10.08.2018
NASA TESTS FLIGHT RECORDERS AHEAD OF ORION ABORT TEST
This is an artist's concept of the attitude control motor in operation during an abort. Photo: NASA
NASA engineers spent Wednesday dropping six flight data recorders into the Atlantic Ocean from a helicopter 5,000 feet up.
They’re testing a system that will help keep deep space astronauts safe.
If something goes wrong during a launch of NASA’s Orion space capsule, powerful engines on top of the vehicle will fire, pulling it to safety.
Engineers are planning a critical test of that system next year where they will rely on twelve tiny flight recorders small enough to fit in your hand to provide data to engineers.
The Orion program’s Christina Rojdev says about 20 people were involved in the drop test of the equipment from Kennedy Space Center “making sure it can survive the impact loads when it lands in the water and making sure our beacons work and we can find them.”
Orion’s David Petri said the drop test was a success and is ready for a larger test, called the Ascent Abort 2 (AA-2) next year.
“[The test is] going to allow us to refine that concept to make sure we recover all of our data recorders, because the most importing thing about the AA-2 mission is the data.”
The drop test comes ahead of an in-flight abort test of the system, scheduled for April 2019 from Cape Canaveral.
Quelle: 90.7 WMFE
---
Update: 14.08.2018
.
Digging into the details of Orion’s EM-1 test flight
As NASA continues to analyze and refine the profile for the Exploration Mission-1 (EM-1) test flight, more information about the multi-week mission is beginning to be detailed. The Orion spacecraft will fly into orbit around the Moon before returning to Earth in a shakedown mission before the first crew flies in Orion on Exploration Mission-2 (EM-2).
EM-1 will be the first flight of Orion’s European Service Module, also pairing it with the Crew Module for the first time, with hundreds of test objectives to be evaluated during the mission.
Orion will fly on EM-1 for the first time with all of its primary spacecraft elements. The European Service Module (ESM) will make its first flight, connected to the second crew module (CM) unit by a crew module adapter (CMA) making its first flight.
The integrated spacecraft will be tested on a multi-week flight to a Distant Retrograde Orbit (DRO) around the Moon and back. “The missions are either 26-27 days or they’re going to be 38 to 42 days and there’s nothing in between,” Nujoud Merancy, Exploration Mission Analysis Lead at NASA’s Johnson Space Center, said in an interview with NASASpaceflight.com. “The difference is the DRO orbit is a twelve-day period, so one lap around the Moon takes twelve days.”
“In a short mission you’re only there for half an orbit so you enter sort of in front of the Moon and you depart from behind it so you’ve only gone halfway around,” she explained. “For the long mission then you stay for another orbit, so you’ll do one and a half times around the Moon with the long class.”
The long class mission duration was added to provide the required lighting conditions for landing and recovery for any time of the year. The ESM will provide the CM with the power and consumables to fly crew for as much as three weeks and without crew for over half a year. “We’re certifying this vehicle for those 40 days but the Orion requirements are 21 crewed days and 210 uncrewed days, so in theory the mission could be 231 days within our requirements base,” Merancy noted.
Without a crew on board, NASA and prime contractor Lockheed Martin will take the opportunity to exercise the other vehicle subsystems for possibly up to six weeks, but the mission duration won’t stress the overall requirements.
“Once you take the people out it’s really a matter of how much prop (propellant) are you using and if all you’re doing is attitude control you really don’t burn prop very quickly or if you were docked to the LOP-G (the proposed Lunar Gateway), then we’re not even using our attitude control system so you could just be there for a long time,” she said.
“So uncrewed there’s not a whole lot of limitations, it’s now valve seals and things like that. The lifetime certification should be over 200 days for the vehicle.”
“That’s why when we switched from the [short duration only mission] to the include the long class on this one it wasn’t really that it was stressing anything,” she added. “People have to go back and make sure their systems are all still good, but it was a pretty easy change to insert for the mission because when it’s uncrewed there’s not much difference in the vehicle operation.”
Merancy noted that Lockheed has done studies in the past looking at how to fly Orion for 1000 days. “There’s only like a few things you change and it’s really like changing out a few seals,” she explained. “If you want a thousand day vehicle then you can’t have even the minor leakage that occurs through the hatch seals, you want like a third seal in there, right?”
“So there’s a few things you change, but a thousand-day Orion isn’t much of a difference from a 200-day Orion.”
Orion test flight
EM-1 is a first flight for most of NASA’s current human exploration programs. The Orion crew module is one of the only major elements not making its debut; its first flight was Exploration Flight Test-1 (EFT-1) in late 2014, where it was launched by a Delta IV Heavy booster with mass simulators for the most of the Service Module elements.
Flying on this flight integrated with a Service Module making its debut, this Orion will be carried into orbit by the Space Launch System (SLS) rocket on its first launch. Orion and SLS will also liftoff on EM-1 in the first launch from Exploration Ground Systems’ rebuilt launch operations infrastructure at the Kennedy Space Center in Florida.
NASA and its contractors have been studying and analyzing the EM-1 mission profile for a long time. Early plans were to fly a shorter circumlunar flight test, but it was subsequently decided to use the flight to demonstrate one of the tactical Design Reference Missions (DRM), which is to fly to DRO.
The spacecraft has hundreds of test objectives on EM-1. “We have something like a hundred thirty FTOs, flight test objectives,” Merancy said. “The three big priorities are the lunar velocity heat-shield reentry, the end to end entry sequence, and the in-space demonstration of all the subsystems.”
“The whole flight is to make sure the vehicle works, so pretty much every subsystem has objectives to evaluate after the flight, for how well did it perform. You have really obvious ones like ‘must do main engine burns.’ The nominal mission execution will hit almost every single objective you need, because in order to execute the mission you need to use the main engine and you have to use the power and thermal [systems].”
SLS will first insert Orion and its Interim Cryogenic Propulsion Stage (ICPS) into Earth orbit, followed by ICPS making a long Trans-Lunar Injection (TLI) burn at the end of the first orbit. Separation from the ICPS will largely mark the end of the SLS test flight and the beginning of Orion’s.
Springs will push Orion away from the ICPS about ten minutes after TLI cutoff. The springs will provide some separation velocity between spacecraft and upper stage, but Orion will also fire its auxiliary engines to increase the separation rate after coasting away from ICPS for over a minute.
Orion has had three types of engines on the ESM: reaction control system (RCS) thrusters for attitude control and small translational maneuvers, auxiliary (Aux) engines for most translational maneuvers, and an Orbital Maneuvering System engine (OMS-E) for large translational burns.
If necessary, there are multiple opportunities for Orion to make outbound trajectory correction (OTC) maneuvers on the way to the Moon; on its first flight, the plan is to use the first opportunity a few hours after TLI to test-fire the OMS-E.
“[For] the first outbound trajectory correction we’re going to do an OMS Check-Out/OCO burn because in all likelihood the burn you need for the correction would be so small you don’t need to use the OMS,” Merancy explained. “It’s likely you’d do it on Aux and it’d just be a little correction for whatever dispersion ICPS drops us off at.”
“That means that the first time you ever use the OMS engine would be on the far side of the Moon when you don’t have comm (communications), so that’s kind of dumb,” she said.
Orion will make a pair of burns with its main engine to enter and leave DRO. Entering, the spacecraft will make that Outbound Powered Flyby (OPF) “far side” burn near closest approach to the Moon at an altitude of around 100 km, which sets up a Distant Retrograde orbit Insertion burn (DRI) around four days later. Orion will leave DRO the opposite way, with a Distant Retrograde orbit Departure (DRD) burn first, setting up a Return Powered Flyby (RPF) burn to return to Earth.
The OCO burn gives the flight control team and the program a chance to evaluate engine performance within the spacecraft system early in the mission. The engine itself is a space veteran, flying on several Space Shuttle missions; however, this is the first time it is integrated with a different spacecraft.
The trajectory might not need to be corrected, so it’s likely almost all of the velocity components of the OCO burn will be out of plane. “We’re going to intentionally do an OMS burn which means it has to be bigger than you need and you’ll just burn in a sort of a null direction,” she explained.
“If you burn perpendicular to the velocity vector it really doesn’t affect the trajectory, so you’ll just put whatever component you need for correction in and then burn a bunch out of plane so you can get a 30-second OMS burn in and confirm that the engine and all the systems are working right there at the beginning of the flight.”
Merancy noted that the minimum burn time for the OMS engine on Orion is five seconds, but it has to run longer than that for the vehicle guidance system. “We’re just sort of doing a wasting burn if you will, so most of it won’t do anything to the mission, but you have to turn on the engine long enough,” she noted.
“To get a whole guidance cycle where it actually closes the loop and calculates it all, that’s 30 seconds so that’s why we’re doing a 30 second burn there.”
Most of the time on the long coast periods outbound to and returning from the Moon, Orion will be in a tail-to-Sun attitude. “Our vehicle design is the tail-to-Sun flight attitude, so that way your arrays get full Sun and the radiators are around the barrel [are] looking at deep space. So that tail-to-Sun is sort of our baseline power/thermal-balanced attitude.”
“Nominally, the vehicle could just sit there in ‘tail to sun’ indefinitely, but we do have other things that you have to do, like the IMUs (Inertial Measurement Units) will need to be aligned and you’ll need to do star-tracker takes and stuff,” she added. “So there will be times you’ll go out of attitude just to get data and align the IMUs, but you’ll just keep going back to tail to sun.”
The spacecraft doesn’t have to hold the coast attitude precisely. “It’s got a big plus or minus 20-degree deadband,” Merancy said.
“You don’t have to hold it that tight. So when you’re sitting tail-to-Sun you can just bounce around in there, because it just drives up your prop quantity [consumption] to hold it really tight and you don’t need to. The arrays can track plenty and you’ve 40 degrees worth of ‘slosh,’ so GNC doesn’t need a tight deadband on that.”
Crew module outfitting
The EM-1 Orion crew module won’t have much in the way of crew systems on this flight, but it will be outfitted with some hardware.
“For this flight I think we have at least one or two seats installed because there is going to be a dummy put in with a radiation vest and stuff like that, so at least some of it will be accurate, but we aren’t putting in the crew displays and we don’t have the ECLSS (Environmental Control and Life Support System) wall installed, which is at sort of the back of the cabin,” Merancy explained.
“That’s not going in this flight. I think the floor panels will be in, and at least two seats I think and a dummy, so there will be some stuff in there, but it still won’t look like the true EM-2 crew vehicle. There will be cameras hard mounted and things like that which wouldn’t be there for EM-2, though.”
There will be opportunities to downlink imagery from spacecraft cameras during the flight, but they will be more limited than Earth-orbiting spacecraft. “I think we get live video, some of it will be fairly low quality,” she said. “I think we get sequential still video and we can downlink high-res pictures.”
Merancy noted that she’s looking forward to pictures taken from outside: “We have cameras on the tips of all the solar arrays, so that means we can take a selfie with the Moon, so that’s going to be the one that I’m waiting for.”
Although live imagery feeds may be limited, a lot of video will be recorded on the vehicle. “There’s a bunch of data recorders on board, so a lot of it is recorded on board and will be pulled off when we land,” she said.
In addition to providing long-term power for CM systems, the ESM design carries crew-related consumables such as cabin atmosphere, but only one of those will be connected to the CM through the CMA on EM-1. “The nitrogen tank — I think that’s the only one that’s hooked up all the way to the CM,” Merancy said.
“There is a nitrogen tank because you will use that if there is a leak to repressurize because the cabin needs the pressure for reentry. They are flying the water tanks, but they’re not plumbed to the CM.”
For launch, the cabin will start with fresh air from the launch site. “It’ll be Florida air when the hatch gets closed,” she said. “I think we have sensors on-board so we can…measure if there’s any cabin leaks in flight and the humidity level and stuff like that, but the humidity level shouldn’t change.”
Orion’s hatch won’t be closed for flight until shortly before or during the launch countdown in order to allow for late configuration of items in the cabin and late stow of experiments. Although there is no crew, the Crew Access Arm on the Mobile Launcher is installed and will be used during the EM-1 launch campaign. “There’s a bunch of late stow items,” Merancy said.
“There’s radiation sensors that are going in…and all that has to be turned on at the last minute. They’re just stowed in there, so there’s no command capability to them. So there is a bunch of late stow [and] a couple of science experiments going in, so at a minimum you need the Crew Access Arm to get to it for those on the pad.”
Most of the ECLSS units won’t fly on Orion until EM-2, but NASA is carrying out ground and flight tests of the other critical systems in preparation for the first crewed flight. “Station has our ECLSS swing bed thing, the whole amine swing bed,” Merancy noted.
“They’ve been doing a demo on orbit for a while now. And they built somewhere around here there’s a test lab where they built up an ECLSS system to start testing it on the ground, so there’s a bunch of mitigations that are being done for the fact that we’re not flying it on EM-1.”
“But the other part of it is that without having a biological person inside the vehicle to use the systems, putting it on there wouldn’t actually test them,” she explained. “So unless you had something like released a CO2 tank you would never know if the swing beds worked even if we had put them on EM-1.”
Quelle: NS
---
Update: 16.08.2018
.
Engine test for NASA’s heavy-lift SLS rocket cuts off early, but achieves goals
News Brief: NASA put a developmental model of the RS-25 engine for its heavy-lift Space Launch System rocket through a hot-fire test today at Stennis Space Center in Mississippi, with NASA Administrator Jim Bridenstine in attendance. Although the test firing ended at 319 seconds rather than the originally planned 500 seconds, officials said the test achieved all its planned objectives. NASASpaceflight.com quoted sources as saying that the premature cutoff was due to a liquid hydrogen transfer issue at the facility, rather than any problem with the engine itself. The SLS’ first flights will use engines left over from the space shuttle program, and newly built Aerojet Rocketdyne RS-25 engines are to be delivered in the 2020s.
Quelle: GeekWire
---
Update. 17.08.2018
.
Boeing team challenges focusing SLS Engine Section work
The Boeing team is working to finish the integration of the first engine section element of NASA’s Space Launch System (SLS) Core Stage by focusing its efforts in short-term team challenges. Boeing management recently challenged the team at Michoud Assembly Facility (MAF) in New Orleans to complete packages of major work items within a few weeks. They are currently beating or meeting those deadlines as the Core Stage prime contractor aims to hold to a late Fall completion date for the element.
The engine section is the pacing item in the schedule for completing Core Stage-1 (CS-1), the first flight vehicle which will fly on Exploration Mission-1 (EM-1).
While the team challenges resulted in a series of major hardware installations inside and outside the engine section, welding tubes and testing wiring also continues.
Engine section team challenges
Boeing continues to work around-the-clock shifts on the element, looking to make up time lost in the first half of the year after recovering from the tubing contamination discovered in February. Tubing that is being installed in the compartment was not fully cleaned by the supplier as required prior to delivery to MAF.

The +Z side of the CS-1 engine section surrounded by scaffolding and clean room ventilation hoses on August 13. The light brown areas are cork panels that will eventually cover most of the outside. Credit: Philip Sloss for NSF/L2.
Management is looking for ways to pick up and maintain a higher level of productivity and gave the engine section team a challenge in mid-June. They gave the team two weeks to lift all five of the large composite overwrapped pressure vessel (COPV) gaseous helium tanks, four thrust vector control (TVC) platforms, and the outfitted avionics bay shelf into the engine section and install them.
“This whole area [outside the engine section] was populated with five helium tanks, and four platforms, and an AV (avionics) bay, and we came in two weeks ago and said look, we want to fly all that stuff in and assemble it,” John Shannon, Boeing’s SLS Vice President and Program Manager said in July. “And they were like: ‘what?'”
“The team, they just pulled together and they got it done — three days early, too,” he added. “They did all that work, put the platforms in, [and] took one NC (non-conformance) for one little drill thing. Just a phenomenal job.”
NASA and Boeing leadership visited MAF in early July to thank the team for its work and serve lunch to the different work shifts. With the uncertainty removed about the sequencing and availability of tubing for installations, Boeing is hoping to maintain the higher pace of work the team demonstrated in that challenge during the last two weeks of June.

The tail service umbilical plates on the +Z side of the engine section. Among several services provided to the vehicle from the ground at the umbilical plates, LOX will be loaded from the left side panel, LH2 from the right. Credit: Philip Sloss for NSF/L2.
“In fact, ten percent of the total build was done in the last two weeks, just based on the amount of installations that we had,” Rick Navarro, Boeing’s Director of Space and Launch Operations, noted at the time. “If we sustain that path, we will be able to be ready for stacking by the late Fall.”
“We’re on a pace that puts us ready for stacking by late Fall,” Navarro said in early July. “Over the last four or five weeks, as we got through all the tube recycling issues and got them all back in the right sequence we’ve picked up the pace dramatically.”
Wiring, feedline installs
Since last month, the team has met similar timed challenges to install dozens of wire harnesses inside the engine compartment and the first of two sections of the liquid oxygen (LOX) feedline that mount to the outside.
“That process will be a temporary initial install,” Steven Ernst, Boeing’s Core Stage Engineering Support Manager, said in early July about the wire harness install challenge. “We won’t be clamping them up, we’ll be tying them off.”
“[We’ll] check all the routing [and] make sure we understand that we’ll do measurements to make sure we have the right-sized clamps, and then as we get the P-clamps installed, they start clamping up the routing.”
Two sixteen-inch diameter LOX feedlines run down the outside of the liquid hydrogen (LH2) tank to the engine section where the propellant enters and is branched out to each of the four RS-25 engines in the Core Stage. The section of LOX feedline was installed on the -Z side of the engine section on the side where the systems tunnel will be, and opposite the T-0 umbilical plates on the +Z side.
The ends of the section are bolted flanges that will have to precisely line up with other sections of the propellant line.
“Siting of this is extremely critical because the mating surface of the downcomer is a datum that you have to align around on the upper flange,” Ernst said in a follow-up interview on August 15.

CS-1 engine section in late February, better showing the reaction beams (upper left center) that will eventually surround the +Z LOX downcomer. The outside pockets can be seen on the right beam; those will eventually be filled in with spray-on foam insulation (SOFI). Credit: Philip Sloss for NSF/L2.
“Conversely on the feedlines you [have] to do things on the other side of the mate so that when you bring these together eventually they all align.” The section is an elbow, with the bottom flange inside the barrel.
The assembly also has a plate that wraps around the propellant line and is attached to the outside of the engine section on either side of the line. “We have to align, not only for that upper flange, but for the flange inside,” Ernst said. “You go through and you laser shoot these in and then we match drill the holes [to the outside].”
The propellant line is also connected to reaction structure beams on the outside of the engine section. In contrast to most of the engine section which will be covered with cork panels and white paint, the beams and structure associated with the LOX downcomers will be closed out with spray-on foam insulation (SOFI).
“Those are actually pocketed beams,” Michael Alldredge, NASA SLS Core Stage TPS Team Lead, noted. Ernst said that the mirror image downcomer section for the +Z side is completing its offline TPS work and then it will also be installed.
Orbital tube welding ongoing
The engine section is even more densely packed on the inside than other areas on the stage when complete, so most of the work inside was planned to be installed in strict sequences.
“We have to be very selective of when we put big components in because you’re going to close yourself from accessing to other areas,” Navarro said. “All those miles of tubing and all those [wire] harnesses, we have to do them in layers, because once we put in a big piece of ducting you pretty much can’t get back in there.”

NASA Administrator views the inside of the CS-1 engine section from its top work platform at MAF during his tour of the facility on August 13. Marshall Space Flight Center director Jody Singer is to his right. Credit: NASA/Jude Guidry.
“We planned it out by zones and we know we need to put this in before this and this after this,” Ernst added. “There’s been a lot of effort put into that planning.”
A lot of the tubing is going into the engine section, which requires a lot of welding inside. “We have approximately 250 to 260 orbital tube welded connections we have to make,” Navarro noted in early July. “These are not the mechanical fasteners, these are actual orbital tube welds. We just passed the hundred-mark on orbital tube welds, so we’re reaching the halfway mark in the total weld jobs.”
“We have picked up the pace significantly in welding, so we’re able to handle up to seven welds in a day if we need to,” he added. “So now it’s a race to finish the remaining hundred-plus welds, [and] connect all the systems.”
Ernst noted that in contrast to the big propellant lines that have bolted flanges, orbital tube welding makes for a reliable connection for things like the smaller high-pressure lines.
In an update at the time of the interview on August 15, Ernst also noted that they have now passed the 50 percent mark with orbital tube welding inside the engine section.
Quelle: NS
---
Update: 21.08.2018
.
Heat Shield Install Brings Orion Spacecraft Closer to Space
Lockheed Martin engineers and technicians check fittings during installation of the heat shield to the Orion crew module July 25, 2018, inside the Neil Armstrong Operations and Checkout Building high bay at NASA's Kennedy Space Center in Florida. Orion is being prepared for Exploration Mission-1 (EM-1), the first unscrewed integrated flight test atop NASA's Space Launch System rocket. The heat shield will need to withstand temperatures of up to 5,000 degrees Fahrenheit during Orion's descent and re-entry through the Earth's atmosphere before it splashes down in the Pacific Ocean. Photo credit: NASA/Kim Shiflett
-
During Exploration Mission-1 (EM-1), an uncrewed Orion spacecraft will launch atop NASA's Space Launch System rocket and begin a three-week voyage in space, taking it about 40,000 miles beyond the Moon and back to Earth. On its return, the spacecraft's heat shield will need to withstand temperatures of nearing 5,000 degrees Fahrenheit during its fiery re-entry through the Earth’s atmosphere before it splashes down in the Pacific Ocean.
Technicians at NASA's Kennedy Space Center (KSC) in Florida recently secured the heat shield to the bottom of the crew module, using 68 bolts. Designed and manufactured by Orion prime contractor, Lockheed Martin, the heat shield is like an intricate puzzle with pieces that all have to fit together perfectly. Before the final installation, a fit check was performed to ensure all of the bolt fittings lined up.
"Installation of the EM-1 crew module heat shield is a significant milestone representing the beginning of closing out the crew module assembly," said Jules Schneider, Lockheed Martin Orion senior manager for KSC Operations. "When the heat shield is installed, access to components becomes more difficult, and in some cases there is no more access. So by installing the heat shield you are declaring that a certain percentage of the spacecraft is finished."
Measuring 16.5 feet in diameter, Orion's new heat shield is the largest of its kind developed for missions that will carry astronauts. The heat shield base structure has a titanium truss covered with a composite substrate, or a skin composed of layers of carbon fiber material.
In a new process, several large blocks of an ablative material called Avcoat, licensed from Boston-based Textron Systems, were produced at Michoud Assembly Facility in New Orleans by Lockheed Martin. They were shipped to Kennedy, where Lockheed Martin technicians machined them into more than 180 unique blocks and bonded them to the heat shield's surface.
To fill tiny gaps between the blocks, the seams were filled with a mixture that over time will become solid. Technicians applied a coat of white epoxy paint to the heat shield's surface and then applied aluminized tape after the painted surface dried. The tape provides surface resistivity, and absorbs solar heat and infrared emissions.
"Witnessing assembly, test and installation of the EM-1 crew module heat shield brought an appreciation for its innovative design and assembly techniques," said Amy Marasia, the Crew Module Assembly operations lead in NASA's Orion Production Operations.
While Avcoat isn’t new to spacecraft – it was used on the heat shields of Apollo and the Orion Exploration Flight Test-1 – the technique of using blocks instead of injecting the ablative material is proving to be a real production time-saver.
"A benefit of switching from the honeycomb system to the blocks is we now can make the Avcoat blocks at the same time that the Orion structure is being made, and when the module is ready we can secure the blocks, which saves time," said John Kowal, NASA Orion Thermal Protection System manager at Johnson Space Center in Houston. "Before, with EFT-1, we had to wait for the carrier portion to be done, and then apply the Avcoat directly to the crew module."
During its first mission around the Moon, engineers will monitor how Orion’s systems perform in the environment of deep space and its return to Earth. During re-entry the ablative material of the Avcoat blocks will burn away, essentially carrying the heat away from Orion because of the gases created during the ablative process.
Orion is the exploration spacecraft that will carry astronauts to deep-space destinations, including the Moon and on to Mars. Orion will be equipped with power, communications and life support systems to sustain space travelers during their long-duration missions and return them safely to Earth.
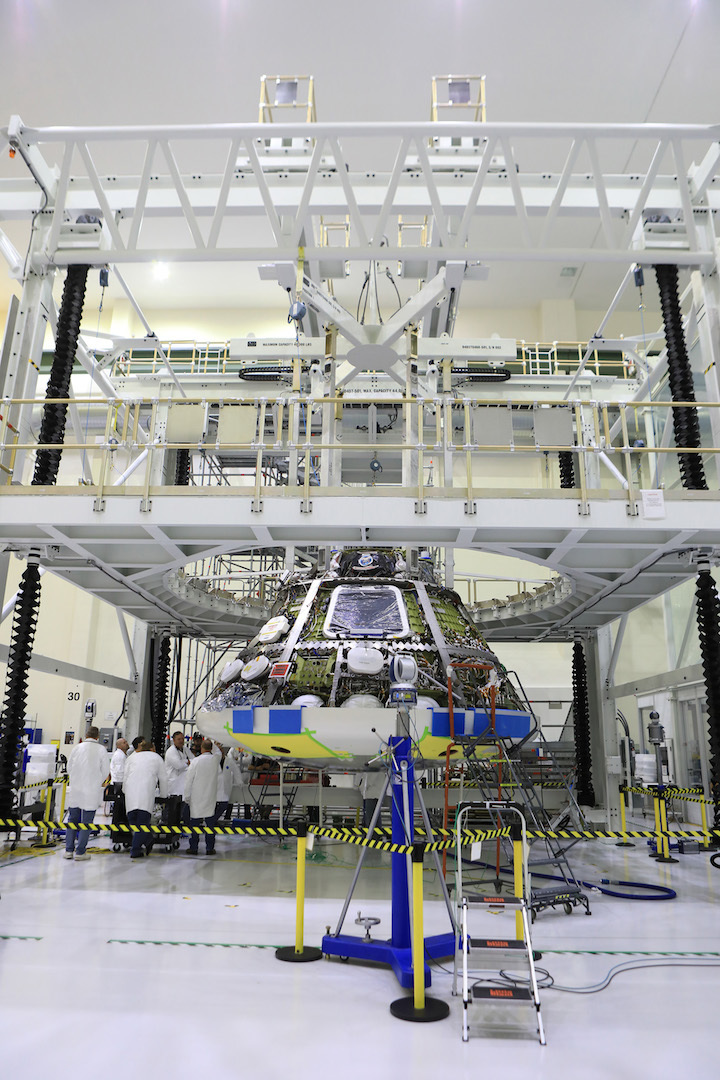
Orion elements coming together for EM-1
At a recent media event, NASA’s Orion Program Manager provided a brief update on development and preparations for Exploration Mission-1 (EM-1). Mark Kirasich ran through some of the current status of the EM-1 spacecraft elements that, once assembled and checked out, will make the cislunar test flight currently forecast for mid-2020.
The three-to-six week EM-1 lunar orbit mission will exercise most of Orion’s systems together for the first time, with the exceptions of a live Launch Abort System (LAS) and Environmental Control and Life Support Systems (ECLSS).
Preparations for EM-1 are nearing the major milestone of the first European Service Module (ESM) being shipped to the Kennedy Space Center (KSC), but NASA and its contractors still have work to complete with the ESM and the Crew Module (CM) and issues to work out before the first deep-space Orion spacecraft can be put together early next year in Florida.
Orion EM-1 status
EM-1 is a first flight for most of NASA’s current human exploration programs. Orion will be flying for the first time with a live Service Module, enabling the multi-week flight into a Distant Retrograde Orbit (DRO) around the Moon. The spacecraft will be flying on top of the Space Launch System (SLS) booster’s first flight, which will also be the first launch from Exploration Ground Systems’ rebuilt launch operations infrastructure at KSC.