9.12.2018
ARIANE 6 ON THE WAY TO FLIGHT
This has been an intense year for Ariane 6 development, with progress boosted across Europe: plants are manufacturing new parts using novel methods, all engines have been tested, and the construction of launch facilities is well underway.
ESA has worked with an industrial network led by prime contractor ArianeGroup, of more than 600 companies in 13 European countries, including 350 small- and medium-sized enterprises, to fine-tune the design and start production. Meanwhile, France’s CNES space agency has been preparing its launch facilities at Europe’s Spaceport in French Guiana.
Details on all these activities were recently shared at the 69th International Astronautical Congress in Bremen, Germany – downloadable here (.pdf) – along with two papers submitted to the congress: launch system (.pdf) and launcher system (.pdf), here are the highlights.
Europe’s new Ariane 6 launcher covers a broad range of commercial and institutional applications while dramatically decreasing the cost of launches compared to Ariane 5.
Enabled by ESA’s Light satellite Low-cost Launch opportunity Initiative, a multiple launch service for small satellites starting mid-2021 will offer cost-effective launch opportunities for satellites of under 400 kg, via a rideshare approach on launchers such as Ariane 6, and its smaller cousin Vega-C.
The Ariane 6’s core stage is powered by Vulcain 2.1, an upgraded engine derived from Ariane 5’s Vulcain 2; its upper stage is powered by the reignitable Vinci engine. Two or four P120C solid-fuel boosters for Ariane 6, common with Vega-C, will be strapped on to provide thrust at liftoff.
The P120C and Vulcain 2.1 development models have started their ground testing, the Vinci is now qualified. This leads to the next significant milestone: the delivery of the Ariane 6 qualification model, to start combined tests in French Guiana at the end of 2019.
The second P120C model will be tested in French Guiana early next year, to verify its design and performance.
The Ariane 6 upper stage will be tested at the DLR German Aerospace Center newly developed P5.2 test facility in Lampoldshausen at the end of 2019.
Quelle: ESA
----
Update: 16.05.2019
.
Prototype Ariane 6 carbon-composite upper stage gets ESA funding
WASHINGTON — The European Space Agency gave contracts to ArianeGroup and MT Aerospace on May 14 to develop a prototype upper stage that could lead to an advanced carbon-composite upgrade for the Ariane 6 rocket.
ArianeGroup, the Franco-German company building Europe’s Ariane 6 rocket, and subcontractor MT Aerospace of Augsburg, Germany, received funding repurposed from a previously scuttled Ariane 6 project to instead develop the “Prototype of a Highly Optimized Black Upper Stage,” or PHOEBUS.
ESA member states decided last May to reallocate 70 million euros ($78.4 million at current exchange rates) to lightweight upper stage technologies and keep production of the P120C strap-on booster in Italy rather than spending it on creating a second production line in Germany. Those funds, provided by Germany, are being channeled into the two PHOEBUS contracts, as well as other programs, Jérôme Breteau, head of ESA’s Future Launchers Preparatory Program, told SpaceNews.
Breteau said by email that the majority of the PHOEBUS program is funded, with a small amount expected to come from ESA’s ministerial conference this November in Seville, Spain, where its 22 member states will decide on funding levels for current and future programs.
An upper stage built with carbon-composite materials instead of aluminum could lower the price of Ariane 6 launches while increasing the amount it can carry to geosynchronous orbit by up to two metric tons, according to ESA.
Guenther Hoerbst, a spokesperson for OHB, the parent company of MT Aerospace, said the company received 8.6 million euros from ESA for the PHOEBUS program. The company will focus on developing carbon-composite tanks and cryogenic structures.
ArianeGroup declined to state the value of its contract. ESA tasked ArianeGroup with working on “innovative stage architectures and system integration,” according to a company news release.
ArianeGroup and MT Aerospace said PHOEBUS prototype technologies will be integrated into a demonstrator in 2021 to test compatibility with liquid oxygen and hydrogen fuels.
The PHOEBUS prototype sets the stage for a future Ariane 6 upper stage called Icarus — the Innovative Carbon Ariane Upper Stage — that would be made of carbon-fiber reinforced plastic. ESA says Icarus could be ready for Ariane 6 by 2025 if fully funded. Ariane 6’s maiden flight is in mid-2020.
Breteau said the final funding level would also determine how much more performance the upgraded rocket stage can provide. Last year former ArianeGroup CEO Alain Charmeau said the target was to increase Ariane 6’s launch capability by one metric ton. ESA and industry’s new goal is around double that amount.
ESA said a decision on Icarus funding will be made at the ministerial conference.
Quelle: SN
----
Update: 2.10.2019
.
Ariane 6's core engine completes qualification tests
Ariane 6, Europe's next-generation launch vehicle, has passed another key development milestone. Its Vulcain 2.1 liquid-fuelled engine has now completed its qualification testing, which means combined tests can now begin.
The main stage Vulcain 2.1 engine will deliver 135 t of thrust to propel Ariane 6 in the first eight minutes of flight up to an altitude of 200 km.
A review last week marked the culmination of two Vulcain static firing test campaigns over 15 months on two demonstration models in test facilities at the DLR German Aerospace Center test facility in Lampoldshausen.
The final qualification static firing test of Vulcain 2.1 in July lasted almost 11 minutes (655 seconds). This completed a total of 13,798 seconds of operation, or nearly four hours with a controlled engine, using Ariane 6 flight actuators to gimbal the engine.
"These very positive results confirm the functional and mechanical behaviour of Vulcain 2.1. The upcoming combined tests will qualify Ariane 6 subsystems at stage and launcher level," commented Guy Pilchen, ESA's Ariane 6 launcher project manager.
The engine will be refurbished for dynamic and vibration tests. Combined tests using a fully representative main stage at Europe's Spaceport in French Guiana, will finally qualify the Ariane 6 core stage for flight.
Completion of the Vulcain 2.1 and Vinci qualification tests represent a major step forward in the Ariane 6 development.
The qualifying tests for the Vinci re-ignitable engine, which will power the launcher's upper stage, were completed in October 2018. Vinci will be integrated with the complete upper stage for tests at Lampoldshausen.
The next step for large propulsion systems is the static firing in French Guiana of the final qualification model of Ariane 6's P120C solid fuel booster. This test will define the acceleration profile for the launcher and will consequently allow engineers to pursue the preparation of the upcoming flights.
Final hot firing proves P120C booster for Ariane 6
The qualification model of the P120C motor configured for Ariane 6, has been static fired on the test stand at Europe’s Spaceport in French Guiana in a final test to prove its readiness for flight.
Advanced features make this new motor a pivotal achievement of European industry. It is an example of innovative thinking and optimisation that allows Europe to equip two very different launch vehicles with the same solid rocket motor.
Depending on the configuration, two or four P120C boosters will be strapped onto the sides of the future Ariane 6 heavy-lift rocket, the P120C will also serve as the first stage of the smaller Vega-C launch vehicle.
This huge P120C motor was filled with 142 tonnes of solid propellant inside its 13.5 m long and 3.4 m diameter casing and was moved from the integration building to the dedicated stand used for testing solid propulsion stages.
After ignition it burned for 130 seconds, delivering a maximum thrust of about 4500 kN simulating liftoff and the first phase of flight. No anomalies were seen and, according to initial recorded data, the performance met expectations. A full analysis of these test results and inspection of all components will confirm readiness of this motor for the debut launch of Ariane 6.
“This firing of the P120C motor paves the way for its use on Ariane 6. It is proof of the hard work and dedication of all the teams involved who have made this test possible despite the COVID-19 crisis. This accomplishes an important milestone towards flight,” commented Stefano Bianchi, Head of Space Transportation Development at ESA.

Avio in Italy built this motor case in one piece by winding carbon-fibre composite for a strong and rigid lightweight shell casing. ArianeGroup in France developed the advanced P120C nozzle, while Nammo in Norway provided the igniter. The propellant was cast by Regulus in French Guiana. Advanced manufacturing techniques have been incorporated by Europropulsion in horizontal robotic integration of the nozzle too. Efficient production methods have shortened production cycles and optimised costs.
Europropulsion built three models of the P120C for testing: a development model (DM) configured for Vega-C; a first qualification model (QM1) also configured for Vega-C; and a second qualification model (QM2) configured for Ariane 6.
This hot firing of QM2 is the third and final test of the P120C. It follows the test of the development model in July 2018 and the first qualification model in January 2019.
The test stand was modified with some specific mechanical and avionics adaptations for the Ariane 6 configuration. This test aimed to observe increased performance characterised by a higher burning rate in a shorter combustion time than in the DM and QM1 motors.
The environmental impacts of every P120C test are measured in a similar way to any launch. Air quality and water pollution are checked in real time around the test bench, in the cities of Kourou and Sinnamary, and at launch observation sites. The measurements are then analysed by the Institut Pasteur.
All measurements on this test so far, indicate an extremely low impact on the ecosystem. This is also thanks to the strict meteorological constraints on wind speed at sea level and at certain altitudes, and the required absence of rain.
Completion of this test is an important achievement and maintains the development schedule for Ariane 6 and Vega-C. The ‘Ground Qualification Review 2’ of all the data collected will finally confirm this motor is qualified for use on Ariane 6.
Ariane 6 will extend Europe’s capabilities to independently access space and offer more opportunities for the commercial and institutional market worldwide while reducing costs.
ESA, France’s CNES space agency, and Europropulsion which is jointly owned by Avio and ArianeGroup, collaborated on this test.

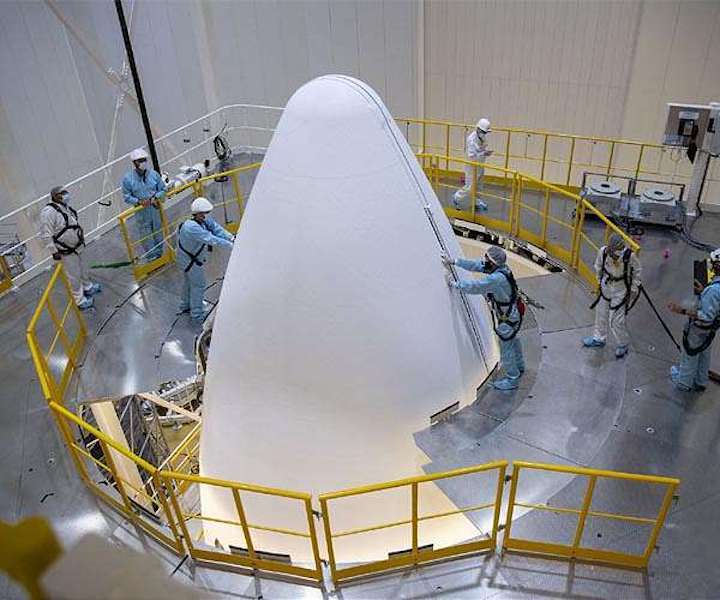
Europe's Spaceport in French Guiana is performing the first combined test in preparation for the inaugural flight of Ariane 6, Europe's new generation launch vehicle.
This test confirms the operations and electrical and mechanical equipment required for integration of the upper part of the launch vehicle. The procedures are carried out in conditions representative of a launch campaign. A major step of this test involves the closure of the Ariane 6 fairing around the payload.
Preparations started in May 2021 with a de-risking campaign of the mechanical operations.
The fairing, built by Ruag Space in Switzerland, stands 20 m high and 5.4 m in diameter. It protects payloads from the thermal, acoustic and aerodynamic stresses on the ascent to space.
This combined test was performed using a new integration dock, composed of a large white frame, with two mobile platforms adjustable to any level and accessible by fixed stairs and platforms, developed by the French space agency, CNES.
The assembly building has two halls: one for integration of the fairing and another where the payload is stowed in the fairing. This encapsulation area is a spacious clean room for Ariane 6.
These activities are part of extensive 'combined tests' at the Spaceport by ESA, CNES, ArianeGroup and other industry partners. They will prove the systems and procedures to prepare Europe's new Ariane 6 launch vehicle for flight.
ESA oversees the implementation and management of verification and qualification activities up to and including the first flight of Ariane 6 before handing over to the exploitation authority.
Ariane 6 is designed to extend guaranteed access to space for Europe and will be capable of carrying out all types of missions to all orbits. It features a modular design with two versions: Ariane 62, fitted with two strap-on boosters, and Ariane 64, with four.
Quelle: SD
----
Update: 30.09.2021
.
Ariane 6 launch complex inaugurated at Europe’s Spaceport
The new launch complex built for Europe’s upcoming Ariane 6 rocket is inaugurated at Europe’s Spaceport in French Guiana.
With this, ESA celebrates another important milestone in the Ariane 6 roadmap as it forges ahead with combined tests between launch vehicle and launch base and preparations towards the first launch campaign.
Clearly visible from space, the facilities feature remarkable complex structures above and below ground specially designed to support Ariane 6 launches into the next decade. It is the proud achievement of the French space agency, CNES – prime contractor to ESA for the development of the launch base, and its European industry partners.

The Ariane 6 programme is funded and developed by ESA. This new launch vehicle will replace Europe’s heavy-lift Ariane 5. Available in two versions, with either two or four boosters, Ariane 6 will offer more performance and flexibility than its predecessor. This opens new opportunities and guarantees continued access to space for ESA Member States.
The Ariane 6 launch complex is a marvel of engineering, designed to optimise the launch system performance and operations workflow. Its design benefits from lessons learned in the construction and operation of the existing Ariane, Vega and Soyuz launch complexes at the spaceport.
The main elements include the launch pad with two exhaust ducts, the mobile gantry and the launch vehicle assembly building.
The launch pad is 28.5 m deep and 200 m wide. Its basic structure was poured in concrete the volume of 67 Olympic-sized swimming pools. At its centre is the launch table which weighs 700 tonnes and is 4 m high, 20 m long, and 18 m wide. This structure was built in Europe by MT Aerospace in Germany and shipped to Kourou for integration on the launch pad. Below ground it protects a host of support systems and will bear the weight of Ariane 6.
Ariane 6’s final integration will take place inside a mobile gantry, just like Soyuz and Vega. The mobile gantry was manufactured in Europe by Eiffage Metal in Germany and was assembled at the spaceport. It will protect Ariane 6 on the launch table during each launch campaign.

This 90 m-high by 50 m-wide gantry weighs 8200 t – more than a thousand tonnes heavier than France's Eiffel Tower. Work platforms will enable engineers to access the vehicle levels to vertically position Ariane 6’s central core directly on the launch table, add two or four boosters depending on the launch configuration, and integrate the fairing that houses the payload. The gantry retracts 140 m on rails before launch. If the launch is delayed the gantry can be rolled back in place to allow access to Ariane 6 before its next launch attempt.

The Ariane 6 core and upper stages will be integrated horizontally inside the launch vehicle assembly building and prepared for rollout to the launch zone. The building is 20 m tall, 112 m long and 41 m wide, some 1 km from the launch zone.
Horizontal integration lowers the cost of facilities and launcher integration while offering a higher level of flexibility and growth potential and allowing easier access to the whole rocket. Overall, the improved Ariane 6 approach to integration and operations will reduce the duration of a launch campaign from months to weeks.
ESA’s contract with CNES for the launch base development worth €600 million was signed in 2015. CNES allocated a third of this funding to infrastructure with notable involvement of local industry for construction, materials and equipment, and the remainder to contracts in mainland Europe.
The systems that are part of the main launch complex structures are being qualified. For example, the deluge system which will protect Ariane 6 and ground installations from the acoustic energy created at liftoff was tested. The disconnection of the fluidic systems for Ariane 6 on the launch pad, tested in France, are now being tested on the launch pad. A central core mockup was used to test ground equipment and practise the manoeuvres involved in a launch campaign. France’s space agency (CNES) and ArianeGroup teams jointly performed these tests under the responsibility of ESA.
Further combined tests between launcher and launch base are under way.

“The Ariane 6 launch complex is a remarkable achievement and an icon of European cooperation and advancement. It represents a vital part of a programme of intense activity at Europe’s Spaceport to prepare for the first flight of ESA’s next generation launch vehicle,” commented Daniel Neuenschwander, ESA Director of Space Transportation.
The inauguration was held in the presence of Sébastien Lecornu, French Minister of the Overseas, Philippe Baptiste, President Director General of CNES, and Daniel Neuenschwander, ESA Director of Space Transportation. Also present were industry partners André-Hubert Roussel, CEO of ArianeGroup, Stéphane Israël, CEO of Arianespace, and Gabriel Serville, President of the Territorial Collectivity of French Guiana.
Quelle: ESA
----
Update: 31.10.2021
.
Ariane 6 undergoing preparations for its 2022 debut
ArianeGroup and the European Space Agency are carrying out preparations for the maiden launch of the Ariane 6 rocket next year. Ariane 6 represents the next generation of the Ariane family of rockets, intended to allow its customers lower-cost access to space. The rocket and launch pad still have an extensive test program ahead of them, with a current target launch date in the second half of 2022.
Ariane 6 is the sixth member of the Ariane family of rockets, whose development began in the 1970s to allow the ESA (European Space Agency) to place its own satellites–and commercial payloads–into geostationary orbit. From 1979 to 2003, the Ariane 1, 2, 3 and 4 rockets launched 144 times with 137 successes.
In 1996, the first Ariane 5 G rocket was launched. This introduced a new design using a cryogenic-fuel first stage, burning liquid hydrogen and liquid oxygen, a storable liquid-propellant second stage and two large SRBs (solid rocket boosters). By the time Ariane 4 was retired in 2003, Ariane 5 had taken over as the primary launch vehicle for ESA and Arianespace.
The Ariane 5 has launched 111 times to date, completing 106 missions successfully with two failures and three partial failures. Several variants of the rocket have been built, with the Ariane 5 ECA, first flown in 2002, introducing more powerful boosters, an upgraded first stage, and a completely new cryogenic upper stage.
Cryogenic propellants–also known as hydrolox–are more efficient and environmentally friendly than the hypergolic propellants used on the previous upper stage. As a result of its enhancements, the ECA variant significantly increased Ariane’s payload capacity.
While early issues with the Ariane 5 ECA were worked out, upgraded versions of the Ariane 5 G were brought into service–the G+ having a stretched version of the original upper stage, and the GS adding the more powerful boosters that had been developed for the ECA. A later version, Ariane 5 ES, would pair the upper stage of the GS with the lower stages of the ECA to deliver Automated Transfer Vehicles to the International Space Station and deploy clusters of Galileo navigation satellites.

Ariane 5 ECA launches the Eutelsat Konnect and GSAT-30 communications satellites – via Arianespace
Today, all of the versions of Ariane 5 that used the storable propellant upper stage have been retired, leaving only the Ariane 5 ECA+ (an upgraded version of the ECA) in service. Ariane 5 is mostly used for launches to GTO (geostationary transfer orbit), often carrying two communications satellites at a time. It has also flown missions to low Earth orbit and other trajectories–such as the upcoming launch of the James Webb Space Telescope towards the Earth-Sun L2 Lagrange point.
In its ECA+ configuration, Ariane 5 has carried payloads of up to 11.2 tonnes to GTO, but it is not capable of placing satellites directly into geostationary orbit as its second stage’s HM-7B engine cannot be restarted in flight. As a result, it can make a single burn to reach the transfer orbit, but cannot fire again to circularize the orbit when it reaches apogee. At over 25 years old, the rocket is also becoming increasingly costly to operate.
The Ariane 6 program was started as a way to replace the Ariane 5 with a simpler, cheaper, and more flexible vehicle. Like its predecessor, Ariane 6 will use a large hydrolox core stage, with a second stage that also burns cryogenic propellant. During the early stages of flight, Ariane 6 will utilize two or four large P120C (P120 Common) solid rocket boosters. When flying with two booters, the rocket will be designated Ariane 62, while the version with four boosters will be called the Ariane 64.
The P120C motors are a brand-new set of SRBs made to replace the P80, currently used on Arianespace’s smaller Vega rocket. The P120C measures 13.5 meters long and 2.4 meters in diameter, using a carbon composite casing built by Italy’s Avio. At launch, the P120C will generate approximately 4,500 kN of thrust, making the motor the largest and most powerful single-segment solid rocket motor ever flown.

First hot-fire test of the P120C motor – via ESA
To complete its certification for flight, P120C completed three hot-fire tests at the Guiana Space Center in Kourou. In July 2018, the first hot-fire test was conducted with DM1 (development model No.1). The second hot-fire test was completed in January 2019 using QM1 (qualification model No.1).
A third and final test was conducted in October 2020 using QM2. The QM1 test used a booster configured as the first stage of the upcoming Vega-C rocket, while QM2 was tested in the configuration that will be used on the Ariane 6. With all three firings completed successfully, ESA certified the booster for use on both the Ariane 6 and Vega-C vehicles.
The first stage of the Ariane 6, known as the LLPM (Lower Liquid Propulsion Module), has a diameter of 5.4 meters–the same as the core stage of Ariane 5. It uses a single Vulcain 2.1 engine, derived from the Vulcain 2 engine used on the Ariane 5 ECA.
The Vulcain 2.1 will generate 1,371 kilonewtons of thrust to propel the Ariane 6 for the first eight to ten minutes of flight. The engine will be a gas-generator combustion cycle, similar to the Aerojet Rocketdyne RS-68A engine used on the US Delta IV rocket.

Static fire test of the Vulcain 2.1. – via ESA
Vulcain 2.1 will use a 3D-printed gas generator with a redesigned and simplified nozzle. Its combustion chamber will be ignited from the ground via the bottom of the nozzle, instead of using pyrotechnic devices, which reduce the cost and weight of the engine. Heated oxygen from the exhaust lines will be used to pressurize the first stage propellant tanks instead of the rocket carrying liquid helium for this purpose as on Ariane 5.
These changes are expected to lower the cost of Vulcain 2.1 compared to Vulcain 2, without compromising the exceptional reliability that Vulcain 2 has achieved on the Ariane 5. The DLR (German Aerospace Center) undertook testing of the new engine beginning in January 2018, with final qualification achieved in July 2019. These tests fired Vulcain 2.1 for durations of up to 11 minutes to ensure that it would perform as expected throughout its flight.
Combined with the SRBs for the first minutes of the launch, the LLPM will carry the second stage to an altitude of around 200 kilometers and close to orbital velocity. From here, the second stage will separate to continue pushing its payload towards its target orbit or orbits.
The second stage, or ULPM (Upper Liquid Propulsion Module), uses the Vinci hydrolox engine. Vinci will generate 180 kilonewtons of thrust with a specific impulse of 457 seconds. The engine will use an extended nozzle to increase its performance and features an APU (Auxiliary Power Unit) to help pressurize and settle the propellant tanks, and to produce small amounts of thrust–for example, to help with the spacing of satellites that separate in clusters.
Unlike its predecessor, the HM-7B, Vinci will use an expander cycle where propellant is circulated to cool the combustion chamber and then drive the turbopump as it heats up and expands, before it is finally fed into the engine. Vinci will have the ability to reignite up to three times, allowing for on-orbit maneuvering and a deorbit burn at the end of the mission.

Ariane 6’s upper stage in flight – via Mack Crawford for NSF/L2
The Vinci engine has undergone a long and extensive test program. The first test started in May 2005 under the Ariane 5 Plus program, an ultimately abandoned plan for a mid-life upgrade of the Ariane 5. During the test program, the engine underwent 148 tests and was fired for a total of 52,156 seconds. The final qualification test took place in October 2018.
The second stage itself has started undergoing final ground testing in preparations for launch, including an umbilical separation test, ensuring that the connections between the rocket and its launch pad sever as expected when the vehicle lifts off.
The completed Ariane 6 rocket will be 5.4 meters in diameter and approximately 60 meters tall. A 5.4-meter diameter payload fairing will be mounted atop the second stage to protect the payload during the ascent through the atmosphere. This is a two-piece, or bisector, carbon-fiber composite structure made by Ruag Space.
Two different lengths of fairing will be used: both the Ariane 62 and 64 will be able to fly with a 20-meter long version, while a shorter a 14-meter fairing will also be available for the Ariane 62.
The first 20-meter long payload fairing was delivered to the Guiana Space Center in 2021. The two halves were lifted on top of a payload adaptor with a mock satellite to conduct a combined test. This test, which was completed in September, investigated how the fairings would handle the stresses of a launch.
Alongside the development of Ariane 6, a new launch complex is also under construction to support the rocket. ELA-4 (Ensemble de Lancement Ariane 4) will consist of three main structures in support of Ariane 6: an integration building, mobile gantry, and the launch pad itself.
The first stage and second stage will be integrated within the LVAB (Launch Vehicle Assembly Building), located about one kilometer away from the pad. The rocket will be assembled in a horizontal orientation, with the LVAB providing space for the preparations required before launch. The building will be 20 meters tall, 112 meters long, and 41 meters wide.
Once assembled, the rocket will be moved from the LVAB to the launch pad, where it will be enclosed in the mobile gantry.
Ariane 6 will sit upon a 700-tonne steel launch table, which will support the rocket and provide two main umbilical connectors to fuel the first stage. An umbilical tower will provide the rocket’s upper stage with fuel and electricity before launch. The tower will be connected to the second stage of Ariane 6 via two arms, which will separate at liftoff. Once the arms retract, large doors will close to protect the equipment from the exhaust as Ariane climbs past.
A flame trench under the launch pad will be used to divert the plumes created by the rocket at liftoff down two ducts, with a water deluge system activating shortly before launch to help dampen sound and vibrations. This was tested in April.
Four lightning protection masts around the launch pad will help to protect it in the event of thunderstorms.

Rendering of Ariane 62 on its launch pad – via ESA
The pad’s mobile gantry will be used to support final assembly, testing, and preparations for launch, including integration of the payload with the Ariane 6 rocket. The gantry will also serve to protect the rocket and payload from the elements, and provide engineers with easy access to the rocket if a launch is delayed and inspections or minor repairs are required. The gantry is 90 meters tall with a metallic structure weighing over 8,200 tonnes.
The gantry can move between the launch pad and a parked position 140 meters away, which it will occupy when Ariane 6 is launched. It was first moved 97 meters in July 2019 while the pad was under construction, and testing has continued as construction of the pad and the gantry has proceeded.
With construction of the launch site now completed, testing has begun to ensure the complex works as a whole. This testing has included fit checks with mockups for the P120C motors, and in October 2020, a mockup of the Ariane 6 LLPM and two mockup P120Cs were stacked on top of the launch table for the first time.
For its maiden flight, Ariane 6 will fly in the Ariane 62 configuration, with a pair of solid rocket boosters. This configuration will be able to lift a payload of up to 10,300 kg to LEO (low Earth orbit), and up to 5,000 kg to GTO (geostationary transfer orbit), although for the maiden flight Ariane is not expected to carry a functional payload. The Ariane 64, with its four boosters, will be able to lift 21,600 kg to LEO, approximately 11,500 kg to GTO, and about 5,000 kg directly into GEO (geostationary orbit).

Ariane 6 Lifted off – via Mack Crawford for NSF
This large range of payload capabilities will allow Ariane 6 to place nearly any satellite into nearly any orbit. Like Ariane 5, the Ariane 6 will have the ability to carry two large satellites to GTO. However, with its new Vinci engine, Ariane 6 will be the first member of the Ariane family to be able to take a satellite directly to GEO.
Through Arianespace’s MSL (Multi-launch Service) program, Ariane 6 will also be able to provide for small satellites under 400 kg in mass to launch as secondary payloads in piggyback or rideshare missions. This is similar to the SSMS (Small Spacecraft Mission Service) that Arianespace already offers on its smaller Vega rocket, allowing the rideshare of multiple small satellites to anywhere in LEO. MLS will expand this offering to geostationary orbit and missions to the Moon and beyond.
In the future, Arianespace plans to offer a three-stage version of Ariane 6 with an optional kick stage called Astris. This will be used to interface directly with the payload and deliver it to its final orbit. The Astris can be used in place of built-in propulsion capabilities on some payloads–for example, by raising a satellite from geostationary transfer to geostationary orbit. The stage can also be used to provide an additional boost to payloads bound for destinations beyond Earth orbit, or to allow multiple payloads to be delivered into different orbits during an LEO mission.
The Astris stage will be powered by a Berta engine. Berta is a mid-size storable propellant engine that can be reignited several times. This kick stage can be used for an extended period of time. Astris is expected to make its first launch when an Ariane 64 deploys the European Space Agency’s Hera planetary defense demonstration mission in 2024.

Ariane 64 and Vega C – via ESA
Ariane 6 is currently expected to make its debut in the second half of 2022. Also in 2022, ArianeGroup’s Vega-C rocket is expected to take its maiden flight with the LARES-2 (Laser Relativity Satellite 2) payload aboard. This rocket will use the same P120C solid rocket motor to be flown on Ariane 6 as its first stage and will replace the version of the Vega rocket that is currently in service.
Arianespace currently has six remaining Ariane 5 rockets to launch before it transitions fully to the Ariane 6. The new rocket already has several launches on its books, including the Hera mission and MLS rideshares. It has also been selected to launch one of the ViaSat-3 satellites, Intelsat’s Galaxy 37 spacecraft, and satellites for the Galileo navigation constellation.
(Lead image: Rendering of Ariane 64 on the launchpad – via ESA)
Quelle: NS