2.07.2020
Boeing gives Starliner crew capsule's parachutes a workout in drop test
Starliner's chutes continue to perform.
The parachute system that helps bring Boeing's Starliner crew capsule safely back to Earth just passed another test.
Starliner's chutes performed well during a drop test over New Mexico's White Sands Space Harbor last week that was designed to simulate an abort shortly after launch, Boeing representatives said Monday (June 29).
"Parachutes like clean air flow," Boeing flight conductor Jim Harder said in a statement.
"They inflate predictably under a wide range of conditions, but in certain ascent aborts, you are deploying these parachutes into more unsteady air where proper inflation becomes less predictable," Harder said. "We wanted to test the inflation characteristics at low dynamic pressure so we can be completely confident in the system we developed."
A Starliner test article was dropped from a balloon high in the New Mexico sky on Sunday, June 21. Six seconds after the drop, small chutes deployed as planned, lifting away the capsule's forward heat shield. Shortly thereafter, the vehicle's two drogue parachutes kicked in, deploying successfully despite the low pressure, Boeing representatives said.
Then, 98 seconds post-drop, two pilot chutes fired, pulling out two of Starliner's three main parachutes. The test team kept the third main chute stowed by design, introducing a "fault scenario" for the system to overcome.
The two deployed main chutes did their job, helping the test article land softly in the New Mexico desert about 4 minutes after the drop, Boeing representatives said. (This scenario mirrored what happened during Starliner's November 2019 "pad abort" test, but on that earlier occasion the plan had been for all three of the main parachutes to deploy.)
"Our parachutes have passed every test," Starliner test manager Dan Niedermaier said in the same statement. "We continue to push our system because we know what's at stake. This demanding test program ensures Starliner can bring our astronauts home safe."
Boeing has been developing Starliner with funding help from NASA's Commercial Crew Program and will use the capsule to fly agency astronauts to and from the International Space Station (ISS).
Starliner is in the late stages of its test program. The capsule has already made one trip to space, an uncrewed December 2019 mission called Orbital Flight Test (OFT). OFT didn't go as planned; Starliner suffered a glitch with its onboard timing system and got stranded in the wrong orbit, preventing a meetup with the ISS. The capsule did ace its landing, however, touching down softly in New Mexico under parachute.
Starliner will fly another version of OFT, likely sometime late this year, before taking astronauts aboard on a test flight to the space station.
SpaceX holds a NASA commercial crew deal of its own, which it will fulfill using its Crew Dragon capsule and Falcon 9 rocket. Crew Dragon has already flown successfully to the ISS twice, first on an uncrewed test flight in March 2019 and again on the Demo-2 demonstration mission, which launched on May 30 of this year.
Demo-2 took NASA astronauts Bob Behnken and Doug Hurley to the orbiting lab, where they remain today. It's unclear how much longer the duo will stay in orbit; NASA officials said shortly before launch that Demo-2 will last one to four months end to end, and they have yet to get more specific than that.
If all continues to go well with Demo-2, SpaceX's first contracted commercial crew mission for NASA could launch as early as Aug. 30.
Boeing will continue to test Starliner's parachutes throughout this summer, putting the system through its paces in a variety of conditions, NASA officials said.
Quelle: SC
----
Update: 4.07.2020
.
EGS, Jacobs begin SLS booster build up for Artemis 1
NASA Exploration Ground Systems and prime test and operations contractor Jacobs mated the first of two Space Launch System (SLS) aft motor segments for the Artemis 1 launch with its aft skirt on June 24.
The connection of two of the major elements of the right-hand aft booster assembly continues preparations of Northrop Grumman booster hardware for the first SLS launch tentatively scheduled for late next year.
First aft assembly mate for build up
The two aft motors and two aft skirts were delivered to the Rotation, Processing and Surge Facility (RPSF) in mid-June to begin readying them for eventual stacking on Mobile Launcher-1 in the Vehicle Assembly Building at the Kennedy Space Center later this year. Following rail transportation from Utah, Jacobs and Exploration Ground Systems (EGS) removed the aft motors from their railcars, rotated them to a vertical orientation, and mated them to the aft skirts in build up stands in the RPSF.
Nozzle extensions, also known as exit cones, and other hardware will be added to the aft motor and skirt to complete build up of the aft booster assemblies so they are ready to stack by the end of the Summer. Roll from the RPSF to the Vehicle Assembly Building (VAB) for stacking will then wait until after the Core Stage hot-fire test at the Stennis Space Center in Mississippi, tentatively scheduled for this Autumn.
For build-up, the right-hand aft solid rocket motor segment for Artemis 1 was lifted into one of the build up stands where the bottom case of the aft segment was mated to the top of the aft skirt. The lift and mate on June 24 followed a week of initial offloading and receiving inspections after arrival of the ten solid rocket motor segments by train from their production facility in Promontory, Utah.
SLS Booster prime contractor Northrop Grumman delivered almost all the Artemis 1 Solid Rocket Booster (SRB) hardware to EGS in mid-June, with the two completed aft skirts transported from the Booster Fabrication Facility at KSC to the RPSF a few days before the motor segment train arrived in Florida.
The two SRB exit cones were delivered to EGS late in 2019; all that remains to be delivered for the boosters are the forward assemblies, which are nearly complete and being closed out for handover in the Booster Fabrication Facility.
The ten motor segments compose the two, five-segment solid rocket motors (RSRMV) at the heart of the SLS Boosters. The RSRMV is an evolution of the Space Shuttle Reusable Solid Rocket Motor (RSRM) design; originally selected to be the first-stage of the Constellation Program’s Ares I Crew Launch Vehicle, after Constellation was cancelled the design was adopted for SLS in 2011. The Shuttle RSRM had four segments: the forward, forward-center, aft-center, and aft segments. The RSRMV adds an additional center-center segment in the middle of the motor.
Processing of the boosters in the RPSF began with the two aft segments. The two boosters are being assembled by combining the ten motors with the two sets of aft skirts, exit cones, forward assemblies, and other hardware.
Most of the assembly is done during stacking operations on the Mobile Launcher in the VAB, but several of the major booster elements are part of the aft booster assemblies, and those are integrated in the RPSF as a prerequisite to start stacking.

Credit: NASA/Ben Smegelsky.
(Photo Caption: Two overhead cranes in the Rotation/Processing Building of the RPSF begin lifting the right aft motor segment off its transportation railcar on June 19. The train from Utah with all ten Artemis 1 solid rocket motor segments arrived in Titusville on June 12 and the segment cars were moved onto KSC on June 15. Processing started with the right aft motor car the next day.)
“We preposition the aft skirt; we then mate the aft segment to the skirt, and we go through a series of operations to make it the aft booster assembly by installing things like the Core Stage attach ring. We have some [Development Flight Instrumentation] that we need to install, we have cable harnesses we need to run, thermal curtain installation on the bottom of the aft skirt,” Jeffrey Angermeier, EGS Flow Director, explained in a recent interview.
The RPSF is composed of four buildings in an area just north of the VAB outside the crawler-transporter tracks. The work to prep the segments for stacking is performed in the Rotation/Processing Building. “If you think about the footprint in the rotation building, there are kind of four permanent structures that we have,” Angermeier explained.
“We have what we call two aft booster assembly build up stands, and we also have what we call two inspection stands. Then we have a series of pedestals that we use for some inspections right after we take it off the railcar.”
In addition to the Rotation/Processing Building, the RPSF includes two Surge buildings, or garages, for storing motor segments ready for stacking, along with a support building.
Following arrival of the motor segment train, the cars with the two aft segments were detached and moved to the Rotation/Processing Building for Jacobs and EGS to begin their work. The two aft booster assemblies are staged in the build up stands there, with the aft skirts set up there first.
While the aft skirts were being staged in the build up stands, the aft motor segment railcars were rolled into the Rotation/Processing Building one at a time for offloading. The clamshell shipping cover was removed from the railcar and then the covers bolted onto both ends of the segment were removed.
“The end covers of the right aft motor segment were removed to allow for grain inspections of the solid propellant,” Kerry Chreist, Jacobs RPSF Flow Manager, said.

Credit: NASA/Ben Smegelsky.
(Photo Caption: The right aft motor segment is moved towards its inspection stand pedestals on June 23. The segment was first rotated from its horizontal orientation for shipping to vertical for processing at KSC.)
Following initial inspections, two overhead cranes were attached to the forward and aft ends of the motor for the breakover operation, where the segment was offloaded from the railcar and rotated. “After you lift it off of the railcar, you go from horizontal to vertical,” Angermeier said.
“Then you’ll position the segment on top of a pedestal. We have a pedestal that is used for the aft motor segments, then we have pedestals that we can use for all the other segments.”
The aft motor segment has a dome on the bottom that the other four do not; the forward segment has a dome on the top. “We have an accommodation to the roundness of the bottom of the segment for the aft [segments] to allow us to go do what we need to go do there,” Angermeier noted.
Following more inspections, a single crane lifted the aft motor into one of the build up stands for attachment to the aft skirt. “As we attach the aft motor segment to the aft skirt, we pin those together and then there’s a closeout that we have to do with a pin band that we would put around that joint,” Angermeier said.
In addition to connecting the aft motor, aft skirt, and exit cone, a lot of work goes into integrating electrical, mechanical, and thermal protection systems for the aft booster assembly.
Angermeier further outlined some of the work after the aft motor segment is attached to the aft skirt. “One of the first things that we do is we will install the aft exit cone,” he said. “We received one in November and one in December of 2019, so they’ve been here ready.”
“We will attach that exit cone, we’ll do a leak check, and then we’ll close out the joint and we’ll do things like if there’s any painting of bare metal and there’s a nozzle sealant application and the cure we have to do with that.” The aft skirt also houses the booster’s hydraulic thrust vector control (TVC) system, and the two hydraulic actuators will also be attached to the full-length nozzle.
“Once we get done with that, then we get into the Core Stage Attach ring installation,” he continued. “That is the structural ring that goes around that aft motor segment that we will use to attach to the Core Stage.”

Credit: NASA.
(Photo Caption: Composite slide graphics from a NASA presentation showing the SLS Booster configuration and aft booster assembly elements. Some of the changes for the aft assembly elements made from the heritage Shuttle hardware and design to Ares I to SLS are also highlighted.)
“What we will do is we will install the struts; there’s three struts on each side. You have the upper, the lower, and the diagonal struts, so there will be a total of six, three per each booster. And that’s how you’ll attach the boosters to the lower part of the Core Stage.”
Each of the two SLS Boosters attach in two locations to the Core Stage. At their aft end, they are bolted to a structural ring built into the barrel of the Core Stage’s engine section; at their forward end they attach to either side of a thrust beam that runs through the middle of the intertank.
In contrast to the aft assembly for the four-segment Shuttle boosters, where the attach ring was located at the top of the motor segment, for the SLS five-segment boosters, the ring is located twenty feet lower on the aft segment, closer to the aft skirt. The inline SLS configuration has the nozzles for the liquid engines and solid motors close together compared to the Shuttle orbiter that was side-mounted farther above the exit plane of the boosters.
“Once we get that ring installed, then there are electrical harnesses that we have to run through the [Core Stage Attach] ring,” Angermeier added. “Additionally, there’s some Development Flight Instrumentation with some thermocouplers and other instrumentation that we have to run. And that Development Flight Instrumentation, we also have to go through a checkout to make sure that it’s working properly.”
“In parallel with that, we’re working underneath installing the thermal curtain. Also on the bottom part of the aft skirt, we have our ground umbilical plate that provides all the electrical feed from the ground up through the booster. We install the ground plate up to the flight plate; we install that in the Rotation building.”
In addition to connecting electrical cabling for operational and development flight instrumentation laid out all over this first flight vehicle, Angermeier noted that the ordnance lines to explosively separate the boosters from the Core Stage during launch will also be connected.
“There is some ordnance lines, some firing lines, that we install and checkout over in the Rotation building,” he explained. “That’s the separation ordnance for the three struts that we have on the [Core Stage Attach] ring.”
There is also some ground test instrumentation that needs to be installed on this first SLS vehicle for more pre-launch development tests. “We also have modal sensors that we will install on the aft motors; we do that in the build up stand,” Angermeier said.
“When we’re in the VAB we have the Integrated Modal Test that we have to do for the full vehicle. We have ninety-one sensors that we have to install on the two boosters while the booster segments are in the Rotation building, and so for the ones that we have to install on the aft motor, we do that in the build up stand.”
“And basically we have a series of closeouts on the [Core Stage Attach] ring and other parts of that booster assembly,” he noted. “Once we’re done with the fully integrated aft booster assembly, we’ll keep that in the build up stands until we need those over in the VAB once we commit to stacking.”
“So when we need them over in the VAB, we’ll lift it out of the build up stand, we will put it on a transportation pallet, and then we’ll use one of our transporters to take it over to the VAB, and we’ll commit to stacking.”

Credits: NASA/Kim Shiflett.
(Photo Caption: A composite of images from the start of right-hand aft segment lifting operations on June 24. After being set on the inspection stand pedestals, a lifting ring was disconnected from the aft end of the segment to prepare for the mate with the aft skirt. The segment was then lifted by one of the overhead cranes still attached to the forward lifting ring off the pedestals and into the build up stand for mating to the right-hand aft skirt.)
After both aft segments are offloaded from their railcars and installed in the build up stands in the Rotation/Processing Building, the rest of the segments will be brought to the building for offloading. “All the other segments, they come off the railcar and they go over to that pedestal like I mentioned before,” Angermeier said. “There’s a few operations that we do on the pedestal, and then we lift it and put the segment on top of a pallet that’s in what we call one of two inspection stands.”
Center and forward segments will be stored in the nearby Surge buildings of the RPSF until it is their turn for stacking in the VAB.
Stacking flight hardware on the Mobile Launcher will not begin until completion of the Core Stage test-firing at the end of the ongoing Green Run test campaign.
Spaceport facility sharing
The train carrying the 10 Artemis 1 live solid rocket motor segments from Promontory to KSC also included cars with two inert motor segments for the commercial OmegA launcher under development by Northrop Grumman. The company is planning OmegA’s first launch next year, and launch operations share multiple Launch Complex 39 facilities that EGS uses for SLS launch operations.
“One thing we’ve been working on within our program and with [KSC is] doing everything we can to make it a multi-user spaceport. And there is a lot of activity as you can see with SpaceX and their activities out at Pad A and then with Northrop Grumman and their OmegA rocket,” Angermeier said.
OmegA includes segmented solid rocket motor stages at its base. As with the SLS Boosters, they will be received and processed in the RPSF following rail transportation from the same Utah production facilities.
“The thing that we work with Northrop Grumman is a shared use of the facilities; it really comes down to when do the two programs need flight hardware elements processed and ready for use,” Angermeier said. “The facilities that they’re utilizing are managed by the Exploration Ground Systems program, the program that I work for.”
“We have daily integration meetings and they are part of those meetings and we do everything we can to make sure that the two programs can co-exist and not create any schedule impacts for either program. We worked with Northrop Grumman to understand their schedule and when they need those segments offloaded.”

Credit: NASA/Ben Smegelsky.
(Photo Caption: Jacobs personnel stand under the left-hand aft skirt in one of two build-up stands in the RPSF on June 23. Surrounded by an environmental enclosure, the inside of the aft skirt houses thrust vector control (TVC) components from hydraulic actuators to hydraulic power units to avionics boxes. Both aft booster assemblies will be integrated side-by-side in the RPSF build up stands this Summer.)
“It turns out that the timing when they need those is after we offload all the Artemis 1 segments. And so in our schedule right now we plan to get all the segments offloaded for Artemis 1 in the August time-frame, and then once we’re done with those in mid- to late-August, that’s the tentative schedule to offload the OmegA segments,” he said.
As with SLS launch processing, OmegA motor segments will be stacked on a separate mobile launcher in the VAB. EGS will integrate SLS vehicles in the northeast High Bay 3 cell of the VAB while Northrop Grumman will integrate OmegA vehicles in the southwest High Bay 2 cell.
As with the RPSF, the two programs will also synchronize operations and share ground support equipment in the VAB. “It’s a lot of integration,” Angermeier said. “We do have five major cranes in the building, but you can only have one major lift going on at a time in the building.”
“Whenever you lift a segment that’s not inert, a segment that has propellant in it, you have to clear the entire building. We have worked with Safety and there will be some operations that we may be able to do in parallel in the Vehicle Assembly Building while we’re lifting the segments. But generally speaking, we could not be lifting an Artemis 1 booster segment while they are lifting an OmegA segment up into High Bay 2.”
Stacking starts with the aft assemblies
While waiting to stack the flight hardware on Mobile Launcher-1 in VAB High Bay 3, EGS and Jacobs will run through one more practice session with inert motor hardware. Over the past two years, segment-to-segment mating exercises were performed “offline” in VAB High Bay 4, where SLS motor segments will go for final preparations to be lifted into the integration cell.
During previous practice periods, Mobile Launcher-1 was still under construction and going through checkout activities in and around the VAB; EGS and Jacobs will now get a chance to run through stacking procedures with the ML in High Bay 3. “Right now we have it tentatively set for early-August,” Angermeier said. “We have about two weeks of operations practicing stacking.”
“They have been practicing a lot of the joint mating activities offline in High Bay 4 with one of the stands that we have over there. Our plan to stack it on the ML is we will stack the aft motor inert and then we’ll stack an inert center segment on top of that.”
“Then we’ll destack that inert center segment, lift the aft motor assembly off one set of support posts and put it on the other one and then we’ll stack the inert center on top of that one again. So basically we’re going to work on both Vehicle Support Posts (VSP) with the [inert] aft booster, so we’ll get a chance to essentially mate that first joint twice up on the ML in August.”
Following roll on a transportation pallet from the RPSF to the VAB, most segments will go through a similar sequence of final stacking preparations in High Bay 4. “For the non-aft segments, we have to place it over the slap stand, and we do our operations to ensure that the lower part of that segment (tang) from a roundness perspective is going to fit nicely with the clevis part on the segment that’s already up in the High Bay,” Angermeier said.

Credit: NASA/Glenn Benson.
(Photo Caption: NASA EGS and Jacobs technicians practice segment lifting and field joint mating operations with inert hardware in VAB High Bay 4 in January. On the left, an inert center segment is lifted to practice mating its bottom, clevis end to the top, tang end of an empty, bare metal segment case. On the right, another bare metal cylinder is mated to an inert aft assembly in one of the build up stands used early in the Shuttle program. The inert aft assembly and inert center segment will be used to practice stacking and mating operations on Mobile Launcher-1 in High Bay 3 later in the Summer.)
“So we lift off the pallet, we position over what we call the slap stand, we do the inspection of the lower mating joint. We do the alignment [check], and then once we get the go from engineering that we have good alignment between the clevis and the tang, we will lift and go up and over and commence the mating operation over in High Bay 3.”
“For the [aft] segments they will just roll into the center part of High Bay 4, we’ll attach the 384-beam and we’ll go up and over.”
In contrast to when they were used on Shuttle SRBs, the aft booster assemblies will not be held down for launch. “With Shuttle what we had is a system where the nut was pyrotechnically split in two and then the bolt would fall into our hold down post and then the nut would fly with the boosters and then we would get it post-flight,” Angermeier explained.
“We do not have that on Artemis rockets, so when we stack it there’s no bolts that we attach to the support post and the aft skirt.” Non-pyrotechnic, non “T-zero” bolts will be used temporarily when the fully integrated vehicle is moved by a Crawler Transporter during rollout to the pad and rollback from the pad to the VAB.
“Prior to roll for Wet Dress, we clamp the boosters to the VSP using a nut/bolt similar to what we used in shuttle, eight total,” he explained. “When we get to the pad for Wet Dress, we will remove the bolts to rehearse what we will do following the launch rollout.”
“We will reinstall the bolts prior to rollback following WDR, and they will stay installed until we rollout for launch. They will be removed days prior to launch when we are at the pad. The boosters are heavy enough that we won’t have to worry about them moving around without bolts installed.”
Following roll on a transportation pallet from the RPSF to the VAB, most segments will go through a similar sequence of final stacking preparations in High Bay 4. “For the non-aft segments we have to place it over the slap stand and we do our operations to ensure that the lower part of that segment (tang) from a roundness perspective is going to fit nicely with the clevis part on the segment that’s already up in the High Bay,” Angermeier said.
“So we lift off the pallet, we position over what we call the slap stand, we do the inspection of the lower mating joint. We do the alignment [check] and then once we get the go from engineering that we have good alignment between the clevis and the tang and we will lift and go up and over and commence the mating operation over in High Bay 3.”
“For the [aft] segments they will just roll into the center part of High Bay 4, we’ll attach the 384-beam and we’ll go up and over.”
Quelle: NS
----
Update: 6.07.2020
.
Starliner Parachutes Perform Under Pressure
Boeing’s spacecraft completes another reliability test; shares data
Boeing put Starliner’s parachutes to the test again on June 21 as part of a supplemental reliability campaign designed to further validate the system’s capabilities under an adverse set of environmental factors.
Boeing is developing the Starliner spacecraft to take astronauts to and from the International Space Station in partnership with NASA’s Commercial Crew Program.
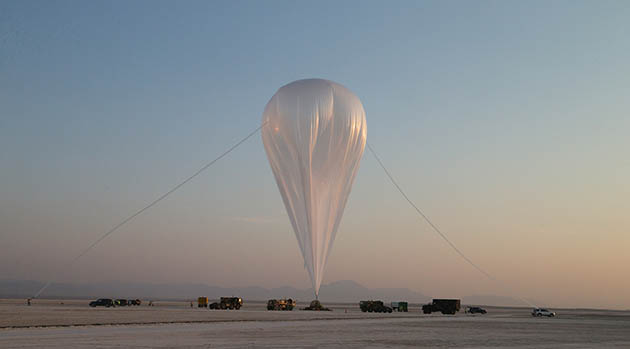
An inflated high altitude balloon hovers over the desert at White Sands Space Harbor in New Mexico on June 21 ahead of Boeing Starliner’s recent parachute reliability drop test.
BoeingThis latest balloon drop, conducted high above White Sands Space Harbor in New Mexico, demonstrates Starliner’s parachutes continue to perform well even under dynamic abort conditions and a simulated failure. Boeing and NASA jointly developed the conditions for this test as part of a comprehensive test campaign to demonstrate Starliner parachute performance across the range of deployment conditions.
Teams wanted to be sure that if an abort were to occur early into launch, certain parachutes in Starliner’s landing sequence would inflate correctly despite needing to deploy in significantly different flight conditions than those seen with normal landings.
“Parachutes like clean air flow,” said Jim Harder, Boeing’s flight conductor. “They inflate predictably under a wide range of conditions, but in certain ascent aborts, you are deploying these parachutes into more unsteady air where proper inflation becomes less predictable. We wanted to test the inflation characteristics at low dynamic pressure so we can be completely confident in the system we developed.”
This critical test phase began six seconds into the drop when small parachutes designed to lift away Starliner’s Forward Heat Shield deployed successfully. Ten seconds later, the vehicle’s two drogue parachutes followed suit, inflating perfectly despite the low dynamic pressure. But the Starliner boilerplate wasn’t out of the woods yet.
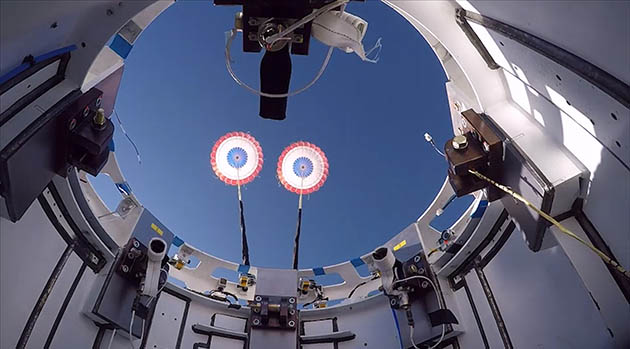
Two drogue parachutes successfully deploy from a Boeing Starliner test article during a landing system reliability test conducted on June 21 above White Sands Space Harbor in New Mexico.
BoeingTest teams added a fault scenario to the test objectives by preventing one of Starliner’s three main parachutes from deploying altogether. At 98 seconds into flight, just two pilot chutes were fired resulting in only two of the three main parachutes deploying. Despite the higher loading, Starliner’s parachutes performed effectively, bringing the test article down to Earth safely and slowly about two-and-a-half minutes later.
The data extracted from this test will be utilized to improve the reliability of the Starliner parachute system ahead of crewed flights and be shared with NASA for their own vehicle use.
“Our parachute system is very similar to the design NASA uses to bring humans safely back from the Moon. Turns out, we can use some of their test data to model our mission scenarios, and they can use a lot of our data to model theirs,” said Starliner test manager Dan Niedermaier. “It really is all about the data. The more you have, the more accurate your models will be. This shared approach helps to keep both systems incredibly safe.”
During the summer, Boeing and NASA will continue to test Starliner’s parachute strength, building out even more reliability on a system that’s already shown to be consistently robust.
“Our parachutes have passed every test.” Niedermaier said. “We continue to push our system because we know what’s at stake. This demanding test program ensures Starliner can bring our astronauts home safe.”
NASA’s Commercial Crew Program is a public-private partnership combining NASA’s experience with new technology and designs pioneered by private industry to make space travel safer and available for all. This test is one of many steps that advances NASA’s goals of returning human spaceflight launches to U.S. soil on commercially-built and operated American rockets and spacecraft, preparing for a human presence on the Moon, and ultimately sending astronauts to Mars.
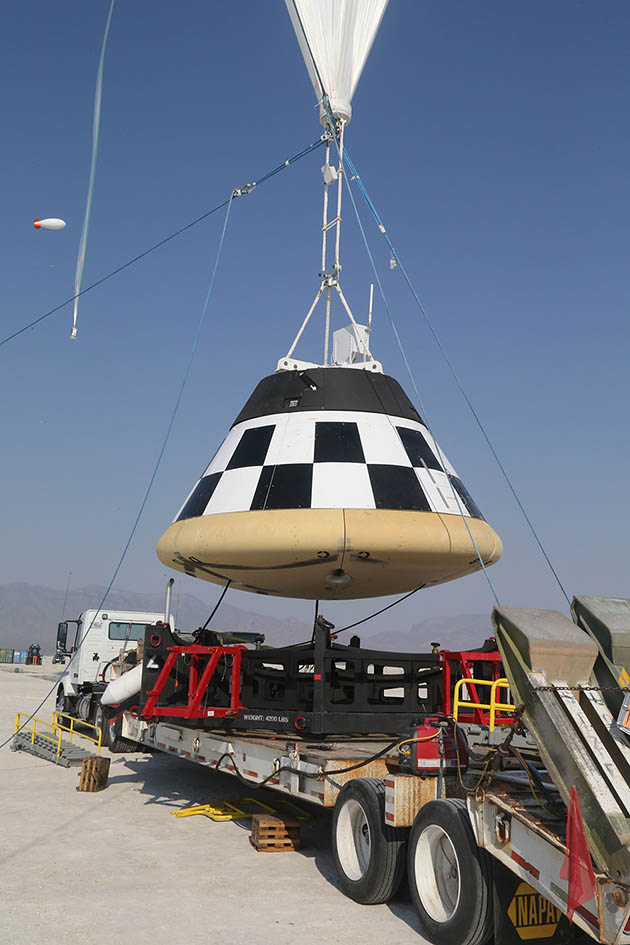
A Boeing Starliner boilerplate hangs from a high altitude balloon in preparation for launch during a recent parachute reliability test on June 21 at White Sands Space Harbor in New Mexico.
Quelle: Boeing
----
Update: 8.07.2020
.
NASA and Boeing Complete Orbital Flight Test Reviews
NASA and Boeing have completed major reviews of the company’s uncrewed Orbital Flight Test in December 2019 and are continuing with preparations to refly the test, designated Orbital Flight Test-2 (OFT-2), to the International Space Station as part of NASA’s Commercial Crew Program.
“NASA and Boeing have completed a tremendous amount of work reviewing the issues experienced during the uncrewed flight test of Starliner,” said Steve Jurczyk, associate administrator at NASA. “Ultimately, everything we’ve found will help us improve as we move forward in the development and testing of Starliner, and in our future work with commercial industry as a whole.”
The joint NASA-Boeing Independent Review team completed the final assessment into the intermittent space-to-ground communication issue detected during the first uncrewed Orbital Flight Test of Boeing’s Starliner spacecraft. The review team previously completed its investigation into the two other primary anomalies experienced during the test.
With the completion of the investigation’s third and final focus area, the review team identified a total of 80 recommendations that Boeing, in collaboration with NASA, is addressing, with action plans for each already well under way. Although the full list of recommendations is company sensitive and proprietary, the categories of the corrective and preventative actions are as follows:
- Testing and Simulation: 21 recommendations including the need for greater hardware and software integration testing; performance of an end-to-end “run for record” test prior to each flight using the maximum amount of flight hardware available; reviewing subsystem behaviors and limitations; and addressing any identified simulation or emulation gaps.
- Requirements: 10 recommendations including an assessment of all software requirements with multiple logic conditions to ensure test coverage.
- Process and Operational Improvements: 35 recommendations including modifications to change board documentation; bolstering required participants in peer reviews and test data reviews; and increasing the involvement of subject matter experts in safety critical areas.
- Software: 7 recommendations including updating the software code and associated artifacts to correct the Mission Elapsed Timer Epoch and Service Module disposal anomalies; and making the antenna selection algorithm more robust.
- Knowledge Capture and Hardware Modification: 7 recommendations such as organizational changes to the safety reporting structure; amending the Independent Verification and Validation (IV&V) approach; and the addition of an external Radio Frequency (RF) filter to reject out-of-band interference.
As a result of this work and Boeing’s separate analysis, the company proactively announced in April it would fly a second orbital test at no cost to the government to prove the Starliner system meets NASA’s requirements, including docking to the space station.
Boeing and NASA have asked the independent review team to remain engaged as a valuable and important partner in the Starliner’s path to crewed flight. Additionally, lessons learned from the Starliner’s first uncrewed flight test are being shared across the human spaceflight community to strengthen the industry as a whole.
“As vital as it is to understand the technical causes that resulted in the flight test not fulfilling all of its planned objectives, it’s equally as important to understand how those causes connect to organizational factors that could be contributors,” said Jurczyk. “That’s why NASA also decided to perform a high visibility close call review that looked at our combined teams.”
NASA has now also completed the high visibility close call investigation to specifically review the organizational factors within NASA and Boeing that could have contributed to the flight test anomalies. The close call investigation team, established in March, was tasked with developing recommendations that could be used to prevent similar close calls from occurring in the future.
The close call team built off the technical findings of the joint independent review team related to the software coding errors made during the development of the spacecraft. The team also received additional briefings, held subject matter expert discussions and conducted interviews across the organizations.
Based on the findings, the team developed the following recommendations for the NASA Human Exploration and Operations Mission Directorate to incorporate into future programs:
- Require that the systems engineering management plan delivered by each contractor contain specific requirements related to the contractor’s management approach.
- Ensure that NASA reviews and approves the contractor’s hazard verification test plans prior to test execution.
- Ensure NASA independent validation and verification (IV&V) teams provide insight to contractor IV&V agents.
- Implement an approach that ensures alternate standards are reviewed and approved prior to beginning development work.
- Develop a best practices document for use by future programs that implement the shared accountability model used in NASA’s Commercial Crew Program.
- Evaluate Boeing’s actions developed by the joint independent review team for applicability post-certification.
With the development of these recommendations, the high visibility close call investigation has concluded.
“I can’t stress enough how committed the Boeing team has been throughout this process,” said Phil McAlister, director of commercial spaceflight development at NASA. “Boeing has worked collaboratively with NASA to perform these detailed assessments. To be clear, we have a lot more work ahead, but these significant steps help us move forward on the path toward resuming our flight tests.”
Boeing and NASA have not yet established a launch date for OFT-2.
Quelle: NASA