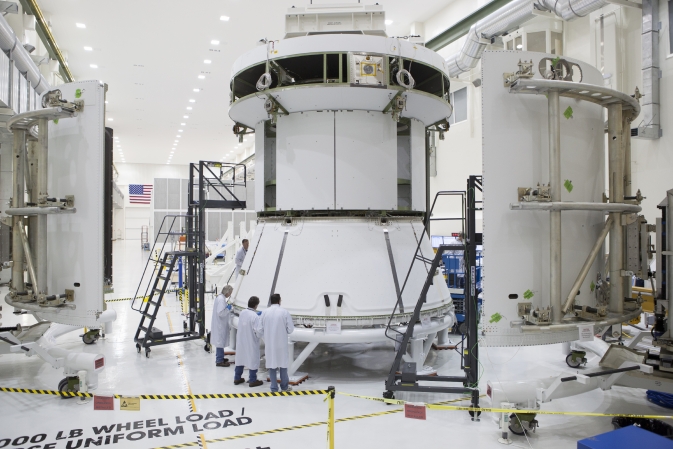
Engineers prepare Orion’s service module for installation of the fairings that will protect it during launch this fall when Orion launches on its first mission. The service module, along with its fairings, is now complete.
.
Orion is marching ever closer to its first trip to space on a flight that will set the stage for human exploration of new destinations in the solar system.
The Orion team continues to work toward completing the spacecraft to be ready for a launch in September-October. However, the initial timeframe for the launch of Exploration Flight Test-1 (EFT-1) has shifted from September-October to early December to support allowing more opportunities for launches this year. Completing the spacecraft according to the original schedule will allow many engineers and technicians to continue transitioning to work on the Orion spacecraft that will fly atop the agency's Space Launch System. It will also ensure that NASA's partners are fully ready for the launch of EFT-1 at the earliest opportunity on the manifest.
To that end, the core and starboard boosters for the United Launch Alliance Delta IV Heavy rocket that will launch Orion into space for the first time arrived at Cape Canaveral Air Force Station this month. That leaves just one booster still in production at the company's Decatur, Ala., facility. It's scheduled to arrive in April along with the rocket's upper stage, and will join the other boosters inside ULA's Horizontal Integration Facility for processing and testing.
Meanwhile, in the spacecraft factory at Kennedy Space Center - the Operations and Checkout Facility - Orion itself is making progress of its own.
After completing construction on the service module in January, engineers at Kennedy moved on to testing whether it could withstand the stresses that it will endure during launch and in space. The service module sits below Orion's crew module and above the rocket, and would normally provide power and in-space propulsion and house a number of other systems that aren't needed on this first flight. Despite being pushed and twisted in multiple directions, the service module came through the tests not only unscathed, but earlier than planned.
Once the service module testing was completed, it was the crew module's turn.
Almost all of the spacecraft's avionics components have been installed, and system by system, the engineers are powering them up. It's a methodical, deliberate process, in which each connector is checked individually before they're hooked up and the system turned on to make sure each battery, heater, camera and processor - to name a few - works on its own, before the entire system is turned on together. Otherwise, one faulty cable could damage an entire, one-of-a-kind system.
The process is called functional testing, and once it's complete and all 59 systems have been verified, the engineers will graduate to performance testing, in which all of the systems work together to operate the crew module as a whole. Ultimately, they'll be able to turn on all of the flight computers, radios and other systems at once and simulate the vehicle's sensors so that the spacecraft thinks its flying in space.
The crew module testing will wrap up in April, and then Orion's heat shield - the largest of its kind ever built - will be installed. With that in place, the crew module, service module and launch abort system will be ready to mate this spring. Its launch later this year will send Orion 3,600 miles above the Earth for a two-orbit flight that will give engineers the chance to verify its design and test some of the systems most critical for the safety of the astronauts who will fly on it in the future. After traveling 15 times farther into space than the International Space Station, Orion will return to Earth at speeds near 20,000 mph, generating temperatures of up to 4,000 degrees Fahrenheit, before splashing down in the Pacific Ocean.
Quelle: NASA
.