21.04.2019
NASA Launch Services Program outlines the alternative launcher review for EM-1
Orion configuration considerations
“The thing that kept me up at night just gagging was the prospect of needing to shift twenty-five metric tons three kilometers per second out of low Earth orbit into trans-lunar injection,” Wood said. At the outset, one of the things the study group looked at was how they might reduce Orion’s mass to make it better fit one of their launcher options.
The twenty-five metric tons is the approximate in-space mass of Orion; however, the spacecraft launches with a massive, tractor rocket abort system that also serves as an aerodynamic fairing.
“The Launch Abort System and what they call the ogive shroud, those were items that I wanted to attack immediately because between the LAS and the ogive shroud and the tri-sector cylindrical aerofairing that’s ejected from around the Service Module in flight after dynamic pressure falls off, that was a lot of mass, that was on the order of twenty-thousand pounds mass or approaching ten metric tons on its own,” Wood noted.
“Not only is it mass that we think we didn’t need in flight — obviously we weren’t going to be jettisoning the capsule — but also that was a lot of additional mass to simply have to handle in the ground integration.”
Setting aside crew safety, since EM-1 is an uncrewed launch and mission, flying Orion inside a standard payload fairing might have released those ten extra metric tons of launch mass. “[The goal] would have been keeping them within the static envelope that’s allowable either by the SpaceX five-meter fairing that flies on Falcon or the five-meter ULA fairing,” Wood said.
“They have specific static envelopes that are allowable that constrain you both in diameter as well as axial station and so that would have been the limiting factor and it would not have fit.”
As they dug deeper into the problem, consulting with Orion’s prime contractor Lockheed Martin, they came full circle. “When we looked at their system-level impact they needed the LAS to get the ogive fairing off of the command module (Orion crew module), they couldn’t just fly the command module without some kind of fairing,” Wood explained.
“We weren’t going to be able to fit the command module and that stack inside of a conventional payload fairing that we would have to bring to bear on either Falcon Heavy or the Delta 4 Heavy, so we said really we need to leave the LAS in place and we need the LAS to get the ogive fairing off. We can jettison it earlier in the flight than it would be for a crewed mission, but we pretty much have to leave it on there.”
“And then the aerodynamicists came back; our aerodynamicists did a preliminary look at what buffeting considerations we would have to look at,” he continued. “For example EFT-1 (Exploration Flight Test-1) flew with the Orion outer mold line integrated into a five-meter core on a Delta 4 Heavy, but on a Falcon Heavy that’s a less than four meter diameter core and so you’re talking about having a hammerhead configuration aerodynamically and we would have to look at that as to whether or not we were going to be inducing aerodynamic buffet considerations.”
“So from an aerodynamic standpoint it also made the most sense to leave the LAS in place and that hurt because I really wanted to get rid of that thing, but it made sense,” Wood continued.
“From the standpoint of initial consideration going in I think the spacecraft customer would have wanted us to leave it in as a ground rule. In challenging that ground rule and challenging what we could do with it and what benefit we could take from it we worked our way around back to say, you know, it’s not really worth chasing this, we’re not going to get enough benefit out of the deal.”
Orion mass reductions and docking additions
In-space mass was also going to be an issue, and the Orion crew module was going to need to be stripped of any non-essential items for performance reasons. “We stressed the Lockheed Martin and the Orion folks quite a bit, and I say that positively but we definitely pushed them outside their comfort zone with our requests to investigate what they might do to shed mass on the command module and on their stack,” Wood said.
“Of course realize, most of the EM-1 spacecraft stack is built and the command module is closed out. So we can blindly talk about removing mass simulators and say ‘hey that would save us over a thousand pounds of dead weight that we don’t have to push into trans-lunar injection any more.’ And they said ‘yeah, but we’re the ones that have to do it, our command module is buttoned up.'”
“These things are not sitting out there saying ‘hey take me I’m a mass simulator and unload me off of the capsule,'” he continued. “That was going to take quite a bit of work on their part.”
“They did work it out how they would approach the problem and do it and then we would also work with them on ideas of different fuel, partial fuel loading options on the European Service Module and tried to explore every bit of the trade space that they had available to them from the Europeans and from their own requirements for being able to vary the amount of propellant that was loaded on there.”
The public debut of the feasibility study was accompanied by the suggestion of doing a dual-launch, Earth Orbit Rendezvous style mission, so rendezvous and docking options were another avenue studied at the outset.
“Before the performance answers would even start to favor or not favor a rendezvous solution one of the things we needed to establish, and this was working with the JSC Orion project office and Lockheed Martin the prime contractor, was on the Orion side whether or not they would even have a capability for a rendezvous and docking of another vehicle, should another vehicle become available or be created to apply the delta-V to the stack to finish getting it out to the trans-lunar injection,” Wood explained.
“The EM-1 mission configuration does not have a docking collar, nor the software and avionics to accomplish a rendezvous on its own. So one of the things that we did early on was investigate with Orion and Lockheed Martin the feasibility of being able to integrate a docking collar and associated hardware into the command module on EM-1 such that we could accomplish a rendezvous with their spacecraft in what was called a passive-passive mode.”
“And that is to say not try to accelerate the docking capability but rather allow the capsule to just be a passive target and let someone else like a Dragon based vehicle accomplish the rendezvous as the active participant with the active docking collar, something like what was accomplished when the Dragon DM-1 mission flew to the Space Station and it accomplished an automated docking there,” Wood continued.
“That was an area where Lockheed Martin and JSC Orion put in some serious effort to be able to characterize, identify the hardware, the schedules, the timelines that would be necessary in order to put a docking collar onto the EM-1 Orion and be able to facilitate that kind of in orbit rendezvous.”
“In parallel we worked with SpaceX, because of course they’re the only ones with a flight-demonstrated autonomous rendezvous capability and so I spent some time with their Dragon GN&C (Guidance Navigation and Control) folks out in Hawthorne, we spent some good bit of time on the phone discussing the specifics of what that system needed, what its capabilities were for rendezvousing with a passive target with just optical targets and laser reflectors on it.”
“That was one of the crucial enabling technical elements to say ‘is rendezvous even in the picture?’ Now ultimately from a performance standpoint, there was no rendezvous option that bore any fruit that we could realize in the short design and integration timeline that we had available and the reason for that is just that even if I had an Orion stack in orbit that had a docking collar on it that could accept a docking from an active participant, shifting that amount of mass out into trans-lunar injection from low Earth orbit was just such a Herculean task there’s nothing on the shelf today that would accomplish that.”
“Essentially, a new stage would have to be designed around Dragon’s rendezvous/docking and propulsion elements,” they added in a follow-up email. “Certainly keeping the Falcon second stage attached to Dragon would have been an option to meet performance requirements, but as indicated during our initial interview, the thrust generated by the SpaceX Mvac engine produces loads that are not acceptable to this payload, so this option was quickly ruled out.”
Horizontal integration
Another area that was tackled at the beginning was integrating Orion with the SpaceX Falcon Heavy launch vehicle — Orion was designed for vertical integration, Falcon for horizontal integration. “That was one of the things that we attacked right away, knowing that Falcon Heavy was a candidate and there was a potential that the horizontal integration could render that option infeasible right off the bat,” Wood explained.
“So that was when we worked directly with the Lockheed Martin spacecraft team who, as it happens is down here in the same building that we are, and so I kind of short-circuited the process just a bit and worked with a couple of their senior engineers. In the course of two or three days we worked through the problems and the challenges that would be associated with integrating the spacecraft in the horizontal.”
“When the spacecraft goes up to Plum Brook for their thermal vacuum testing, they’ll fly in the Super Guppy and they will fly in an unfueled, but horizontal configuration,” Wood continued.
“Now they won’t have the LAS on there, but the spacecraft can take some degree of horizontal handling and transport loads, but there’s quite a bit of propellant for a spacecraft in a launch configuration and of course you’ve got the heavy LAS that would be attached to the nose of the command module structurally and would have to be factored into whether or not you could accomplish a horizontal to vertical transition on the Transporter Erector necessary to launch a Falcon Heavy in the configuration that they have today.”
“We only made it far enough before the end of the study to be able to say that the team working the problem had found no obvious showstoppers, but that there was going to be a considerable amount of work that still had to be completed. And a lot of that would have involved coordination with the Europeans, because now we would be handling their Service Module in a fueled condition that’s not consistent with the vertical integration and vertical handling that they had planned for all along for their nominal processing here at Kennedy.”
“Again the enemy here is time, so if you’re going to do a short timeline for integration, currently they have no vertical integration capability at Complex 39 for a Falcon 9 single stick or a Falcon Heavy,” Wood added. “The National Reconnaissance Office and the U.S. Air Force have asked them to look at a vertical integration capability and so some design work has been done in that direction, but nothing would be ready in time to support integration and processing in mid-2020.”
“Really the best option would have been to work through the problems and make the horizontal integration and normal Falcon Heavy style of erection, to make that work. That would have been the least risk option.”
The spacecraft will also need some set of ground services, but that was also not considered to be a showstopper. “We had expected that we would be required to accommodate a ground umbilical servicing, which would be [a] normal part of our mission design for any of our spacecraft customers, so that level of mission integration design work was something that we didn’t have time to go into and we had judged that that was not going to be a discriminator on whether we had a feasible solution to fly them on a commercial vehicle.”
Performance and mass considerations
Ultimately, the options that are available today were going to need performance augmentation. “We called ‘victory’ a lunar free return flyby, without any hope of getting into a lunar orbit,” Wood said.
“Obviously we would have loved to have satisfied all of their preferences but we decided that victory would be if we could show feasibility and that’s getting within what I’ll call spitting distance with the preliminary design that we were doing and making use of all of the propellant in the Service Module that they [Orion] would let us take advantage of. And we worked closely on this on how much delta-V we could count on the spacecraft providing on their own.”
“That ‘within spitting distance’ that James is referring to, when we were getting within a thousand meters per second of the TLI end state we were generally getting to be pretty happy,” Carney added.
“What that meant was that the Service Module was required to augment that TLI burn by a thousand meters per second, that’s a fair amount of delta-V that they were eating into for their mission profile and that was what was keeping them from meeting all of their objectives, so we were never able to find that closed solution. ‘Close’ defined in this case getting to TLI and not requiring some help from the spacecraft.”
A free-return mission was still feasible and on the surface would have satisfied one of the primary flight objectives, which was to test the spacecraft on a lunar return velocity re-entry. Orion’s heatshield was redesigned between the EFT-1 mission and now, and NASA wants to test it before committing to flying a reentry from the Moon with crew.
“I had messed with them on that part because in order to accomplish that lunar free return we needed them to get rid of all of their mass simulators in the command module,” Wood noted. “It messed with their balance and trim for executing that entry, so while we could achieve the entry velocity numbers it was going to be very difficult for them to achieve the trim conditions that they were targeting.”
“So meeting the entry heatshield flight test objective was only a maybe at that point and required more assessment, but that was definitely far from their only flight test objective,” he added.
“That was one of their prime objectives and we did talk with them about that,” Carney said. “Initially that was really kind of what they first came to us with and then as we continued to work the problem more and more their desire to meet the full suite of objectives that James and I are talking about that I think became more solidified, more what they really wanted to see out of this.”
Orion’s total delta-V capability is quoted to be about 1340 meters per second; within the Exploration System Development (ESD) division’s requirements, taking into account “all translational and rotational maneuvers under dispersed conditions” and Flight Performance Reserve drops the usable amount down to around 1250 meters per second.
However, those are numbers to meet the requirements for a fully-loaded Orion configuration with crew and supplies for a twenty one-day mission on its own.
The mass simulators inside Orion’s crew module for EM-1 help give the capsule the weight and center of gravity (CG) that will be seen on crewed missions beginning with Orion’s next flight. The flight control system nominally performs a skip entry to reach the designated landing zone.
Removing the mass simulators may create an unrealistic test configuration on EM-1 for the flight control system, but it is uncrewed and eliminating the simulated mass of environmental control and life support systems (ECLSS) from the Crew Module would increase the Service Module’s overall performance and give mission planning more flexibility in terms of meeting the shortfall from any of the commercial launcher options.
“We were generally looking at 1 to 1.5 km/sec delta V augmentation from the SM (Service Module) for potential scenarios,” they said. “Those options were definitely in the trade space; however, they obviously impacted the EM-1 mission test objectives since we used SM propellant for a portion of the TLI burn that was originally planned for other burns near the moon.”
“[Initially] we were going ‘ok, so if the whole thing is just about getting the speed up for testing out the heatshield on entry, well that simplifies the problem,'” Wood explained. “And the answer in working with the spacecraft project was ‘no,’ there was a much more detailed list of flight test objectives that they wanted to wring out their ability to navigate around the Moon, to conduct those long-duration ops with the service module and the command module and the long burns and delta-V applications that they would want to make before they put the crew in that position.”
“I think that was a measure of we were having some success, we were actually getting a better answer than what were expected to find and so they started taking us more seriously along the way and saying ‘OK, let’s see how much actually can we get done here’ and it ended up being a very good collaboration investigating how many of those, that total set of flight test objectives that could be met,” Wood added. “Now again, couldn’t meet all of them, and they had a solution that would, so they chose that path.”
“But it was surprising how successful, what a percentage — and I can’t give you a number on that — but it was a greater percentage than expected of flight test objectives that we would have been able to help them meet.”
Future options
The most promising launcher in the study was a fully-expended SpaceX Falcon Heavy, which was the highest performance option for this TLI-trajectory study.
“We examined a number of options involving various reusable and expendable core and booster combinations,” they noted. “Ultimately, the only potentially feasible options required fully expendable boosters and core for the Falcon Heavy.”
“The magic number that we were shooting for was 3000 meters per second out of approximately a hundred eighty-five kilometer park orbit,” Carney said. “And like I said we were getting two-thirds of the way there in some cases.”
“Just using a Falcon Heavy alone and surgery, major surgery on the Orion,” Wood added, with Carney also adding, “and maybe a little bit of surgery on the Falcon.”
Although launching an Orion in less than fifteen months from now on a commercial launch service might not have the necessary technological readiness level, there were some interesting combinations of off-the-shelf capabilities if one could relax the time constraint. “The interesting thing was the LOX (liquid oxygen)-hydrogen ICPS (Interim Cryogenic Propulsion Stage), derived from the Delta Cryogenic Second Stage,” Wood said.
“The concept of putting a high-energy, LOX-hydrogen stage on top of a Falcon Heavy stack underneath the spacecraft stack, that would be something that if we’d had more time, if we had more time out in the mid-2020s time frame or something like that, that would be something that would bear additional investigation.”
“It never closed the case with the assumptions we had to make in terms of analysis, but it had some interesting possibilities that were worth checking out in the future,” he added. “Performance aside, trying to integrate a large, LOX-hydrogen fueled stage onto the Falcon Heavy stack, plus the heavy Orion integrated stack, plus the LAS on top of that stack, we were reaching a point where if I had five years to plan and execute something like that we might be able to take that on.”
“From a performance standpoint, we were getting very close, we were getting under that 1000 meter per second augmentation help that we needed,” Carney added. “We were still showing we needed a little bit of help, but not quite as much and as you say James with some time and some additional study we might have been able to close that case. On the surface we weren’t able to do it though.”
“The other competing factor and also in fairness that we need to note is that we were looking at the EM-1 configuration,” Wood added. “EM-2 (Exploration Mission-2) was only going to get heavier and that was something that we had not considered in our performance trades — we were not hunting EM-2, if you will, but we know that’s only going to get heavier, it’s not going to get lighter.”
Still, the Administration is not closing the door on looking at alternate launch options for Orion, especially in light of the subsequently announced goal to land Americans on the Moon within the next five years.
“There is a solution here that could potentially work for the future,” Administrator Bridenstine said in a NASA agency-wide town hall meeting on April 1. “It would require time, it would require cost, and there is risk involved but guess what? If we’re going to land boots on the Moon in 2024, we have time and we have the ability to accept some risk, make some modifications, all of that is on the table.”
“There is nothing sacred here that is off the table and that is a potential capability that could help us land boots on the Moon in 2024.”
Quelle: NS
----
Update: 25.04.2019
.
DoD practices Starliner at sea recovery for first time
In a critical first for Boeing’s CST-100 Starliner capsule, the crew transportation vehicle is putting DoD and Air Force rescue teams through their paces as they seek to understand and refine what will be needed to rescue a Starliner crew from the capsule should an off-nominal landing in the water occur.
Starliner at sea rescue practice/process:
The test is a critical part of Starliner’s certification to carry astronauts to and from the International Space Station.
SpaceX’s Dragon capsule went through similar tests last year, and NASA has conducted similar exercises with its Orion spacecraft.
Starliner itself will nominally land on land in the American southwest, but in-flight aborts/off-nominal emergency returns from orbit will/could result in Starliner splashing down in the ocean.
Despite the planned difference in an off-nominal vs. nominal landing of Starliner, the equipment sea rescue personnel would use for Starliner is the same as it is for Dragon and Orion.
After Starliner splashes down in the ocean and members of the 304th Rescue Squadron reach the spacecraft, the first thing the team will assess is the orientation of the craft.
If Starliner has landed upside down or tipped upside down after landing, the first and foremost action will be the right the spacecraft.
This process was not described in detail, but Air Force Major Marcus Maris, DoD (Department of Defense) Human Space Flight Support Office Rescue Division Chief, and Captain Paul Fry, 304th RQS Assistant Director of Operations, iterated that the team – while novices for such a practice on Starliner – have practiced the basics of the procedure on both Orion and Dragon.
Moreover, part of today’s test – this afternoon – will be purposefully capsizing the Starliner mockup so teams can practice the righting process.
Once the capsule is righted, or if it lands in the correct upright orientation, the next order of business would be for rescue teams to gauge the stability of the craft in the given sea states (wave heights, winds, etc.).
If warranted, the rescue team will deploy a stabilization collar around the base of Starliner to help control the craft during rescue operations.
The collar would be deployed by divers, wrapped around the base of Starliner, the orange cords/lines on the collar attached to the spaceship, and the collar then inflated using scuba tanks.
The rescue divers/team would use the same stabilization collard for Starliner as they will for Dragon.
The collars have differently colored cords/lines, with orange being used for Starliner and blue being used for SpaceX.
This was built into the design so that the rescue equipment is as standardized as possible between the three U.S. crew spacecraft.
Only Orion has a different stabilization collar simply because of how much larger its base is then Dragon’s and Starliner’s.
After the stabilization collar is attached, rescue teams will deploy and inflate the “Front Porch”, a specially-built life raft that will deploy in front of Starliner’s side hatch.
The Front Porch has enough room and can carry enough supplies (food, water, medical) to support 4 Starliner crewmembers and the 9-person rescue dive team for up to 72 hours.
Like the stabilization collar, the Front Porch for Starliner is the same as the one that would be used for Dragon and Orion off-nominal water landing rescues.
Once the Front Porch is deployed, crews will then open Starliner’s side hatch and begin assessing and extracting the crew.
If for some reason the side hatch cannot be physically opened or cannot be safely opened to due water intrusion concerns from high seas, rescue teams can open the top hatch to reach and extract the crew.
The crew would then take refuge in the Front Porch life raft with the 9-member dive team to await evacuation back to a ship or land.
The first part of the test today went well and was conducted inside the middle basin at Port Canaveral on the Air Force-controlled side of the port.
Based on lessons learned from today’s first test, Major Marcus Maris and Captain Paul Fry hope to proceed to open ocean tests by the end of this week.
Those open ocean tests will occur roughly 10 miles off shore of Cape Canaveral.
NASA at sea rescue requirements for Starliner, Dragon, and Orion:
While today’s test was the first in-water practice run for Starliner at sea rescue, it represents a much larger DoD commitment to space crew rescue operations – universal procedures that would be followed for Starliner, Dragon, and Orion.
During ascent for Starliner, Dragon, and Orion, the 304th Rescue Squadron will have two teams stationed along the east coast of the United States, one at Patrick Air Force Base (just South of the Cape) and the other in Charleston, South Carolina.
The Patrick team, Rescue 1, will be responsible for on-pad aborts that place a capsule in the water or for aborts in the first couple minutes of flight that place the capsule within a 200 nautical mile zone from the Cape.
After that distance is exceeded, the Charleston crew (Rescue 2) would be responsible for rescue of a launch-aborting crew vehicle anywhere else across the Atlantic.
The third team, stationed in Hawai’i, (also part of Rescue 2) would be responsible for any after-launch immediate landing need or off-nominal Station return contingency that places a Starliner or Dragon in the Pacific.
If an off-nominal from orbit return occurred with splashdown in the Atlantic, an emergency ocean return within 200 nautical miles of Cape Canaveral would fall to Rescue 1.
Any other Atlantic splashdown would fall to Rescue 2 from Charleston because they have more powerful aircraft that could reach Starliner or Dragon or Orion quicker than the Patrick support craft.
Rescue 1 carries a requirement to have a crew en route back to land within 6 hours of splashdown.
Rescue 2 carries a requirement to have the hatch on a capsule opened within 24 hours of splashdown and a crew evacuated (via helicopter or ship) from the sea landing area within 72 hours of hatch open.
These sea rescue operations are led by the 45th Ops Group Detachment 3 – Human Spaceflight Support Office – at Cape Canaveral, in coordination with NASA.
The main diving rescue force is the 304th Rescue Squadron based in Portland, Oregon – which is part of the 920th Rescue Wing based at Patrick Air Force Base, FL.
Quelle: NASASpaceflight.com
+++
Crews use Boeing training capsule to practice search, rescue at sea for 1st time
BREVARD COUNTY, Fla. - Days after a SpaceX mishap sent smoke up into the air along Florida's Space Coast, another commercial partner of NASA was working on plans to launch astronauts from U.S. soil again.
Boeing is still months away from its first uncrewed test flight to the International Space Station, but astronaut rescue training is underway should the need ever arise.
Channel 9's Melonie Holt was at Cape Canaveral Air Force Station's Army Wharf on Tuesday to watch U.S. Air Force pararescue teams practiced reaching a capsule, stabilizing it and removing its crew members.
The rescue teams used a training capsule of the Boeing CST-100 Starliner, which the company is developing to ferry astronauts to the ISS as part of NASA's commercial crew program.
The agency's other partner, SpaceX, will fly its own capsule, the Crew Dragon, atop a Falcon 9 Block 5 rocket.
SpaceX successfully completed an unmanned test flight to the ISS before that vehicle suffered a setback and experienced an "anomaly" during a static test fire Saturday that could delay the company's first manned test flight.
Boeing is targeting August for its first uncrewed flight aboard a ULA Atlas V.
Unlike the Crew Dragon, which was designed to splashdown, the Starliner will return to Earth on land in a 15-square-mile safe zone, unless a situation necessitates a water landing.
"It's very significant, very important that the crew knows that there's a rescue capability and a force that's been trained and prepared," said U.S. Air Force Maj. Marcus Maris.
The U.S. Department of Defense's Human Space Flight Support Office Rescue Division has supported all NASA human spaceflight programs and will now be on standby for both the commercial crew program and NASA's Orion deep space exploration program.
"Our part is the easy part compared to everything else that's going on," said U.S. Air Force Capt. Paul Fry, the 304th Rescue Squadron assistant director of operations. "We'll definitely be ready."
The training will continue Wednesday when rescue crews move from the basin to the ocean.
Quelle: WDTV9
----
Update: 26.04.2019
.
NASA urged to retain key SLS test
WASHINGTON — As NASA studies ways to accelerate development of the Space Launch System, an independent safety panel called on the agency to retain a major upcoming test of the vehicle.
NASA had been contemplating eliminating the so-called “green run” of the SLS core stage as a way to cut several months of schedule. In that test, the completed core stage would be brought to the Stennis Space Center and placed on a test stand, where its four RS-25 engines would be fired for eight minutes, simulating the actual flight of the vehicle.
In testimony before a House appropriations subcommittee in March, NASA Administrator Jim Bridenstine said the agency was studying doing away with the green run test. Instead, NASA would ship the completed core stage directly to the Kennedy Space Center, where its engines would be briefly fired on the pad at Launch Complex 39B.
Bridenstine suggested in his testimony that alternative testing of the RS-25 engines could eliminate the need for the green run. “Could we test each engine individually at very high off-nominal kinds of conditions to get certainty, or at least eliminate as much risk, or almost as much risk, as we would if we ran the green run?” he said. Doing so, he said then, could cut six months from the vehicle’s development schedule as NASA sought ways to keep the first SLS launch scheduled for 2020.
However, at an April 25 meeting of the Aerospace Safety Advisory Panel (ASAP) at the Marshall Space Flight Center, members recommended that NASA carry out the green run test as one of several milestones to ensure the vehicle is safe to carry crewed spacecraft.
“There is no other test approach that will gather the critical full-scale integrated propulsion system operational data required to ensure safe operations,” Patricia Sanders, chair of the panel, said of the green run test. “Shorter-duration engine firings at the launch pad will not achieve an understanding of the operational margins, and could result in severe consequences.”
“I cannot emphasize more strongly that we advise NASA to retain this test,” she added.
NASA has not provided an update on efforts to accelerate SLS development since Bridenstine, speaking at the National Space Council meeting March 26 in Huntsville, Alabama, concluded that it was not feasible to shift Exploration Mission (EM) 1 from the SLS to commercial vehicles. However, there is growing belief in the space industry that NASA will keep the green run test even if it jeopardizes the ability to launch the SLS in 2020.
Sanders said at the meeting that the committee was aware NASA was trying to launch EM-1 as soon as possible, and that effort could find ways to streamline the process. “But as NASA evaluates different paths to potentially accelerate the EM-1 flight, it cannot lose sight that the ultimate objective of that flight is to mitigate risk and provide a clear understanding of the risk posture prior to the first crew flight,” she said.
She noted there are two approaches NASA can take to test flights like EM-1: either waiting to launch until all flight components have been qualified, or launching earlier and incorporating data into the qualification process. Each approach as its own strengths and weaknesses, she said. “Determining the proper timing of an integrated flight test requires a deliberate, detailed and important dialogue on the risk tradeoffs for the overall program,” he said.
Aging spacesuits
In a separate discussion at the meeting, panel members raised concerns about aging extravehicular mobility units (EMUs): spacesuits worn by astronauts who perform spacewalks, or extravehicular activities (EVAs), outside the International Space Station. Those units are decades old and, the panel believes, represent a growing safety risk.
“The EMUs used for ISS are now about 40 years old and aging out,” said Susan Helms, a panel member and former astronaut. NASA seeks to extend the life of those suits to 2028, but she argued that is insufficient.
“The view of this panel is that, in spite of their heroic efforts, the current suit is now outside its design life and we are growing increasingly concerned about the risk posture that NASA has adopted with the current suit,” she said. “We recommend that NASA begin an immediate transition to a next-generation EVA suit system before the risk becomes unmanageable.”
Another committee member and former astronaut, Sandra Magnus, agreed, saying that NASA is too focused on the day-to-day issues of maintaining the current spacesuits to see the overall issue with the risk the suits pose. “I would like to invite the NASA management to really take themselves out of the system for a moment and look at this particular issue objectively, because it’s really important,” she said.
“We have reached a point with the EMUs where it’s time to retire the current suit and move on to a next-generation suit,” Helms said.
Quelle: SN
----
Update: 27.04.2019
.
More delays for NASA's test of Orion spacecraft's emergency system
NASA recently asked boat retailer MarineMax Houston to shrink wrap an Orion crew module test article so it could be shipped from Texas to the Plum Brook Station testing facility at NASA's Glenn Research Center in Ohio.
A test of the emergency system on the spacecraft being built to take humans back to the moon has been delayed again -- this time to allow for more testing at Cape Canaveral, Fla.
The Orion spacecraft program announced Thursday on Twitter that the test would not be conducted until July 2. Most recently, it was scheduled for early June.
"This date provides additional time for work on the launch abort system and takes into account Eastern Range availability," the tweet stated.
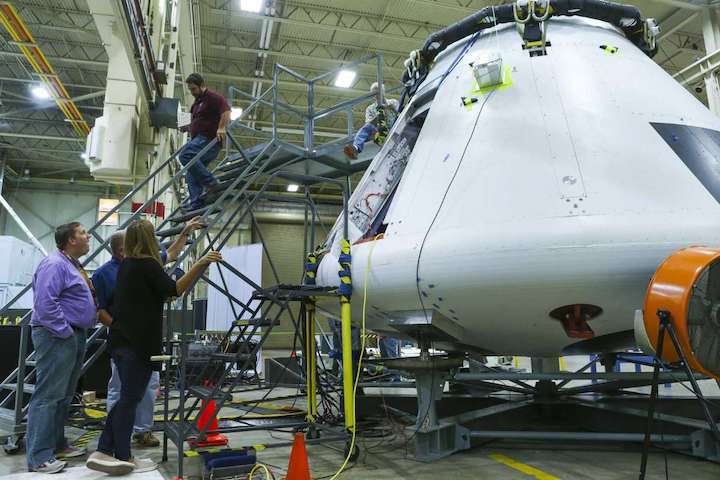
This is the second major delay for the test, known as Ascent Abort-2, since late last year. The test suffered a two-month delay because of the federal government shutdown that began Dec. 22 stemming from a political battle over a border wall between the U.S. and Mexico.
Work on Orion's primary safety feature, known as the launch abort system, largely has been conducted at Johnson Space Center in Houston. It has been the subject of year-long Houston Chronicle series called Chasing Orion.
The launch abort system will allow the spacecraft's eventual four-person crew to escape if the rocket explodes. Its importance was demonstrated worldwide in October, when the Russian Soyuz spacecraft transporting an American astronaut to the International Space Station had to abort its launch after a rocket booster failed, forcing an emergency landing.
Such an event had not happened for Russia in 30 years. And even though it was a success -- both NASA astronaut Nick Hague and Russian cosmonaut Alexey Ovchinin were safe -- it served as a reminder of why such a system is so important.
The Orion spacecraft has been in various stages of design for nearly two decades, its destination shifting between the moon and Mars depending on White House leadership. But a return to the moon is a top priority for President Donald Trump's administration.
NASA had planned to launch an Orion capsule without humans onboard around the moon next year, but problems with the Space Launch System rocket that is supposed to push it out of Earth's atmosphere may jeopardize that schedule.
The simplified module will not be reused once the test is complete. Additional capsules for the unmanned and crewed missions are under construction. The Space Launch System that will send Orion to space — the most powerful rocket NASA has ever built — and the ground systems for launch are being developed simultaneously.
Johnson personnel also are designing Orion's cockpit and flight software, spacesuits and parachutes. Johnson is home to the nation's astronaut corps, where human space flight research and training take place. It is also home to the International Space Station's mission operations and the Orion program.
From start to finish, the abort system test is expected to account for only $256 million of the program's more than $11 billion budget.
Quelle: Houston Chronicle
----
Update: 29.04.2019
.
How to rescue Dragon, Starliner, and Orion crews at sea
n preparation for the return of crew launches from the United States, the Department of Defense, in coordination with the U.S. Air Force and rescue dive teams, have outlined how they would rescue the crews of a Dragon, Starliner, and/or Orion spacecraft should they abort into the sea or perform an off-nominal ocean landing.
The procedures are only in regard to rescuing a crew, with the recovery of the individual capsules being left to the respective agencies.
Generic procedures:
The outline of this plan came earlier this week while crews performed the first open water test of rescue operations for Boeing’s Starliner capsule in the middle basin of Port Canaveral, Florida.
That test was specifically to determine how the various rescue equipment would be connected to the Starliner and how the overall generic rescue procedures need to be modified or tweaked for Starliner as compared to Dragon and Orion.
Starliner was the third of the new vehicles to undergo such testing, which was carried out this week ahead of Starliner’s anticipated flights later this year on an uncrewed Orbital Flight Test and a Crew Flight Test.
Per the generic rescue plan across all three U.S. crew vehicles, the practice and trainings – like the one this week – are meant to familiarize the Air Force and DoD rescue divers with how to “stabilize the capsule, get astronauts out, and then perform immediate care and treatment until [they can get] to a higher level of care.” said Captain Paul Fry, 304th RQS Assistant Director of Operations based in Portland, Oregon.
The rescue procedures were developed between NASA and the DoD, with capsule-specific input from SpaceX for Dragon, Boeing for Starliner, and NASA for Orion.
While minor elements will need to be tweaked here and there for each capsule, the overall procedures are the same, as is the equipment that will be used.
As previously reported, the stabilization collar for Starliner and Dragon will be the same, with different colored cords noting which hookups go to which vehicle; however, the stabilization collar for Orion has to be different due to the larger size of Orion’s base compared to the commercial capsules.
The front porch, conversely, will be the same for all vehicles.
The main difference, though, with the generic rescue plan has to do with Starliner – which is the only one of the vehicles with nominal land landings at the end of its mission.
Because of this, Starliner’s hatch will ride lower to the waterline compared to Dragon and Orion. Thus, rescue of a Starliner crew will first and foremost involve assessing how the capsule is riding in the water and attaching lifting bags or airbags to the craft to help raise it higher in the water.
This would particularly be needed for inclement weather conditions during a potential Starliner crew rescue, as opening the hatch while the capsule is in its natural height above the waterline could permit water intrusion into the capsule – which needs to be avoided whenever possible.
Attaching these lifting bags and raising the Starliner further out of the water than how it naturally lands will, however, not always be a necessity. Should the capsule land in very calm conditions, it might not be necessary to raise the capsule higher in the water before opening the side hatch.
Day of launch process:
For launch abort and rescue operations, the 304th RQS will have three teams stationed around the world, a six-person team at Patrick Air Force Base, FL, just south of Cape Canaveral; a nine-person team in Charleston, South Carolina; and a nine-person team in Hawai’i.
The Patrick Air Force Base team will be tasked with abort rescues that occur within 200 nautical miles of Cape Canaveral – be it a pad abort or an In-Flight Abort in the first couple minutes of flight.
Under this scenario, the Patrick Air Force Base six-person team will have to reach the capsule, get the crew out, and have started back to land within 6 hours of the abort.
“For launch, we’ll be stationed and all our equipment will be on the aircraft and ready to go. We’re going to be in a 15-minute alert, sitting there ready to take off,” said Captain Fry.
“We’ll take off, and then as far as our actual deployment, once we get over sea and we can confirm that we’re actually looking at the capsule, then we’ll start throwing all our boats out and jump to it.”
The Patrick Air Force Base team will use either an HH-60 helicopter or a C-130 aircraft for their deployment to the rescue zone.
But for an aborting capsule that lands outside of the 200 nautical mile zone around Cape Canaveral, the Charleston, South Carolina, deployment would then be the primary response team.
The Charleston team will use a C-17 aircraft, faster and larger than the C-130, enabling them to reach downrange aborting capsules faster than the Cape Canaveral team once the 200 nm line is crossed.
The Hawai’i team will also use a C-17.
The Charleston team would be responsible for reaching a spacecraft anywhere beyond the 200 nautical mile limit of Cape Canaveral Air Force Station all the way across the Atlantic on a northeasterly Space Station launch trajectory to just off the coast of Ireland.
For Orion missions launching on much more easterly trajectories for lunar missions, the same 200 nautical mile rescue line would be observed, but it is important to note that the 200 nautical mile line is not a hard and fast limit.
Should a capsule abort and actually land 202 or 210 nautical miles downrange in the Atlantic, the Patrick team might still be the ones to deploy as opposed to the Charleston team based on day-of assessments of how quickly a team could reach the capsule.
Based on where Starliner, Dragon, and Orion will enter their preliminary orbits, the next likely emergency landing location should an emergency occur in the first few moments after orbit insertion would be in the Pacific Ocean, at which point the Hawai’i team would be the responsible unit for rescue and recovery of a crew.
For the Charleston and Hawai’i teams, their rescue plan calls for them to be on site with the hatch to the capsule opened within 24 hours of splashdown.
“The 24-hour requirement is that these guys need to be there … and open the hatch within 24 hours,” related Brent Maney, Space Medical Contingency Specialist for the Human Space Flight Support Medical/Rescue Division of the Department of Defense stationed with the 45th Operations Group, Detachment 3.
“The rationale for having the hatch open within 24 hours is because of the way the life support is set up. If the crew has to stay in the vehicle and can’t get themselves out before [the rescue guys] get there, they only have a life cycle of about 24 hours.”
For the Hawai’i rescue team, analysis shows that they could take anywhere between 4 to 12 hours to reach a capsule splashing down in the Pacific.
Right now, the Indian Ocean is not planned as an emergency landing location, but should that need to happen, the Hawai’i team would be the responsible rescue party.
Moreover, Captain Fry related that it is actually more efficient for the rescue teams to be stationed on land than it would be for them to be pre-positioned at certain locations in the ocean.
“We would not be quicker out in the ocean because the capsule could land anywhere. So if we’re in the ocean, it would take us significantly longer [to reach the capsule] than flying there,” related Captain Fry.
“You can only go maybe 20 knots with big ships, and we don’t own any of those. But the aircraft that we’re flying can go 300 to 400 miles per hour and just fly right to the capsule.”
Regardless of what team is deployed, the worst case scenario is if a capsule lands and flips upside down in the water, known as the Stable II configuration.
Stable I is when the capsule splashes down and remains upright.
Stable II happened twice during the Apollo program, after the Apollo 7 and Apollo Skylab 4 capsules splashed down and flipped upside down in the ocean.
The Apollo Skylab 4 capsule upside down in Stable II configuration in the water following splashdown. (Credit: NASA)
The extra stress this puts on the crew is one of the first and foremost reasons to quickly right the capsule.
For the 304th rescue divers, the same lift bags they would use to raise a Starliner capsule farther out of the water to prevent water intrusion into its side hatch are the same devices they would use to right an Orion, Dragon, or Starliner capsule.
After this, the stabilization collar would be attached to the bottom of a capsule and then the front porch deployed in front of the side hatch.
The front porch is a specially built life raft for the new U.S. crew vehicle emergency rescue operations; it can support a 9-person team with a 4-person crew for up to 72 hours as they await a rescue ship or rescue helicopter for transport back to land.
It can also serve as a medical triage facility for any injured crewmember.
More so, an interesting element to these at sea rescues is the role weather could play.
For on-pad aborts or aborts shortly after liftoff, odds are the weather would be perfectly acceptable or at sea rescues or at least would clear quickly enough to meet the safety standards set by NASA, the DoD, and the various crew capsule programs.
But farther down range aborts along the ground track could result in a capsule splashing down in the middle of weather systems over the Atlantic.
In this particular case, pre-launch day-of considerations would have to be made by the Department of Defense and NASA as to what risk they are willing to accept should a crew capsule splashdown in one of these inclement weather areas during an abort.
These considerations range from a delay to launch to a delay to rescue for the safety of the rescue teams to sending the rescue teams out in potentially hazardous weather conditions.
The 304th rescue squadron itself also has the ability to make a call on weather conditions they believe are too dangerous for their teams to operate in.
“I’ve been in 15-20 foot seas doing training missions,” said Captain Fry. “But there are some weather constraints. For our parachute systems, we can’t parachute through lightning, and if it’s pouring down rain that would also affect our parachutes.
“Sea states [are also a concern]. If [they] get real big, we have to start weighing that risk and reward of ‘are we going to be able to survive going into that situation.’”
Brent Maney added, “There’s a whole risk mitigation process, and NASA and the DoD accept that risk. So one of the things our team goes through is that the day of launch, day of landing, there’s an entire process of looking at the global weather along the landing track and analyzing whether it’s worth the risk.
“If the north Atlantic has a really nasty storm but here it’s beautiful, the powers-that-be … might decide it’s worth the risk to go ahead and do the launch, accepting that it could land in the north Atlantic and accepting that these guys might make a call that it’s too rough.
“So it’s just a risk mitigation process. It’s all coordinated in advance.”
Regardless of the weather, the team did make clear that their only concern is the rescue of the crew, not the recovery of the capsule.
This means that if a Starliner, Dragon, or Orion vehicle lands hundreds or thousands of kilometers downrange from its launch site, the rescue team would leave it floating by itself once their mission of recovering the crew is complete.
Recovery of the capsule would then fall to NASA for Orion, SpaceX for Dragon, and Boeing for Starliner.
Quelle: NS