9.08.2019
The most prominent launcher of small carbon composite rockets, Rocket Lab, announced plans on Tuesday to recover the first stage of their Electron rocket and eventually reuse the boosters on future launches.
In short, CEO Peter Beck very humbly stated that he would have to eat his hat during the ~30-minute presentation, owing to the fact that he has vocally and repeatedly stated that Rocket Lab would never attempt to reuse Electron. If Rocket Lab makes it happen, the California and New Zealand-based startup will become the second entity on Earth (public or private) to reuse the boost stage of an orbital-class rocket, following SpaceX’s spectacularly successful program of Falcon 9 (and Heavy) recovery and reuse.
WHAT IS ROCKET LAB?
Rocket Lab – headquartered in Huntington Beach, California – is unique among launch providers because they specialize in constructing and launching small carbon composite rockets that launch from the gorgeous Launch Complex 1 (LC-1) in Mahia, New Zealand. Their production facilities are located in Auckland, New Zealand, where they not only produce their own rockets but also 3D print Rutherford engines, the only orbital-class engine on Earth with an electric turbopump.
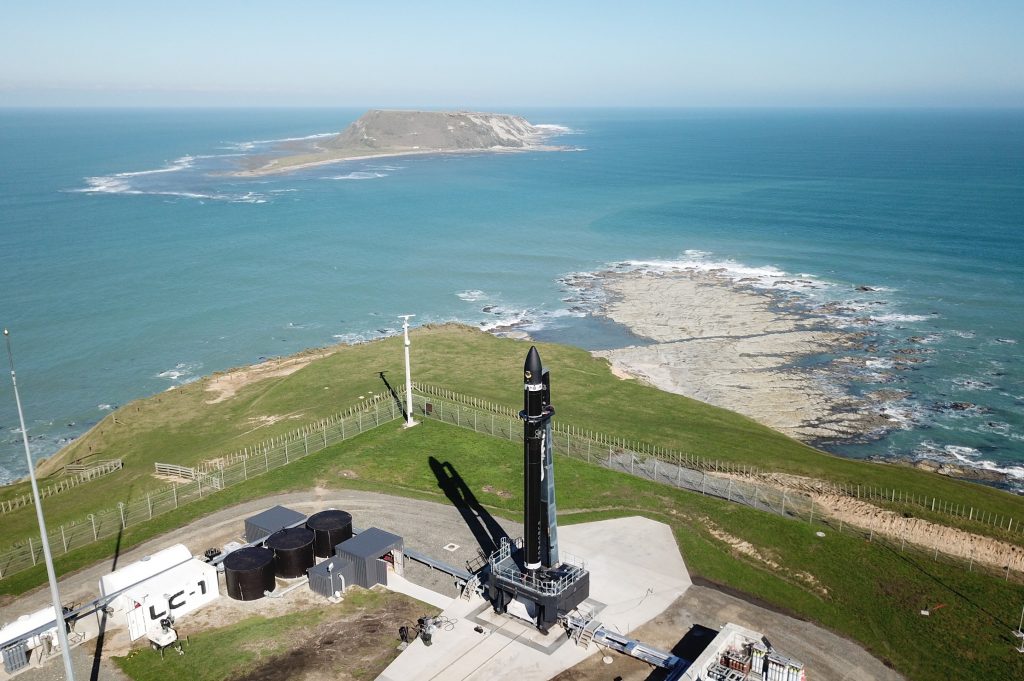
Electron’s 1.2-meter (4 ft) diameter body is built out of a super durable, lightweight carbon composite material that relies on custom Rocket Lab-developed coatings and techniques to function as a cryogenic propellant tank. It is powered by 9 liquid kerosene and oxygen (kerolox) Rutherford engines that rely on a unique electric propulsion cycle. The engine is also the only fully 3D-printed orbital-class rocket engine on Earth, with all primary components 3D-printed in-house at Rocket Lab’s Huntington Beach, CA headquarters. Pushed to the limits, a complete Rutherford engine can be printed and assembled in as few as 24 hours.
Currently, Rocket Lab is producing an Electron booster every 20-30 days and flies about once a month out of New Zealand. Since the first operational flight at the end of 2018 Rocket Lab has supported both commercial and government payloads. With a new launch complex (LC-2) coming online in Wallops, Virgina by the end of this year, they look to increase launch frequency, but also widen its market of customers. According to CEO Peter Beck, booster reuse could be a boon for Electron’s launch cadence.
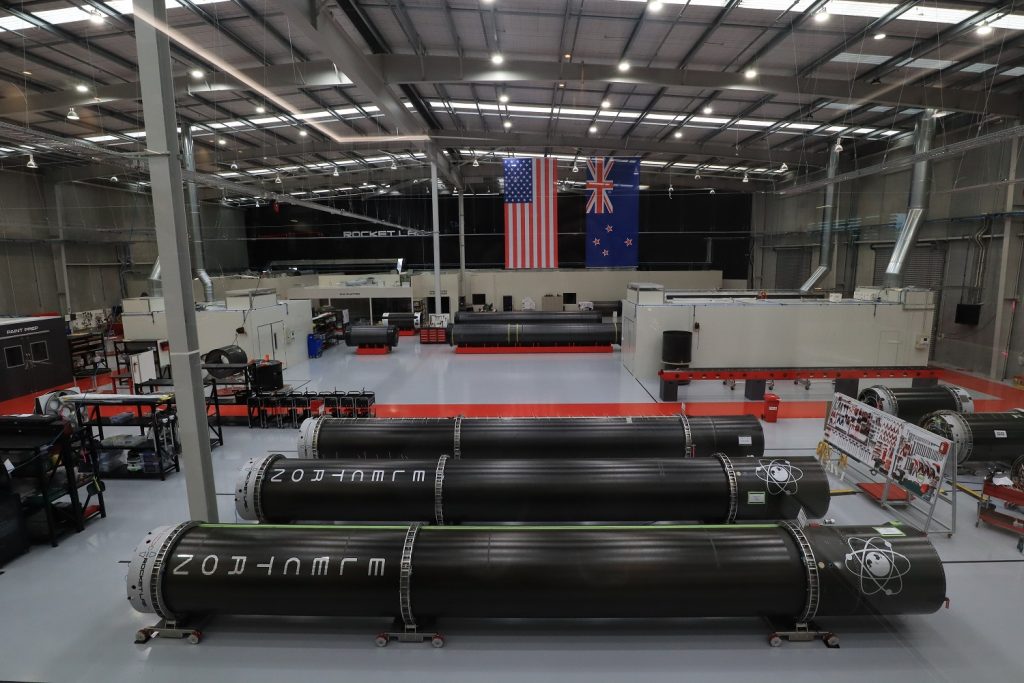
“ELECTRON, BUT REUSABLE.”
In the world of aerospace, SpaceX is effectively the only private spaceflight company (or entity of any kind) able to launch, land, and reuse orbital-class rockets, although other companies and space agencies have also begun to seriously pursue similar capabilities. Rocket Lab’s announcement certainly brings newfound interest to the private rocket launch community. Reuse of launch vehicle boosters – typically the largest and most expensive portion of any given rocket – is a fundamental multiplier for launch cadence and can theoretically decrease launch costs under the right conditions.
Rocket Lab hopes, more than anything, that recoverability will lead to an increase in their launch frequency and – at a minimum – a doubling of the functional production capacity of the company’s established Electron factory space. This will allow for more innovation and give the company more opportunities to “change the industry and, quite frankly, change the world,” according to founder and CEO Peter Beck.
Unlike like SpaceX’s Falcon 9, propulsive landing is not an option for the small Electron rocket. In fact, cost-effective recovery and reuse of vehicles as small as Electron was believed to be so difficult that Beck long believed (and openly stated) that Rocket Lab would never attempt the feat. Beck claims that in order to land a rocket on its end propulsively – by using engines to slow the booster while it hurdles back to Earth in the way the Falcon 9 booster does – would mean that their small rocket would have to scale up into the medium class of rockets. As Beck stated, “We’re not in the business of building medium-sized launch vehicles. We’re in the business of building small launch vehicles for dedicated customers to get to orbit frequently.”
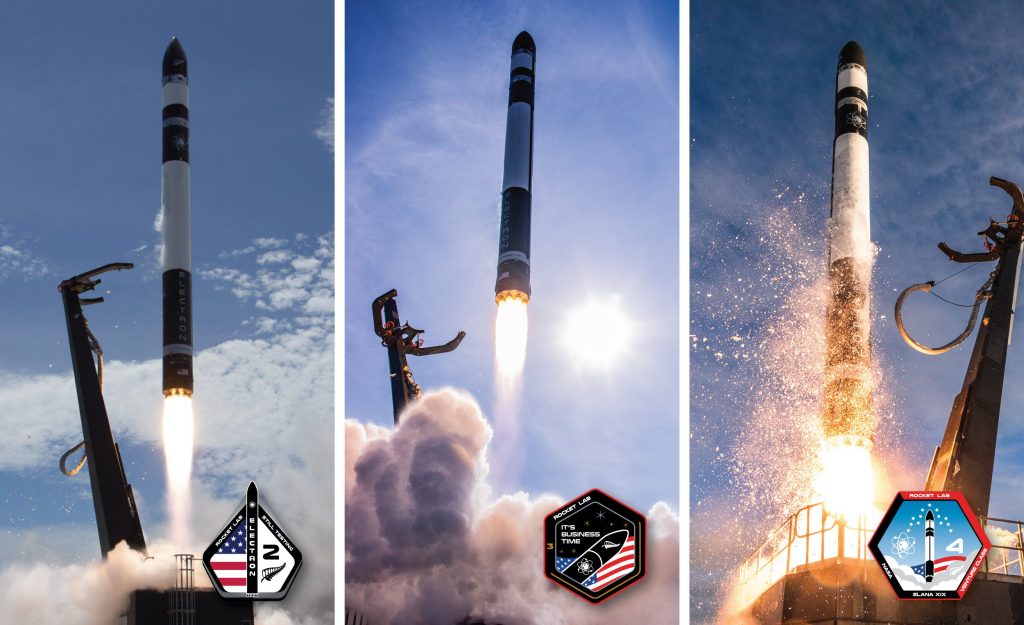
The main concern that Rocket Lab faces with the daunting task of not using propulsion to land is counteracting the immense amount of energy that the Electron will encounter on its return trip through the atmosphere. In order to return the booster in any sort of reusable condition they will have to decrease the amount of energy that the rocket is encountering which presents in the forms of heat and pressure from ~8 times the speed of sound to around 0.01 times the speed of sound. This decrease also needs to occur in around 70 seconds during re-entry and according to Beck “that’s a really challenging thing to do.” Beck went on further to explain that this really converts into dissipating about 3.5 gigajoules of energy which is enough energy to power ~57,000 homes.
BREAKING THROUGH “THE WALL”
When re-entering the atmosphere the energy that any spacecraft endures creates shockwaves of plasma which must be diverted away in order to protect the integrity of the spacecraft. An example of this can be seen during the re-entry of a SpaceX fairing half. Beck explains that “the plasma around those shockwaves is equal to about half the temperature of the (surface of the) sun” which can reach temperatures as high as 6,000 degrees fahrenheit. It also endures aerodynamic pressure equal to that of three elephants stacked on top of the Electron, according to Beck. His team refers to these challenges as breaking through “The Wall.”Beck explains that they will attempt to solve these problems differently using passive measures and aerodynamic decelerators.
The Wall is something that Beck and his team have been trying to tackle for some time now. Since the Electron began operational flights at the end of 2018 data has been collected to inform the problem solving process. In total Electron has successfully completed 7 flights, with its 8th scheduled to occur within the coming days. Beck explains that flights 6 and 7 featured data collection done through 15,000 different collection channels on board of Electron. The upcoming eighth flight will feature an advanced data recording system nicknamed Brutus. This new recording system will accompany Electron on the descent, but will survive while the booster breaks up as usual. It will then be collected and the data will be evaluated and used to further inform the decision making process for how to best help Electron survive its fall back to Earth.
CATCHING ROCKETS WITH HELICOPTERS
Once Rocket Lab breaks through The Wall and effectively returns Electron without harm, the booster will need to be collected before splashing down into corrosive saltwater. This was demonstrated to be done via helicopter which according to Beck is “super easy.”
An animation depicts a helicopter leaving a dedicated recovery vessel to capture the Electron booster after it deploys a parafoil and begins gliding. The helicopter will intercept the booster’s parachute using a hook and will then carry the booster back to the recovery vessel, where technicians will carefully secure it.
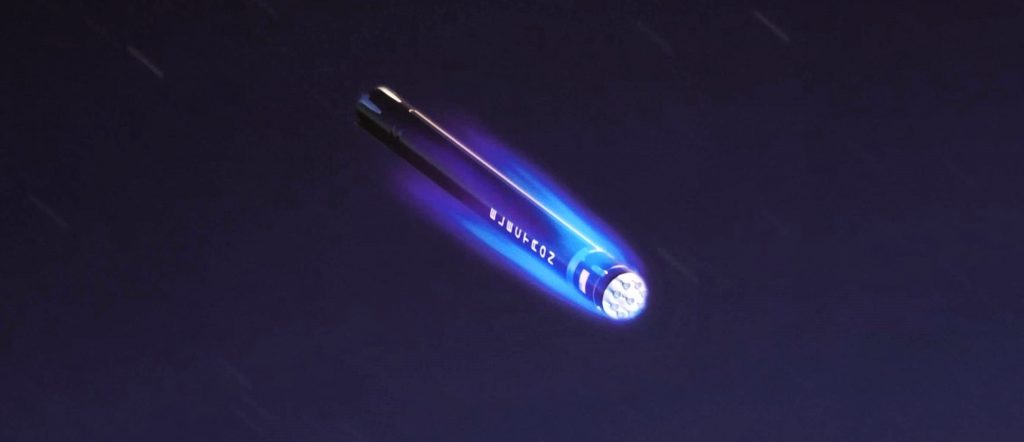
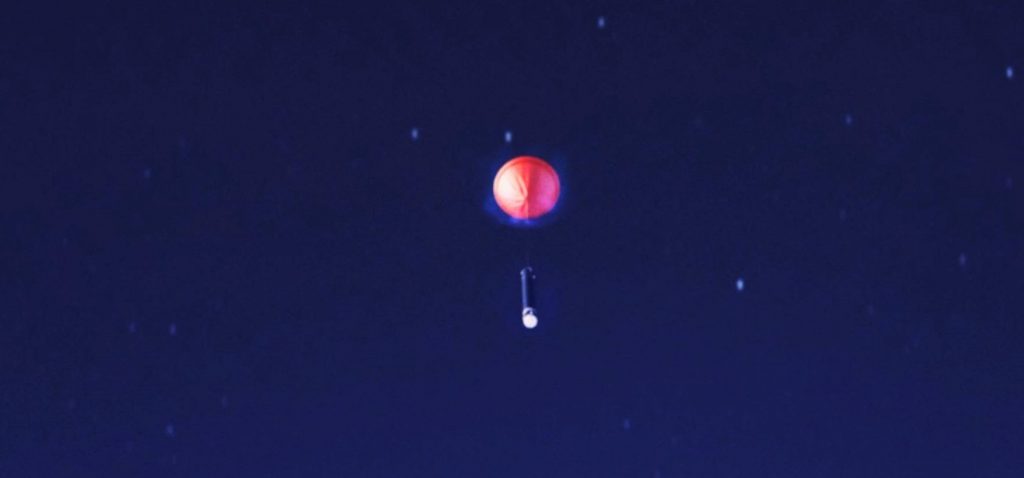
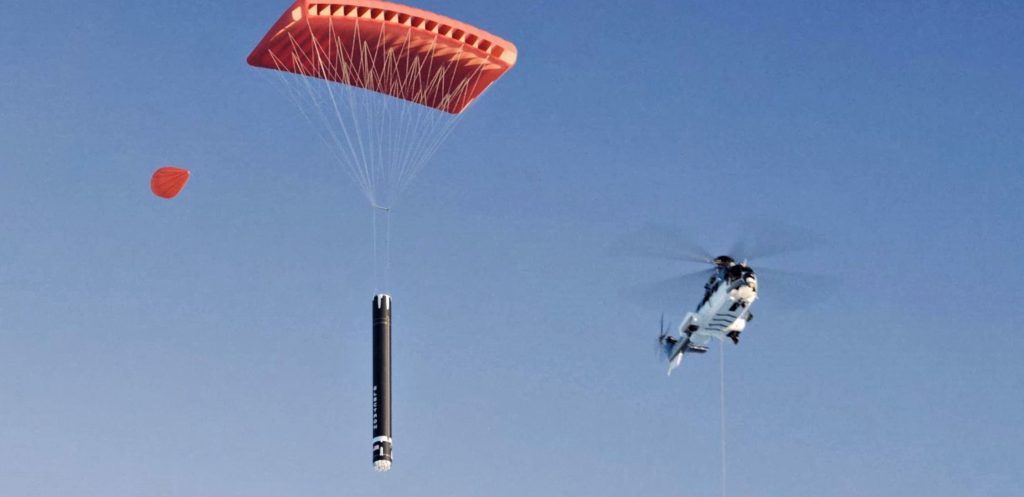
The entire goal of recovering a booster is to be able to reuse it quickly. Beck explains that since Electron is an “electric turbopump vehicle…in theory, we should be able to put it back on the pad, charge the batteries up, and go again.”
Although this goal is ambitious, it is one that – if achieved – will significantly impact the launch community in very positive ways. Not only will the option of rapid reusability open up, but so will opportunity for more agencies to engage in the world of satellite deployment. The Electron currently costs anywhere between $6.5 – 7 million per launch to fly. If the production cost of a new booster is removed space becomes attainable for many more customers.
Quelle: TESLARATI